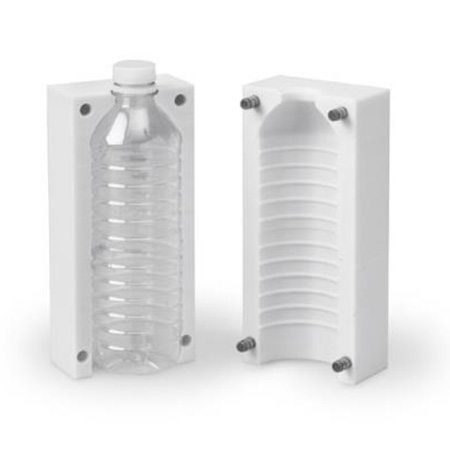
Polycarbonate (PC) Thermoplastic
Accuracy, Durability and Strength for Tough Manufacturing Challenges
3D printing with PC (polycarbonate) offers production-grade thermoplastics with exceptional accuracy, durability, and stability. Create strong parts that can withstand functional testing.
Overview
Printing with PC (polycarbonate) empowers designers and engineers to utilize the freedom and flexibility of 3D printing with the reliability of industrial thermoplastic quality. Strong PC parts can be printed in-house giving manufacturers more opportunities for cutting costs, efficiency, and growth. PC’s high tensile and flexural strength make this material ideal for demanding prototype needs, tooling and fixtures, and patterns for metal bending and composite work. Work with absolute confidence with PC 3D printing.
Material Performance
PC (polycarbonate) thermoplastic 3D printing materials is used widely across automotive, aerospace and medical industries. It’s high flexural and tensile strength make it ideal for rapid tooling, rapid prototyping, jigs, fixtures, and patterns for metal bending and composite work.
IZOD IMPACT,
NOTCHED
73 J/m XZ axis
28 J/m ZX axis
Heat Deflection
Temperature
138 °C
Flexural
Strength
89 MPa XZ axis
68 MPa ZX axis
Tensile
Strength
40 MPa XZ axis
30 MPa ZX axis
Material Highlights
Characteristics
- Opaque
- Heat-resistant
- Strong
- Durable
- Dimensionally Stable
Options
- Available in white
- Break-away support material or
- Dissolvable support material
Applications
- Functional Prototyping
- Jigs and FIxtures
- Rapid Tooling
- Manufacturing Tooling
- Production Parts
- Patterns for Metal Bending and Composite Work
Advantages
- Superior Mechanical Properties
- Accurate, reliable functional testing
- Widely used material
Performance Scale
Material Colours
Technical Specifications
Mechanical Properties | Test Method | English XZ Axis | English ZX Axis | Metric XZ Axis | Metric ZX Axis |
Tensile Strength, Yield (Type 1, 0.125”, 0.2”/min) | ASTM D638 | 5,800 psi | 4,300 psi | 40 MPa | 30 MPa |
Tensile Strength, Ultimate (Type 1, 0.125”, 0.2”/min) | ASTM D638 | 8,300 psi | 6,100 psi | 57 MPa | 42 MPa |
Tensile Modulus (Type 1, 0.125”, 0.2”/min) | ASTM D638 | 282,000 psi | 284,000 psi | 1,944 MPa | 1,958 MPa |
Tensile Elongation at Break (Type 1, 0.125”, 0.2”/min) | ASTM D638 | 4.8% | 2.5% | 4.8% | 2.5% |
Tensile Elongation at Yield (Type 1, 0.125”, 0.2”/min) | ASTM D638 | 2.2% | 2% | 2.2% | 2% |
Flexural Strength (Method 1, 0.05”/min) | ASTM D790 | 13,000 psi | 9,900 psi | 89 MPa | 68 MPa |
Flexural Modulus (Method 1, 0.05”/min) | ASTM D790 | 291,000 psi | 261,000 psi | 2,006 MPa | 1,800 MPa |
Flexural Strain at Break (Method 1, 0.05”/min) | ASTM D790 | No Break | 4% | No Break | 4% |
IZOD Impact, notched (Method A, 23°C) | ASTM D256 | 1.4 ft-lb/in | 0.5 ft-lb/in | 73 J/m | 28 J/m |
IZOD Impact, un-notched (Method A, 23°C) | ASTM D256 | 16.4 ft-lb/in | 3.5 ft-lb/in | 877 J/m | 187 J/m |
Compressive Strength, Yield (Method 1, 0.05”/min) | ASTM D695 | 10,000 psi | 9,200 psi | 69 MPa | 64 MPa |
Compressive Strength, Ultimate (Method 1, 0.05”/min) | ASTM D695 | 28,000 psi | 9,400 psi | 193 MPa | 65 MPa |
Compressive Modulus (Method 1, 0.05”/min) | ASTM D695 | 1,100,000 psi | 227,000 psi | 7,564 MPa | 1,565 MPa |
Thermal Properties | Test Method | English | Metric |
Heat Deflection (HDT) @ 66 psi | ASTM D648 | 280°F | 138°C |
Heat Deflection (HDT) @ 264 psi | ASTM D648 | 261°F | 127°C |
Vicat Softening | ASTM D1525 | 282°F | 139°C |
Glass Transition (Tg) | DMA (SSYS) | 322°F | 161°C |
Melting Point | — | NA | NA |
Electrical Properties | Test Method | Value Range |
Volume Resistivity | ASTM D257 | 6.0×1013 – 2.0×1014 ohm-cm |
Dielectric Constant | ASTM D150-98 | 2.8 – 3.0 |
Dissipation Factor | ASTM D150-98 | .0005 – .0006 |
Dielectric Strength | ASTM D149-09, Method A | 80 – 360 V/mil |
Other | Test Method | Value |
Specific Gravity | ASTM D792 | 1.2 |
Flame Classification | UL94 | HB |
Rockwell Hardness | ASTM D785 | R115 |
UL File Number | — | E345258 |