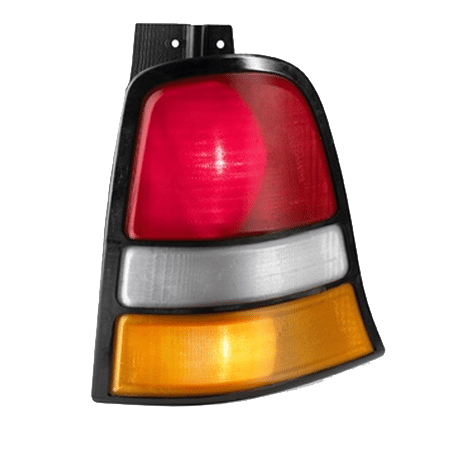
Print translucent parts in standard thermoplastic
Use FDM 3D printing technology to print translucent prototypes in various thermoplastic colours.
Overview
ABSi allows manufacturers to create concept models and functional prototypes that resemble a final product without the need for costly outsourcing. Expand the 3D printing experience beyond opaque parts with ABSi material that allows for light transmission. This material is especially useful in industries such as automotive, aerospace, and medical-device manufacturing.
Material Performance
Its strength is superior to standard ABS, and the translucent nature of ABSi is beneficial for monitoring material flow and light transmission.
IZOD IMPACT,
NOTCHED
107 J/m XZ axis
Heat Deflection
Temperature
87°C
Flexural
Strength
62 MPa XZ axis
Tensile
Strength
37 MPa XZ axis
Material Highlights
Characteristics
- Translucent
- Strong and durable
- Impact-resistant
- Dimensionally stable
Options
- Available in mutual, red and amber colours
- Can be smoothed for improved transparency
Uses
- Automotive design, especially lights and gauges
- Medical device prototypes that require fluid monitoring
- Other parts and prototypes that require fluid monitoring or light transmission
Advantages
- Accurate, reliable functional testing with translucent ABS plastic
- Hands-free support removal
Performance Scale
Material Colours
Technical Specifications
Mechanical Properties | Test Method | English | Metric |
Tensile Strength (Type 1, 0.125″, 0.2″/min) | ASTM D638 | 5,400 psi | 37 MPa |
Tensile Modulus (Type 1, 0.125″, 0.2″/min) | ASTM D638 | 277,700 psi | 1,920 MPa |
Tensile Elongation (Type 1, 0.125″, 0.2″/min) | ASTM D638 | 4.4% | 4.4% |
Flexural Strength (Method 1, 0.05”/min) | ASTM D790 | 8,980 psi | 62 MPa |
Flexural Modulus (Method 1, 0.05”/min) | ASTM D790 | 278,000 psi | 1,920 MPa |
IZOD Impact, notched (Method A, 23°C) | ASTM D256 | 1.8 ft-lb/in | 96.4 J/m |
IZOD Impact, un-notched (Method A, 23°C) | ASTM D256 | 3.6 ft-lb/in | 191.1 J/m |
Thermal Properties | Test Method | English | Metric |
Heat Deflection (HDT) @ 66 psi, 0.125″ unannealed | ASTM D648 | 188°F | 86°C |
Heat Deflection (HDT) @ 264 psi, 0.125″ unannealed | ASTM D648 | 163°F | 73°C |
Glass Transition Temperature (Tg) | DMA (SSYS) | 240°F | 116°C |
Coefficient of Thermal Expansion | ASTM D696 | 6.7×10-06 in/in/°F | 12.1×10-05 mm/mm/°C |
Melting Point | — | NA | NA |
Electrical Properties | Test Method | Value Range |
Volume Resistivity | ASTM D257 | 1.5×109 – 6.1×1010 ohm-cm |
Dielectric Constant | ASTM D150-98 | 3.4 – 3.6 |
Dissipation Factor | ASTM D150-98 | 0.12 – 0.15 |
Dielectric Strength | ASTM D149-09, Method A | 100 – 320 V/mil |
Other | Test Method | Value |
Specific Gravity | ASTM D792 | 1.08 |
Rockwell Hardness | ASTM D785 | R108 |
Flame Classification | UL 94 | HB (0.059″, 1.5mm) |