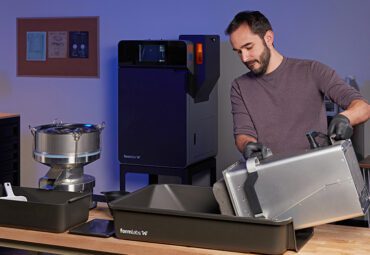
Overview
In the past decade, 3D scanning and additive manufacturing technologies have significantly advanced innovation in the aerospace industry. Applications such as advanced tooling and production have established these technologies as essential components in engineering. Through 3D printing, a new generation of aerospace companies can validate design ideas and tackle design challenges more quickly and affordably than ever before.
Trusted By
Ushering In The Next Generation Of Aviation
Design with Freedom
Explore new horizons as 3D printing gives the manufacturers the flexibility for easy and seamless design iteration and verification. Designs can be as complex or as simple as they need to be without the added costs.
Lightweighting
Reduce the weight of aircraft parts and components by up to 60%. 3D printing enables engineers to design parts with intricate geometries that provide the durability of production-grade thermoplastics while being significantly lighter allowing aircrafts to consume less fuel and emit less carbon dioxide.
Supply Chain Consolidation
Minimize the number of suppliers and outsourcing needed as 3D printing brings the job in-house, saving costs and time.
Safety
3D printed aircraft parts are tested thoroughly and are run through numerous safety regulations approvals to ensure a standard of quality and reliability for use in the air.
Passenger Experience
Create 3D printed interior parts as manufacturers are able to differentiate the passenger experience with unique, low-volume elements that are customized to the end customer’s needs and styles.
Toolless Production
3D printing technology allows for maximum design flexibility in production while requiring less energy and raw materials than traditional manufacturing processes. Parts and components can be produced as needed, saving valuable storage space.