Formlabs® SLA resins offer a diverse range of formulations, allowing for flexibility in material properties. They can be tailored to be soft or hard, incorporate secondary materials like glass and ceramic, or possess specific mechanical properties such as high heat deflection temperature or impact resistance.
These materials cover various industries, from dentistry to prototyping, and are designed to endure rigorous testing and perform reliably under stress.
General Purpose Materials
for High-resolution Models & Rapid Prototyping
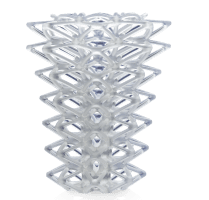
Clear
Material: Formlabs® Clear Resin
Clear Resin polishes to near optical transparency, ideal for showcasing internal features. 3D-printed parts have a smooth surface finish and no post-curing is necessary.
Specs
- Ultimate Tensile Strength:
- Green*: 38 MPa
- Post-Cured**: 65 MPa
- Tensile Modulus:
- Green*: 1.6 GPa
- Post-Cured**: 2.8 GPa
- Elongation at Failure:
- Green*: 12%
- Post-Cured**: 6.2%
- Heat Deflection Temperature @ 264psi:
- Green*: 42.7ºC
- Post-Cured**: 58.4ºC
*Data and specs were obtained from green parts printed using Form 2 SLA printer, 100 microns, clear settings, without additional treatments.
**Data was obtained from parts printed using Form 2, 100 μm, clear settings and post-cured with 1.25 mW/cm² of 405 nm LED light for 60 minutes at 60°C.
Application
- High-Temperature Rapid Prototyping
Technology/Process
- Stereolithography (SLA)
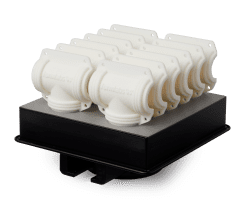
White
Material: Formlabs® White Resin
White Resin captures smooth surfaces and details, making it great for presentation-ready pieces or as a base for painted prints. It is part of Formlabs’ library of Standard Resins.
Specs
- Ultimate Tensile Strength:
- Green*: 38 MPa
- Post-Cured**: 65 MPa
- Tensile Modulus:
- Green*: 1.6 GPa
- Post-Cured**: 2.8 GPa
- Elongation at Failure:
- Green*: 12%
- Post-Cured**: 6.2%
- Heat Deflection Temperature @ 264psi:
- Green*: 42.7ºC
- Post-Cured**: 58.4ºC
- Matt & Smooth surface finish
- Opaque appearance
*Data and specs were obtained from green parts printed using Form 2 SLA printer, 100 microns, clear settings, without additional treatments.
**Data was obtained from parts printed using Form 2, 100 μm, clear settings and post-cured with 1.25 mW/cm² of 405 nm LED light for 60 minutes at 60°C.
Application
- For parts that will eventually be painted or undergo other finishing processes.
Technology/Process
- Stereolithography (SLA)
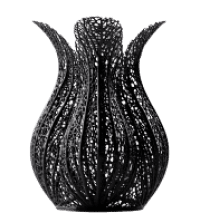
Black
Material: Formlabs® Black Resin
Black Resin is formulated for models with delicate features and intricate details. It is ideal for general-purpose prototyping and design.
Specs
- Ultimate Tensile Strength:
- Green*: 38 MPa
- Post-Cured**: 65 MPa
- Tensile Modulus:
- Green*: 1.6 GPa
- Post-Cured**: 2.8 GPa
- Elongation at Failure:
- Green*: 12%
- Post-Cured**: 6.2%
- Heat Deflection Temperature @ 264psi:
- Green*: 42.7ºC
- Post-Cured**: 58.4ºC
*Data and specs were obtained from green parts printed using Form 2 SLA printer, 100 microns, clear settings, without additional treatments.
**Data was obtained from parts printed using Form 2, 100 μm, clear settings and post-cured with 1.25 mW/cm² of 405 nm LED light for 60 minutes at 60°C.
Application
- High-Resolution Rapid Prototyping
Technology/Process
- Stereolithography (SLA)
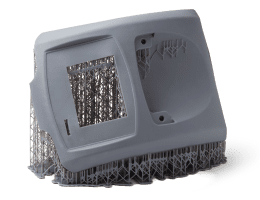
Grey
Material: Formlabs® Grey
Grey resin is a material for high-resolution models and rapid prototyping. It is an engineered resin that captures the finest features of a model and provides robust parts with a smooth surface finish.
Specs
- Ultimate Tensile Strength:
- Green*: 38 MPa
- Post-Cured**: 65 MPa
- Tensile Modulus:
- Green*: 1.6 GPa
- Post-Cured**: 2.8 GPa
- Elongation at Failure:
- Green* 12%
- Post-Cured**: 6%
- Heat Deflection Temperature @ 0.45 MPa:
- Green*: 50°C
- Post-Cured**: 73ºC
*Data and specs were obtained from green parts printed using Form 2 SLA printer, 100 microns, Clear settings, without additional treatments.
**Data was obtained from parts printed using Form 2, 100 μm, Clear settings and post-cured with 1.25 mW/cm² of 405 nm LED light for 60 minutes at 60°C.
Application
- Rapid Prototyping
- Functional Testing
- Product Development
Technology/Process
- Stereolithography (SLA)
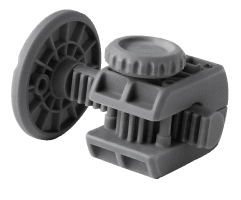
Grey PRO
Material: Formlabs® Grey PRO
Grey Pro Resin offers high precision, moderate elongation, and low creep. This material is great for concept modelling and functional prototyping, especially for parts that will be handled repeatedly.
Specs
- Ultimate Tensile Strength:
- Green*: 35 MPa
- Post-Cured**: 61 MPa
- Tensile Modulus:
- Green*: 1.4 GPa
- Post-Cured**: 2.6 GPa
- Elongation at Failure:
- Green*: 32.5%
- Post-Cured**: 13%
- Heat Deflection Temperature @ 0.45 MPa:
- Green*: not tested
- Post-Cured**: 77.5ºC
*Data and specs were obtained from green parts printed using Form 2 SLA printer, 100 microns, Grey PRO settings, without additional treatments.
**Data was obtained from parts printed using Form 2, 100 μm, Grey PRO settings and post-cured with a Form Cure for 120 minutes at 80°C.
Application
- Form and fit testing
- Injection molded product prototypes
- Mold masters for plastics, silicones, and more
- Jigs and fixtures for manufacturing
Technology/Process
- Stereolithography (SLA)
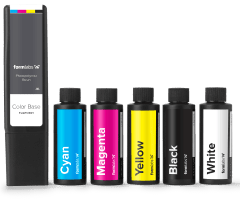
Colour Base | Kit
Material: Formlabs® Colour Base
Color Kit enables 3D printing in various colours without the manual work of finishing and painting. It is the first integrated colour-mixing solution for resin 3D printers.
Specs
- Color Kit contains a Color Base cartridge and all five Color Pigments.
- Mix and print matte, opaque parts in a range of colours
- Field test product concepts with custom colours
Material Properties
- Ultimate Tensile Strength:
- Green*: 38 MPa
- Post-Cured**: 65 MPa
- Tensile Modulus:
- Green*: 1.6 GPa
- Post-Cured**: 2.8 GPa
- Elongation at Failure:
- Green* 12%
- Post-Cured**: 6%
- Heat Deflection Temperature @ 264 psi:
- Green*: 42.7°C
- Post-Cured**: 58.4ºC
*Data and specs were obtained from green parts printed using Form 2 SLA printer, 100 microns, Clear settings, without additional treatments.
**Data was obtained from parts printed using Form 2, 100 μm, Clear settings and post-cured with 1.25 mW/cm² of 405 nm LED light for 60 minutes at 60°C.
Application
- Rapid Prototypes in custom colours
- Medical Models
- Art & Design
Technology/Process
- Stereolithography (SLA)
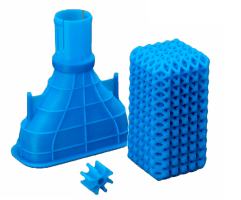
Draft
Material: Formlabs® Draft Resin
Draft resin prints up to x4 times faster than any other standard material. Parts 3D printed with Draft exhibit a smooth grey finish and high accuracy.
Specs
- Print large parts or batches of smaller parts fas
- Slightly more visible layer lines
- No post-curing necessary
Material Properties
- Ultimate Tensile Strength:
- Green*: 24 MPa
- Post-Cured: 36 MPa
- Tensile Modulus:
- Green*: 0.8 GPa
- Post-Cured at Room Temperature**: 1.7 GPa
- Elongation at Failure:
- Green*: 14%
- Post-Cured at Room Temperature**: 5%
- Heat Deflection Temperature @ 1.8 MPa:
- Green*: 37ºC
- Post-Cured at Room Temperature**: 43ºC
*Data was obtained from green parts, printed using Form 3, 200 micron, Draft v2 Resin settings, washed in Form Wash and air dried without post-cure.
**Data was obtained from parts printed using Form 3, 200 micron, Draft v2 Resin settings and post-cured with a Form Cure at Room Temperature for 5 minutes.
Application
- Prototyping and rapid iterations
Technology/Process
- Stereolithography (SLA)
Engineering Materials
with Exceptional Chemical & Mechanical Properties
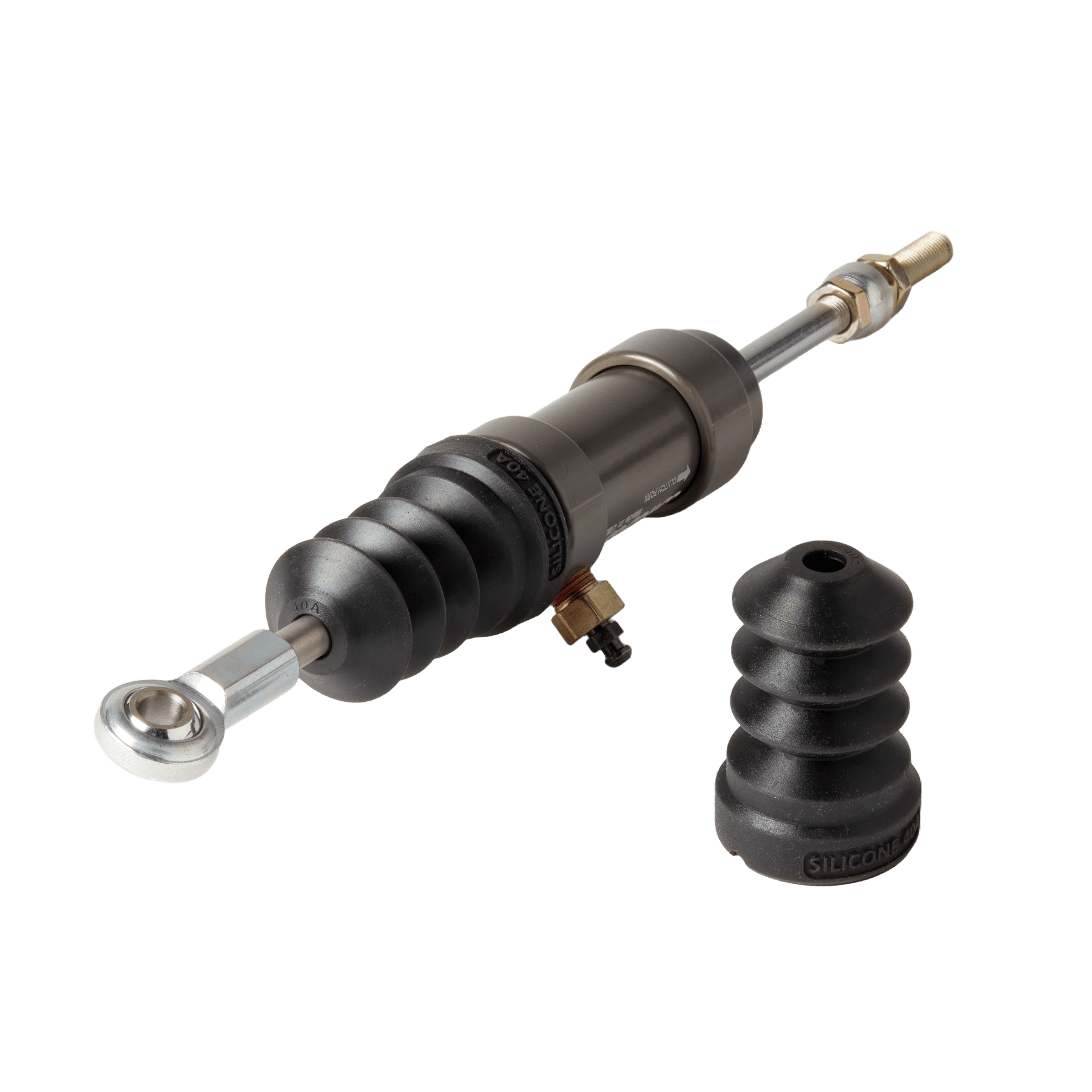
Silicone 40A
Material: Pure Silicone Resin
Formlabs Silicone 40A resin is the first pure silicone SLA 3D printing material, ideal for parts that require pliability and durability even through repeated stretching, flexing, or compression.
Specs
- Ultimate Tensile Strength: 5.0 MPa
- Elongation at Break: 230%
- Shore Hardness: 40A
- Viscosity @ 35°C: 800 cP
Application
- Wearables, handles, and grippers for consumer products
- Seals, gaskets, grommets, connectors, and dampeners for automotive, robotics, and manufacturing
- Customized prosthetics, orthotics, audiology models, and medical devices
- Flexible fixtures, masking tools, and soft molds for casting urethane or resin
Technology/Process
- Stereolithography (SLA)
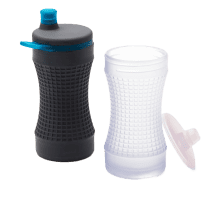
Flexible 80A
Material: Formlabs® Flexible 80A
This resin is one of the most soft-touch materials from Formlabs® with an 80A Shore durometer to simulate the flexibility of rubber or TPU.
Specs
- Ultimate Tensile Strength*:
- Green: 3.7 MPa
- Post-Cured**: 8.9 MPa
- Stress at 50% Elongation:
- Green: 1.5 MPa
- Post-Cured**: 3.1 MPa
- Stress at 100% Elongation:
- Green: 3.5 MPa
- Post-Cured**: 6.3 MPa
- Elongation at Failure:
- Green: 100%
- Post-Cured**: 120%
- Shore Hardness:
- Green: 70A
- Post-Cured**: 80A
*Tensile testing was performed after 3+ hours at 23ºC, using a Die C dumbbell and 20 in/min crosshead speed.
**Data was obtained from parts printed using Form 3 SLA printer, 100 microns, Flexible 80A settings, washed in Form Wash for 10 minutes, and post-cured with Form Cure at 60ºC for 10 minutes.
Application
- Handles, grips, and overmolds
- Seals, gaskets, and masks
- Cushioning, damping, and shock absorption
Technology/Process
- Low Force Stereolithography
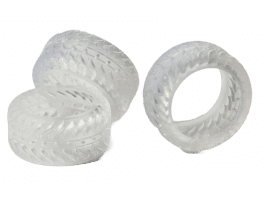
Elastic 50A
Material: Formlabs® Elastic 50A
Elastic 50A is a 50A Shore durometer material for prototyping parts usually produced with silicone that will need to bend, stretch or compress.
Specs
- Ultimate Tensile Strength:
- Green: 1.61 MPa
- Post-Cured*: 3.23 MPa
- Stress at 50% Elongation:
- Green: 0.92 MPa
- Post-Cured*: 0.94 MPa
- Stress at 100% Elongation:
- Green: 1.54 MPa
- Post-Cured*: 1.59 MPa
- Elongation at Failure**:
- Green: 100%
- Post-Cured*: 160%
- Shore Hardness:
- Green: 40A
- Post-Cured*: 50A
*Data was obtained from parts printed using Form 2, 100 µm, Elastic 50A settings, washed in Form Wash for 20 minutes and post-cured with Form Cure at 60 ˚C for 20 minutes.
**Tensile testing was performed after 3+ hours at 23ºC, using a Die C dumbbell and 20 in/min crosshead speed.
Application
It is ideal for parts that will bend, stretch, compress and hold up to repeated cycles without tearing and spring back quickly to their initial shape.
- Wearables and consumer goods prototyping
- Medical models and devices
- Compliant features for robotics
- Special effects props and models
Technology/Process
- Stereolithography (SLA)
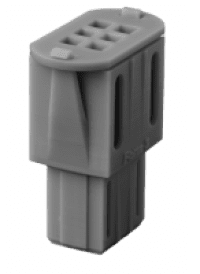
PU Rigid 650
Material: Formlabs' Rigid 650 Polyurethane
PU Rigid 650 Resin is a tough and pliable polyurethane material that can withstand extreme impacts while maintaining true shape long-term.
Specs
- Ultimate Tensile Strength:
- Post-Cured*: 34 ± 3.4 MPa
- Flexural Strength:
- Post-Cured*: 0.67 ± 0.06 GPa
- Flexural Modulus:
- Post-Cured*: 0.57 ± 0.03 GPa
- Elongation at Break:
- Post-Cured*: 170 ± 17 %
- Notched Impact:
- Post-Cured*: 375 J/m
- Heat Deflection Temperature @ 1.8 MPa:
- Post-Cured*: 59ºC
- Hardness:
- Shore D, 64
*Data for post-cured samples were measured on Type IV tensile bars printed on a Form 2 printer with 100 µm PU Rigid 650 Resin settings, washed in a Form Wash for 2 minutes in ≥99% PGDA, and post-cured.
Application
- Impact-resistant components
- Pliable mechanical connectors
- Shock-absorbing bumpers and dampeners
- Noise-dampening components
Technology/Process
- Stereolithography (SLA)
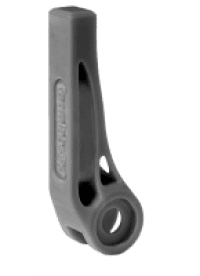
PU Rigid 1000
Material: Formlabs' Rigid 1000 Polyurethane
PU Rigid 1000 Resin is a semi-rigid and tough polyurethane material, ready to handle high impacts and harsh environments repeatedly.
Specs
- Ultimate Tensile Strength:
- Post-Cured*: 35 ± 3.5 MPa
- Flexural Strength:
- Post-Cured*: 32 ± 1.6 GPa
- Flexural Modulus:
- Post-Cured*: 0.75 ± 0.03 GPa
- Elongation at Break:
- Post-Cured*: 80 ± 8 %
- Notched Impact:
- Post-Cured*: 170 J/m
- Heat Deflection Temperature @ 1.8 MPa:
- Post-Cured*: 64ºC
- Hardness:
- Shore D, 74
*Data for post-cured samples were measured on Type IV tensile bars printed on a Form 2 printer with 100 µm PU Rigid 1000 Resin settings, washed in a Form Wash for 2 minutes in ≥99% PGDA, and post-cured.
Application
- Protective casings, housings, and enclosures
- Static jigs and fixtures undergoing high stress
- Sturdy consumer products
Technology/Process
- Stereolithography (SLA)
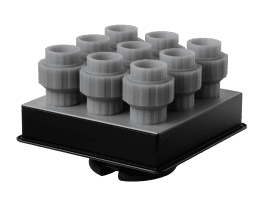
Tough 1500
Material: Formlabs® Tough 1500
Tough 1500 Resin is a resilient material certified for long-term skin contact that is ideal for stiff and pliable parts that bend and spring back quickly.
Specs
- Simulates the strength and stiffness of polypropylene (PP)
Material Properties:
- Ultimate Tensile Strength:
- Green: 26 MPa
- Post-Cured*: 33 MPa
- Elongation at Break:
- Green: 69%
- Post-Cured*: 51%
- Flexural Strength:
- Green: 15 MPa
- Post-Cured*: 39 MPa
- Flexural Modulus:
- Green: 0.44 GPa
- Post-Cured*: 1.4 GPa
- Notched Izod:
- Green: 72 J/m
- Post-Cured*: 67 J/m
- Heat Deflection Temperature @1.8 MPa:
- Green: 34°C
- Post-Cured*: 45°C
*Data was obtained from parts printed using Form 2, 100 μm, Tough 1500 settings and post-cured with a Form Cure for 60 minutes at 70°C.
Application
- Springy prototypes and assemblies
- Jigs and fixtures
- Snap-fit and press-fit connectors
- Wearables, personal protective equipment, and other consumer goods
- Stiff, pliable biocompatible parts
Technology/Process
- Stereolithography (SLA)
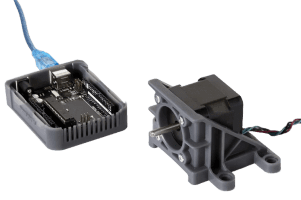
Tough 2000
Material: Formlabs® Tough 2000
Tough 2000 is the strongest and stiffest material in the Tough and Durable resins family. Ideal for prototyping, solid and sturdy parts that should not bend easily.
Specs
Material Properties:
- Ultimate Tensile Strength:
- Green: 29 MPa
- Post-Cured*: 46 MPa
- Elongation at Break:
- Green: 74%
- Post-Cured*: 48%
- Flexural Strength:
- Green: 17 MPa
- Post-Cured*: 65 MPa
- Flexural Modulus:
- Green: 0.45 GPa
- Post-Cured*: 1.9 GPa
- Notched Izod:
- Green: 79 J/m
- Post-Cured*: 40 J/m
- Heat Deflection Temperature @1.8 MPa:
- Green: 42°C
- Post-Cured*: 53°C
*Data was obtained from parts printed using Form 2, 100 μm, Tough 1500 settings and post-cured with a Form Cure for 60 minutes at 70°C.
Application
- Strong and stiff prototypes
- ABS-like strength and stiffness
- Sturdy jigs & fixtures
Technology/Process
- Stereolithography (SLA)
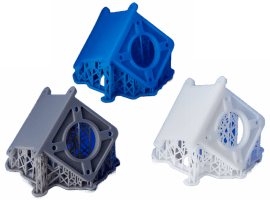
PU Rigid 4000
Material: Formlabs' Rigid 4000 Polyurethane
Rigid 4000 Resin is reinforced with glass to offer very high stiffness and a polished finish. This material is highly resistant to deformation over time and simulates PEEK’s stiffness.
Specs
- Ultimate Tensile Strength:
- UV-Cured*: 69 MPa
- Flexural Strength:
- UV-Cured*: 105 MPa
- Flexural Modulus:
- UV-Cured*: 3.4 GPa
- Elongation at Break:
- UV-Cured*: 5.3 %
- Notched Impact:
- UV-Cured*: 23 J/m
- Heat Deflection Temperature @ 1.8 MPa:
- UV-Cured*: 60ºC
*Data was obtained from parts printed using Form 3, 100 μm, Rigid 4000 (formerly Rigid v1) settings and post-cured with a Form Cure for 15 minutes at 80°C.
Application
- Mounts and brackets
- Thin-walled parts
- Jigs and Fixtures
Technology/Process
- Stereolithography (SLA)
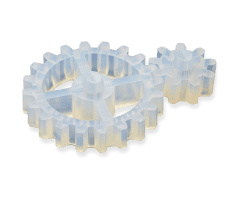
Durable
Material: Formlabs® Durable Resin
Durable Resin is the most pliable, impact-resistant, and lubricious material from Formlabs® family of tough and durable materials.
Specs
- Ultimate Tensile Strength:
- Green: 13 MPa
- Post-Cured: 28 MPa
- Tensile Modulus:
- Green: 0.24 GPa
- Post-Cured: 1.0 GPa
- Elongation at Failure:
- Green: 75%
- Post-Cured: 55%
- Heat Deflection Temperature @ 0.45 MPa:
- Green: < 30°C
- Post-Cured: 41ºC
Green: Data was obtained from green parts, printed using Form 2, 100 μm, durable settings, without additional treatments.
Post-Cured: Data was obtained from parts printed using Form 2, 100 μm, durable settings and post-cured with a Form Cure for 120 minutes at 60 °C.
Application
. It is ideal for squeezable parts and low-friction assemblies.
- Pliable Prototyping
- Impact resistant jigs
- Low-friction and non-degrading surfaces
- Polyethylene-like strength and stiffness
Technology/Process
- Stereolithography (SLA)
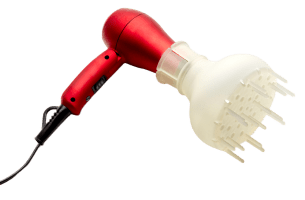
High Temp. Resin
Material: Formlabs® High-Temp Resin
High-Temperature Resin has a heat deflection temp (HDT) of 238 °C @ 0.45 MPa, the highest among Formlabs resins. You can print detailed, precise prototypes with high thermal stability.
Specs
- Ultimate Tensile Strength:
- Green*: 21 MPa
- Post-Cured**: 58 MPa
- Tensile Modulus:
- Green*: 0.57 GPa
- Post-Cured**: 2.8 GPa
- Elongation at Failure:
- Green*: 14%
- Post-Cured**: 3.3%
- Heat Deflection Temperature @ 1.8 MPa:
- Green*: 44ºC
- Post-Cured**: 78ºC
*Data and specs were obtained from green parts printed using Form 2 SLA printer, 100 microns, High Temp settings, washed for 5 minutes in Form Wash and air-dried without post-cure.
**Data was obtained from parts printed using Form 2, 100 μm, High Temp settings and post-cured with Form Cure at 60°C for 60 minutes.
For peak material properties such as HDT of 238 °C @ 0.45 MPa, additional thermal cure can be done: post-cured with Form Cure at 80°C for 120 minutes plus another thermal cure in a lab oven at 160°C for 180 minutes.
Application
- Hot air, gas, and fluid flow
- Heat-resistant mounts, housings, and fixtures
- Molds and inserts
Technology/Process
- Stereolithography (SLA)
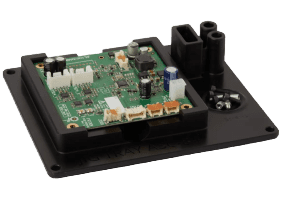
ESD
Material: Electrostatic discharge material (ESD)
ESD Resin is a cost-effective solution for producing static-dissipative parts designed to endure use on the factory floor.
Specs
- Ultimate Tensile Strength:
- Green*: 44.2 MPa
- Post-Cured*: 6410 psi
- Tensile Modulus:
- Green*: 1.937 GPa
- Post-Cured*: 280.9 ksi
- Elongation at Failure:
- Green*: 12%
- Post-Cured*: 12%
- Heat Deflection Temperature @ 1.8 MPa:
- Green*: 54.2ºC
- Post-Cured*: 129.6ºF
- Hardness: Shore D, 90
Electrical Properties:
-
- Surface Resistivity: 1055 – 1088 Ω/sq
- Volume Resistivity: 105 – 107 Ω/sq
*Data and specs were measured on Type IV tensile bars printed on a Form 3 printer with 100 µm ESD Resin settings, washed in a Form Wash for 20 minutes in ≥99% Isopropyl Alcohol and post-cured at 70°C for X 60 minutes in a Form Cure.
Application
- Tooling & fixturing for electronics manufacturing
- Custom trays for component handling and storage
- Anti-static prototypes and end-use components
Technology/Process
- Stereolithography (SLA)
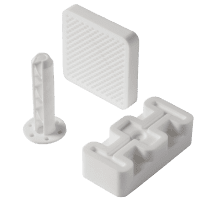
Alumina 4N
Material: Ceramic Resin
Alumina 4N is a high-density, high-purity technical ceramic with great performance in extreme environments. Thermally resistant, hard, abrasion resistant, mechanically strong, and chemically inert.
Specs
Sintered Physical & Mechanical Properties:
- 4 Point Flex Strength (XY)1,2: 400 MPa
- 4 Point Flex Strength (Z)1,2: 320 MPa
- Young’s Modulus: 390 GPa MPa
- Vickers Hardness*: 1500
Resin Properties:
- Purity [%]: 99.99%
- Relative Density: 98.60%
- Colour: Off-white
Thermal Properties:
- CTE (Coefficient of Thermal Expansion): 5 ppm/K
- Maximum Working Temperature: 1500°C
- Thermal Conductivity1,2: 32 W/m·K
1 | Currently testing at an independent lab.
2 | All sintered parts were fired using a 2-oven conservative firing schedule (schedule #1).
3D Printer Compatibility
- Form 3
- Form 3+
- Form 3B
- Form 3B+
Application
- High-voltage components
- Insulating housings or tubes
- Mixing blades and pipes
- Foundry tools for metal casting
Technology/Process
- SLA (Stereolithography)
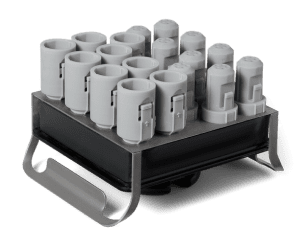
Flame Retardant (FR)
UL 94 V-0 Certified 3D Printed Parts with Great Quality and Heat Resistance
FR Resin is self-extinguishing and halogen-free with favourable flame, smoke, and toxicity (FST) ratings.
Specs
Mechanical Properties for Post-Cured @ 80°C / 120m:
- Ultimate Tensile Strength: 41 MPa
- Tensile Modulus: 3.1 GPa
- Elongation at Break: 7.1%
- Flexural Strength: 75 MPa
- Flexural Modulus: 2.7 GPa
- Notched Izod: 22 J/m
Thermal Properties:
- Heat Deflection Temp. @ 0.45 MPa: 111°C
- Coefficient of Thermal Expansion, 20°- 80°C: 68.1 μm/m/°C
- Glass Transition Temperature (Tg): 144°C
Flammability:
- UL 94: HB Classification*, 1.5 mm**
*HB-classification: slow burning on a horizontal specimen; burning rate < 76 mm/min for thickness < 3 mm or burning stops before 100 mm
**UL flammability rating bars were printed on Form 3+/Form 3 printers with 50µm Flame Retardant Resin settings, washed in a Form Wash for
(a) 10 minutes in ≥99% Isopropyl Alcohol or
(b) 15 minutes in ≥99% Tripropylene glycol monomethyl ether, with a quick water rinse, and then postcured at 70°C for 60 minutes in a Form Cure.
This rating can be achieved printing in any orientation and any available layer height on a Form 3, Form 3+, Form 3B, Form 3B+, Form 3L or Form 3BL.
Application
- Custom jigs, fixtures, and replacement parts for industrial environments with high temperatures or ignition sources
- Interior parts in airplanes, automobiles, and railways with excellent surface finish
- Protective and internal consumer or medical electronics components
Technology/Process
- Stereolithography (SLA)
Jewelry Design. Clean Investment Casting
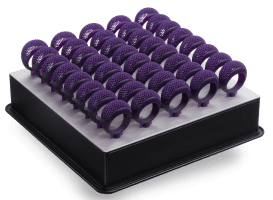
Castable Wax
Material: Formlabs® Castable Wax
Castable Wax offers high strength and stiffness, making it highly capable of printing ultrafine filigree jewelry. It is filled with 20% wax for clean, reliable casting.
Specs
- No post-curing required
Material Properties:
- Ultimate Tensile Strength:
- Green: 12 MPa
- Tensile Modulus:
- Green: 220 MPa
- Elongation at Break (green): 13%
Burnout Properties
- Temperature @ 5% Mass Loss:
- Green: 249ºC
- Ash content (TGA):
- Green: 0.0 – 0.1%
Application
- The high green strength of this resin ensures excellent shape retention for thin patterns such as wire filigree.
- Lightweight, intricate jewelry
- One material for prototypes and production
Technology/Process
- Stereolithography (SLA)
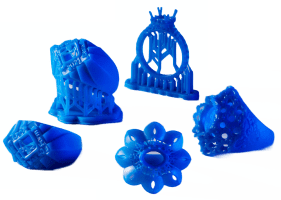
Castable Wax 40
Material: Formlabs® Castable Wax 40
Castable Wax 40 Resin offers exceptional casting performance for challenging designs with a new 40% wax formula and low thermal expansion.
Specs
- Cleanly cast stone settings, embossed text, and heavy pieces
- It uses gypsum investment and standard burnout
- No post-curing required
Burnout Properties
- Temperature @ 5% Mass Loss:
- Green: 249ºC
- Ash content (TGA):
- Green: 0.0 – 0.1%
Application
- This resin is ideal for direct casting the broadest range of styles, from heavy-class rings and medallions to lightweight bridal jewelry.
Technology/Process
- Stereolithography (SLA)
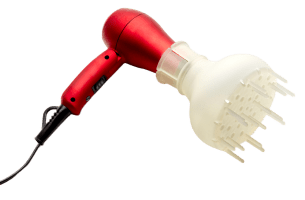
High Temp. Resin
Material: Formlabs® High-Temp Resin
High-Temperature Resin has a heat deflection temp (HDT) of 238 °C @ 0.45 MPa, the highest among Formlabs resins. You can print detailed, precise prototypes with high thermal stability.
Specs
- Ultimate Tensile Strength:
- Green*: 21 MPa
- Post-Cured**: 58 MPa
- Tensile Modulus:
- Green*: 0.57 GPa
- Post-Cured**: 2.8 GPa
- Elongation at Failure:
- Green*: 14%
- Post-Cured**: 3.3%
- Heat Deflection Temperature @ 1.8 MPa:
- Green*: 44ºC
- Post-Cured**: 78ºC
*Data and specs were obtained from green parts printed using Form 2 SLA printer, 100 microns, High Temp settings, washed for 5 minutes in Form Wash and air-dried without post-cure.
**Data was obtained from parts printed using Form 2, 100 μm, High Temp settings and post-cured with Form Cure at 60°C for 60 minutes.
For peak material properties such as HDT of 238 °C @ 0.45 MPa, additional thermal cure can be done: post-cured with Form Cure at 80°C for 120 minutes plus another thermal cure in a lab oven at 160°C for 180 minutes.
Application
- Hot air, gas, and fluid flow
- Heat-resistant mounts, housings, and fixtures
- Molds and inserts
Technology/Process
- Stereolithography (SLA)
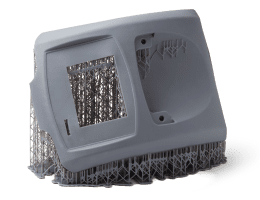
Grey
Material: Formlabs® Grey
Grey resin is a material for high-resolution models and rapid prototyping. It is an engineered resin that captures the finest features of a model and provides robust parts with a smooth surface finish.
Specs
- Ultimate Tensile Strength:
- Green*: 38 MPa
- Post-Cured**: 65 MPa
- Tensile Modulus:
- Green*: 1.6 GPa
- Post-Cured**: 2.8 GPa
- Elongation at Failure:
- Green* 12%
- Post-Cured**: 6%
- Heat Deflection Temperature @ 0.45 MPa:
- Green*: 50°C
- Post-Cured**: 73ºC
*Data and specs were obtained from green parts printed using Form 2 SLA printer, 100 microns, Clear settings, without additional treatments.
**Data was obtained from parts printed using Form 2, 100 μm, Clear settings and post-cured with 1.25 mW/cm² of 405 nm LED light for 60 minutes at 60°C.
Application
- Rapid Prototyping
- Functional Testing
- Product Development
Technology/Process
- Stereolithography (SLA)
BioMed Resins
For Healthcare Professionals seeking Medical-grade Materials
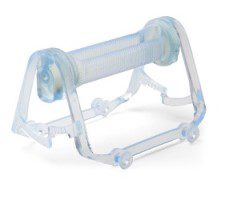
BioMed Durable
Certified medical-grade material
BioMed Durable Resin is a clear 3D printing material for biocompatible applications requiring impact, shatter, and abrasion resistance. It is manufactured in Formlabs’ FDA-registered & ISO 13485-certified facility.
Specs
- Ultimate Tensile Strength: 29.1 MPa
- Tensile Modulus: 994 MPa
- Elongation at Break: 33%
- Flexural Strength: 21 MPa
- Flexural Modulus: 643 MPa
- Hardness Shore D: 75D
- Notched Izod: 98 J/m
- Heat Deflection Temp @ 0.45 MPa: 46ºC
Application
USP Class VI material is made in an FDA-registered ISO 13485 facility and can be used in applications for long-term skin (>30 days) and short-term tissue, bone, dentin, and mucosal membrane contact (<24hrs).
- Patient-specific instruments
- End-use devices and components requiring biocompatibility and impact resistance
- Single-use instruments
Technology/Process
- Stereolithography (SLA)
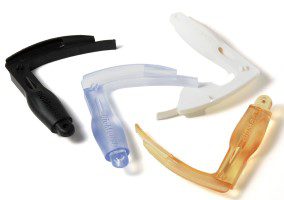
BioMed Clear Resin
For Long-Term Bodily Contact
Formlabs® BioMed Clear Resin is a medical-grade material validated in accordance with ISO 18562 and USP Class VI certified material, supported with an FDA Device Master File.
Specs
- Ultimate Tensile Strength: 52 MPa
- Young’s Modulus: 2080 MPa
- Elongation at Break: 12%
- Flexural Modulus: 2300 MPa
- Hardness: Shore D, 78
- Notched Izod: 35 J/m
*Data were measured on post-cured samples printed on a Form 3B printer with 100 µm BioMed Clear Resin settings, washed in a Form Wash for 20 minutes in 99% isopropyl alcohol, and post-cured at 60°C for 60 minutes in a Form Cure.
Application
- End-use devices, including gas pathway devices
- Models for visualization and implant sizing
- Biocompatible prototypes, molds, jigs and fixtures
- Cell culture and bioprocess devices
- Ventilator and PPE components
- Drug delivery devices
- Research & Development
Technology/Process
- Stereolithography (SLA)
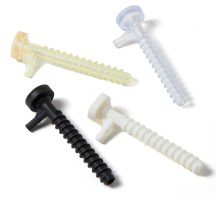
BioMed White Resin
For Rigid, Opaque, Biocompatible Parts
Formlabs® BioMed White Resin is USP Class VI certified and suitable for medical, pharmaceutical and drug delivery applications.
Specs
- Ultimate Tensile Strength: 45.78 MPa
- Young’s Modulus: 2020.16 MPa
- Elongation at Break: 10%
- Flexural Stress at 5% Strain: 74.46 MPa
- Hardness: Shore 80D
*Data were measured on post-cured samples printed on a Form3B with 100um BioMed White Resin settings, washed in a Form Wash for 5 minutes in 99% Isopropyl Alcohol, and post-cured at 60°C, 60 minutes in a Form Cure.
Application
- End-use medical devices and device components
- Patient-specific implant sizing models and molds
- Cutting and drilling guides
- Surgical tools and templates
- Biocompatible molds, jigs, and fixtures
- Anatomical models that can be used in the OR
Technology/Process
- Stereolithography (SLA)
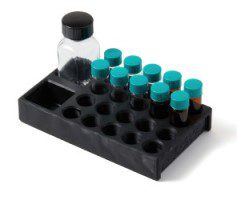
BioMed Black Resin
For Rigid, Opaque, Biocompatible Parts
Formlabs® BioMed Black resin is USP Class VI certified and is used in applications requiring long-term skin or short-term mucosal membrane contact.
Specs
- Ultimate Tensile Strength: 35.71 MPa
- Young’s Modulus: 1523.74 MPa
- Elongation at Break: 14%
- Flexural Stress at 5% Strain: 57.16 MPa
- Hardness: Shore D 77
- Notched IZOD: 24.77 J/m
* Data were measured on post-cured samples printed on a Form3B with 100um BioMed Black Resin settings, washed in a Form Wash
for 5 minutes in 99% Isopropyl Alcohol, and post-cured at 70°C, 60 minutes in a Form Cure.
Application
- Medical devices and device components
- End-use parts requiring patient contact
- Biocompatible molds, jigs, and fixtures
- Consumer goods
Technology/Process
- Stereolithography (SLA)
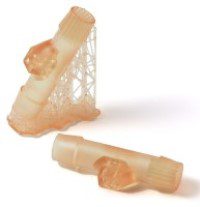
BioMed Amber Resin
For Semi-Transparent, Biocompatible Parts
Parts printed with BioMed Amber Resin are compatible with common solvent disinfection and sterilization methods.
Specs
BioMed Amber Resin is manufactured in Formlabs® ISO 13485 facility.
- Ultimate Tensile Strength: 73 MPa
- Young’s Modulus: 2900 MPa
- Elongation at Break: 12%
- Flexural Modulus: 2500 MPa
- Flexural Strength:103 MPa
- Hardness: Shore D, 67
- Notched Izod 28 J/m
*Data for post-cured samples were measured on Type IV tensile bars printed on a Form 2 and Form 3B (impact and thermal measurements) printers with 100 µm BioMed Amber Resin settings, washed in a Form Wash for 20 minutes in 99% Isopropyl
Alcohol, and post-cured at 60 °C for 30 minutes in a Form Cure.
Application
- Medical devices and device components
- Cutting and drilling guides
- Research and development
- Surgical planning and implant sizing tools
Technology/Process
- Stereolithography (SLA)
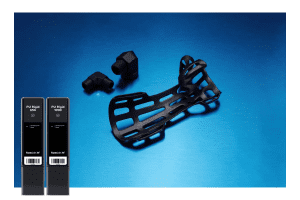
PU Rigid Materials
Material: PU Rigid 650 & 1000
You can choose Formlabs®’ PU Rigid 650 or 1000 for biocompatible applications, as they can withstand rugged applications due to their extraordinary toughness and durability properties.
Specs
- See PU Rigid PU 650 and PU Rigid 1000
Application
- Orthotics, Braces & Orthopedic Stabilizers
- Prosthetic Device Components
- Medical Device Components (Guards, Covers, Handles, Grips)
- End-Use Medical Devices
- Adaptive & Assistive Devices
Technology/Process
- Stereolithography (SLA)
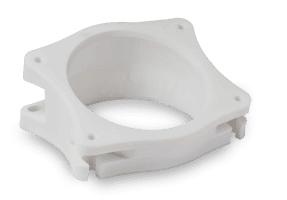
Rigid 10K
Material: Formlabs® Rigid 10K Resin
Rigid 10K Resin is our stiffest material that is ideal for precise industrial parts that need to withstand significant load without bending and benefit from resistance to heat and chemicals.
Specs
- Ultimate Tensile Strength:
- UV Cured*: 65 MPa
- Flexural Strength:
- UV Cured*: 126 MPa
- Tensile Modulus:
- UV Cured*: 10 GPa
- Elongation at Break:
- UV Cured*: 1%
- Notched Impact:
- UV Cured*: 16 J/m
- Heat Deflection Temperature @ 1.8 MPa:
- UV Cured*: 82ºC
*Data was obtained from parts printed using Form 3, 100 μm and post-cured with a Form Cure for 60 minutes at 70°C.
Application
- Short-run injection mold masters and inserts
- Aerodynamic test models
- Heat resistant and fluid-exposed components, jigs, and fixtures
- Simulates stiffness of glass and fibre-filled thermoplastics
Technology/Process
- Stereolithography (SLA)
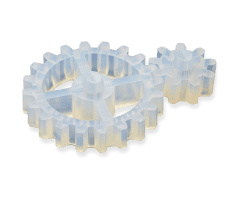
Durable
Material: Formlabs® Durable Resin
Durable Resin is the most pliable, impact-resistant, and lubricious material from Formlabs® family of tough and durable materials.
Specs
- Ultimate Tensile Strength:
- Green: 13 MPa
- Post-Cured: 28 MPa
- Tensile Modulus:
- Green: 0.24 GPa
- Post-Cured: 1.0 GPa
- Elongation at Failure:
- Green: 75%
- Post-Cured: 55%
- Heat Deflection Temperature @ 0.45 MPa:
- Green: < 30°C
- Post-Cured: 41ºC
Green: Data was obtained from green parts, printed using Form 2, 100 μm, durable settings, without additional treatments.
Post-Cured: Data was obtained from parts printed using Form 2, 100 μm, durable settings and post-cured with a Form Cure for 120 minutes at 60 °C.
Application
. It is ideal for squeezable parts and low-friction assemblies.
- Pliable Prototyping
- Impact resistant jigs
- Low-friction and non-degrading surfaces
- Polyethylene-like strength and stiffness
Technology/Process
- Stereolithography (SLA)
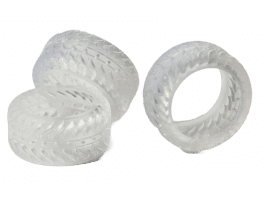
Elastic 50A
Material: Formlabs® Elastic 50A
Elastic 50A is a 50A Shore durometer material for prototyping parts usually produced with silicone that will need to bend, stretch or compress.
Specs
- Ultimate Tensile Strength:
- Green: 1.61 MPa
- Post-Cured*: 3.23 MPa
- Stress at 50% Elongation:
- Green: 0.92 MPa
- Post-Cured*: 0.94 MPa
- Stress at 100% Elongation:
- Green: 1.54 MPa
- Post-Cured*: 1.59 MPa
- Elongation at Failure**:
- Green: 100%
- Post-Cured*: 160%
- Shore Hardness:
- Green: 40A
- Post-Cured*: 50A
*Data was obtained from parts printed using Form 2, 100 µm, Elastic 50A settings, washed in Form Wash for 20 minutes and post-cured with Form Cure at 60 ˚C for 20 minutes.
**Tensile testing was performed after 3+ hours at 23ºC, using a Die C dumbbell and 20 in/min crosshead speed.
Application
It is ideal for parts that will bend, stretch, compress and hold up to repeated cycles without tearing and spring back quickly to their initial shape.
- Wearables and consumer goods prototyping
- Medical models and devices
- Compliant features for robotics
- Special effects props and models
Technology/Process
- Stereolithography (SLA)