Multi Jet Fusion 3D Printing Technology
Multi Jet Fusion is a 3D printing technology that allows for more possibilities when it comes to complex, lower-cost parts. Ideal for both production of single parts or large prints consisting of multiple different parts. Multi Jet Fusion is an excellent technology for applications like thin walls, brackets, housings clips and guides. Industries can benefit from Multi Jet Fusion higher volume capabilities through limited run, pre-production and spare parts.
Applications
The HP Multi Jet Fusion polyamide 3D printing process is perfect for applications that require strength and durability, but higher volumes. Here are some of the common applications we see
|
|
Materials
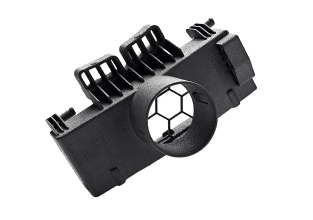
Nylon 12 (HP High Reusability PA 12)
Material: Polyamide 12 (Nylon PA 12)
HP 3D High Reusability PA 12 is a robust thermoplastic that produces high-density parts with balanced property profiles and strong structures.
Specs
- Powder Melting Point (DSC): 187° C or 369° F, ASTM D3418
- Particle Size: 60µm
- Bulk Density of Powder: 0.425 g/cm3 0.015 lb/in, ASTM D1895
- Tensile Strength: 30 MPa
- Elongation at Break: 20%
- Young’s Modulus: 1600 MPa
- Charpy Impact Notched Test: 35kJ/m²
Application
- Consumer goods and electronics
- Low-high volume production
- Rapid prototyping
- Manufacturing aids
- Tooling, end-of-arm tooling, robotics
- Medical
- Porthotics, prosthetics
Technology/Process
HP Multi Jet Fusion (Powder Bed Fusion)
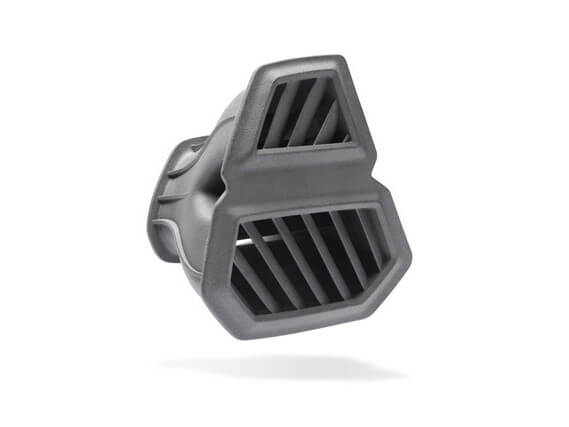
Polypropylene (HP High Reusability PP by BASF)
Material: Polypropylene
This polypropylene 3D printing material is designed for parts that require high strength, excellent chemical resistance and low moisture absorption.
Specs
- Tensile strength: 30 MPa
- Young’s modulus: 1600 MPa
- Elongation at break: 20 %
- Charpy impact notched: 3.5 kJ/m²
- HDT B: 100 °C
Application
Car interior parts, fluid and HVAC systems, tubes, pipes, reservoirs, medical devices, orthotics, functional prototypes, multi-purpose industrial goods
Technology/Process
HP Multi Jet Fusion (Powder Bed Fusion)
HP Multi Jet Fusion (MJF) Technical Specifications
Standard Lead Time |
Standard Lead Time3-5 Business Days |
Part Accuracy |
Part Accuracy+/-0.200mm |
Layer Resolution |
Layer Resolution0.080mm |
Minimum Wall Thickness (Recommended) |
Minimum Wall Thickness (Recommended)0.3mm in XY, 0.5mm in Zminimum feature size 0.1mm |
Maximum Part Dimensions (Single Build) |
Maximum Part Dimensions (Single Build)375 x 280 x 375mm (LxWxH) (Listed build volume is 380 x 284 x 380mm)14.7 x 11 x 14.7 inches |
Available Finishes |
Available FinishesStandard finish is grey powder finishLevel 1 is painted/dyed to a black uniform finish Sand/primer/paint is available upon request |
How Does MJF Work?
Multi Jet fusion is a powder binder based technology that relies on heat, fusing agents, detailing agents, and power polyamide to build up your parts. It all starts with a 3D model and then a 5 step process.