Formlabs® Fuse Sift
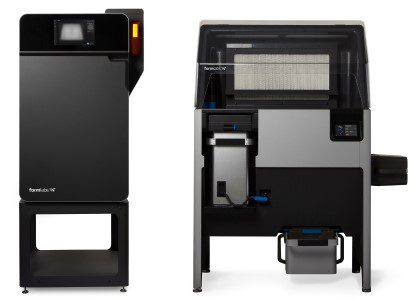
Formlabs®
Fuse Sift & SLS Depowdering Kit
The Key to Affordable, Industrial SLS 3D Printing
Fuse Sift by Formlabs is part of a complete SLS 3D printing workflow. The Fuse ecosystem makes possible the 3D-printing of industrial-grade parts. You can go from printing to finished parts in as little as 15 minutes, with an efficient, hands-off process.
What is Fuse Sift?
Fuse Sift is a de-powdering station designed by Formlabs to help you streamline your workflow with Fuse Series 3D printers by creating a seamless, contained environment for SLS production.
- Mess-Free Post-Processing
- Nonstop Printing
- Automated Powder Mixing
- A Complete Toolkit
Fast, Automated Post-Processing for SLS 3D-Printing
Fuse Sift filters, measures, mixes, and stores powder for you, while Fuse Blast delivers 100% hands-off part cleaning and polishing.
FUSE SIFT Features & Benefits
Compact & efficient powder management station.
- RECLAIM
Parts are extracted from the FUSE 1+ 30W SLS printer, and unsintered powder is collected and sifted to remove debris so it can be reused. - PREPARE
New and used powder are automatically measured, mixed with fresh powder, and stored for the next print.
Enclosed System
FUSE SIFT has a HEPA filter and a negative air pressure system that keeps powder inside, enabling open access and easy cleanup.
- Dimensions
- 1.0 m x 0.6 m x 1.5 m
- 39.9 in x 24 in x 60.8 in
Low Waste
Fuse Sift efficiently collects unsintered powder and filters out debris to be reused in the next print. Competitive material recyclability allows you to use up to 80% used powder.
MATERIAL REFRESH RATE: 20 – 50%
Automatic Powder Mixing
- Fuse Sift will dispense, mix, and store used and new powder automatically. This way, you can reduce waste and control your powder supply easily.
Nonstop Printing
- By transferring modular build chambers and powder cartridges between the printer and Fuse Sift, you can reduce downtime for a continuous, cyclical workflow with minimum downtime – even during cooldown
Technical Specifications
Printer Compatibility |
Printer CompatibilityFuse Series SLS 3D Printers |
Minimum Dimensions for Convenient Access (W × D × H) |
Minimum Dimensions for Convenient Access (W × D × H)221.1 × 122.0 × 218.0 cm87.1 × 48.0 × 85.8 in |
Product Dimensions (W × D × H) |
Product Dimensions (W × D × H)101.5 × 61.0 × 154.5 cm39.9 × 24.0 × 60.8 in Height when open: 190 cm (75 in) |
Product Weight |
Product Weight93 kg (without build chamber or powder)205 lb (without build chamber or powder) |
Hopper Capacity |
Hopper CapacityFresh Powder Hopper Capacity17 liters Used Powder Hopper Capacity 18 liters |
Operating Environment |
Operating Environment18 – 26 ºC68 – 80 ºF ≤ 30% ambient humidity |
Air Handling |
Air HandlingNegatively pressurized hood with replaceable HEPA filterIndependent venting system |
Power Requirements (with a vacuum that draws less than 6 A (230 VAC) / 12 A (120 VAC) |
Power Requirements (with a vacuum that draws less than 6 A (230 VAC) / 12 A (120 VAC)US: 120 VAC, 15 A (dedicated circuit) |
Power Requirements (with a vacuum that draws more than 6 A (230 VAC) / 12 A (120 VAC)) |
Power Requirements (with a vacuum that draws more than 6 A (230 VAC) / 12 A (120 VAC))US: 120 VAC, 20 A (dedicated circuit) |
Compressed Air Requirements |
Compressed Air RequirementsN/A |