A Better Way to Polish Metal Parts
DLyte DryLyte® dry-electropolishing systems simplify and automate the post-processing of metal and alloy parts. This new patented technology uses solid media for grinding and polishing metals leveraging ion transport using free solid bodies.
Unlike traditional polishing systems, DLyte systems obtain a consistent finish avoiding any marks on the surface, patterns such as those generated by machining, and are able to process complex geometries without generating micro-scratches on the surface. DLyte respects the tolerances of the piece, delivering a mirror finish.
Discover a cleaner and more efficient way to smooth and polish metal parts
Powered by Science
Electropolishing is a specific type of electrolysis that involves a direct electrical current that passes through an electrolyte in an electrolytic cell.
The piece of metal to be polished serves as an anode, connected to a positive terminal of a direct current power supply, with the negative terminal connected to a cathode.
The metal part and the cathode are immersed in an electrolytic medium. Activating the power supply produces an electrical current that goes through the anode to the cathode, which results in oxidation on the metallic surface. These oxides that are formed are then dissoled, which eliminates the material on the surface andproduces a smooth and polished effect.
nbnbnbnbnbnbnbnbnbnbnbn
nbnbnbnbnbnnbnbnbnbnbnb
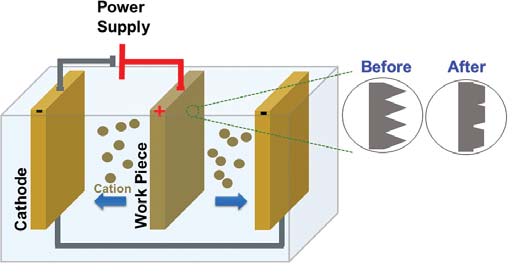
How it works
The metal surface finishing process extracts the material only from the peaks of the roughness. It does not round the edges but penetrates the internal cavities of the piece to which cannot be accessed mechanically.
DryLyte is a new patented technology based on a set of solid electrolyte particles with the ability to conduct electricity and to remove the oxides produced during the electropolishing process. Unlike traditional polishing systems, the DryLyte system obtains a uniform finish avoiding marks on the surface, patterns like those generated by machining, and is capable of processing complex geometries without generating micro-scratches on the surface.
Dry Electropolishing versus traditional polishing methods
Liquid Electropolishing
- Multi steps process
- Higher surface roughness
- Oxidation, passivation, milky surface, orange peel
- Waviness on the surface
Abrasive electropolishing
- Generates dust and noise
- Hazardous for the operator
- Wastewater management required
- Cannot access small corners or dead zones of the metal parts
- Less corrosion resistance
- 5 x slower than the dry electropolishing
Dry electropolishing
- One-step process
- Solid media
- Resistance against corrosion
- Ease of use
- Lower surface roughness
- Can access small corners and dead zones of the metal parts
- Preserves the metal part’s geometry
- Does not round the edges of the metal part
- Same high quality for all polished parts. Homogeneity and repeatability
- Clean and environmentally friendly process
- No risk of contamination and no handling of hazardous chemicals like traditional methods.
DLyte Part Polishing Examples
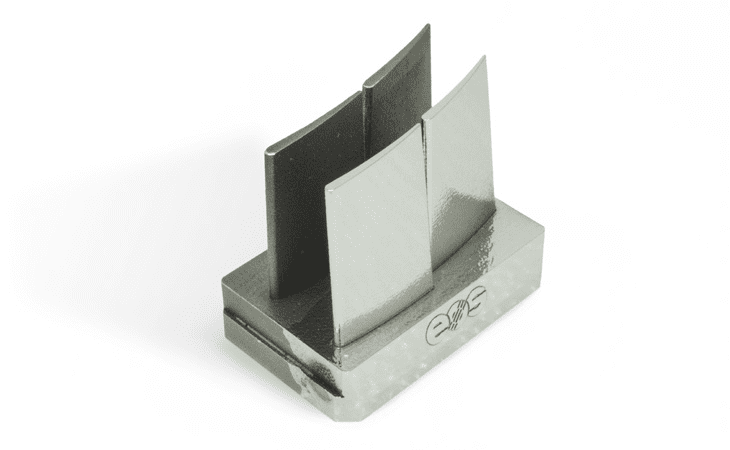
Sintered Inconel 718
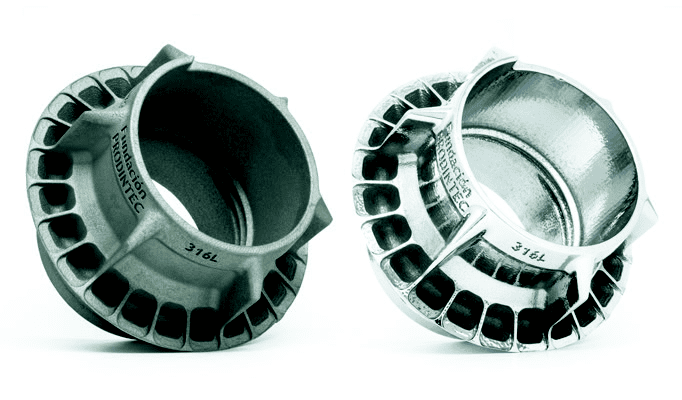
Sintered INOX316L
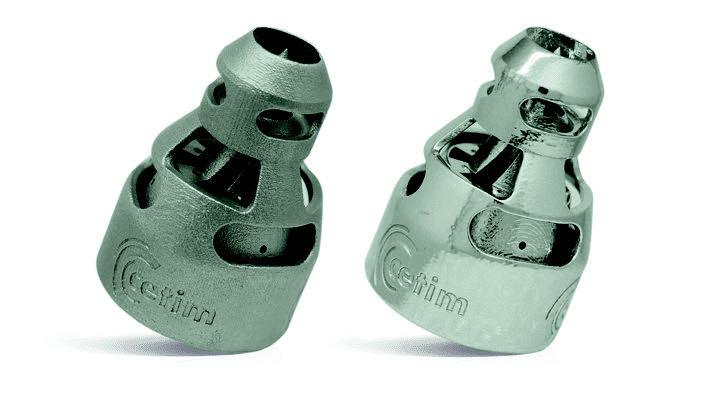
Laser Sintered INOX316L
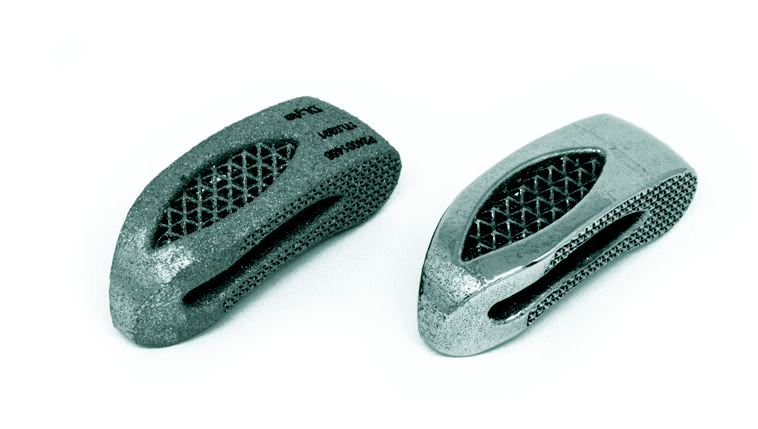
Laser Sintered Titanium
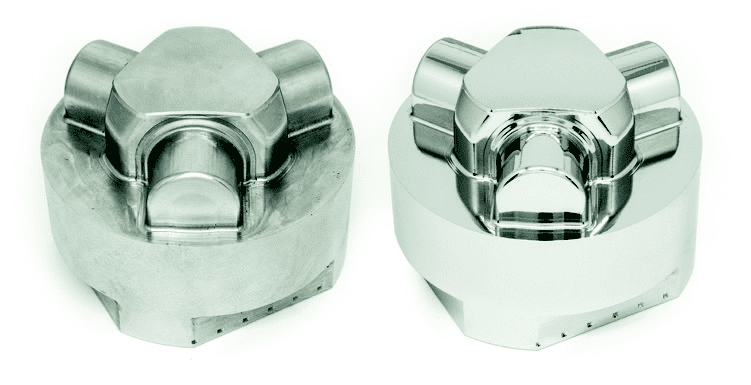
CNC Machined INOX 316L
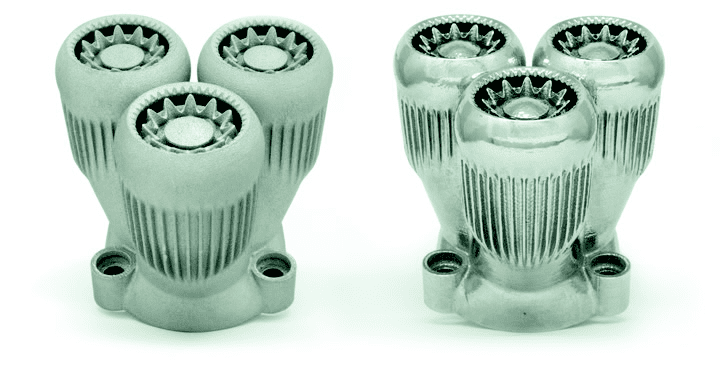
Laser Sintered Chrome Cobalt
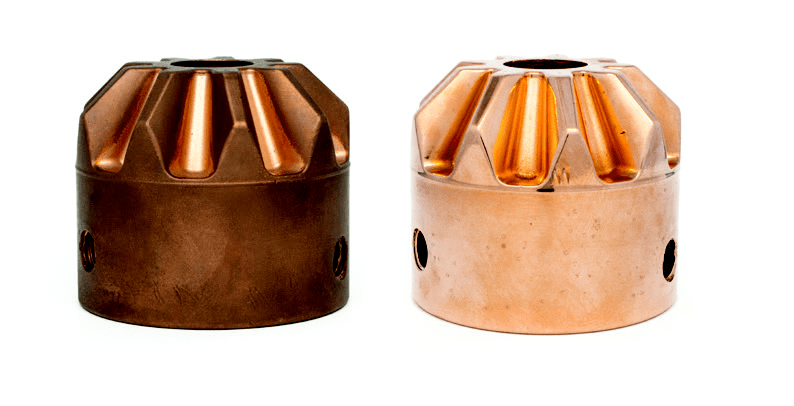
Casted Copper
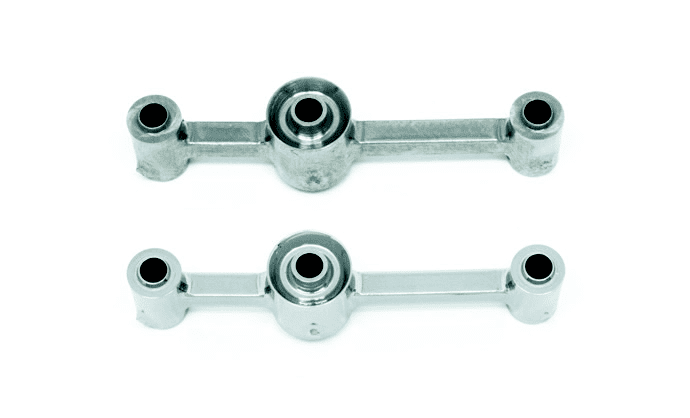
CNC Machined Titanium
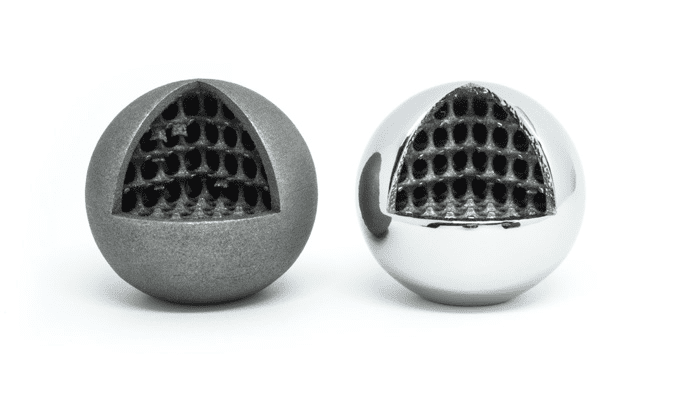
Laser Sintered Chrome Cobalt