Formlabs® Flame Retardant
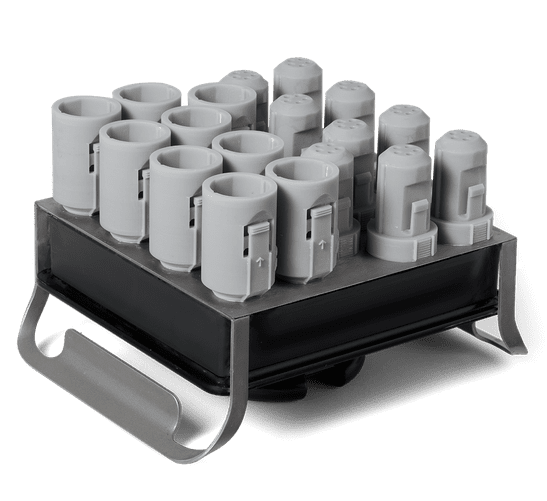
Formlabs®
Flame Retardant Resin
Flame, smoke, and toxicity (FST) SLA 3D printing material
Flame Retardant (FR) resin is an ideal specialty material for manufacturing durable plastic components engineered for stiffness, creep resistance, and optimal performance in both indoor and industrial settings. This Formlabs resin boasts self-extinguishing properties and is halogen-free, earning high marks for flame, smoke, and toxicity (FST) safety ratings.
Material Properties
ULTIMATE TENSILE STRENGTH
41.0 MPa
TENSILE MODULUS
3.1 GPa
FLEXURAL STRENGTH
75.0 MPa
ELONGATION AT BREAK
7.1%
Performance Scale
Strength | |
Injection Molded Look & Feel | |
Heat and Creep Resistance | |
Flammability Resistance |
Colour
The Benefits of Using Flame Retardant Resin
Applications
Produce certified flame retardant, UL 94 V-0, and FAR-rated 3D-printed parts that meet the certification requirements for enduring hazardous environments.
Material Variants | 3D Printer Compatibility
Post Processing
FORM CURE SETTINGS
DURATION TEMPERATURE
60 minutes 70 °C
NOTES
- To achieve the highest HDT of 111 °C @ 0.45 MPa: Post-cure parts in Form Cure for 120 min at 80 °C.
- For applications that do not require the maximum heat resistance but offer more toughness, post-cure parts in Form Cure for 60 min at 70 °C.
Technical Specifications*
|
|
|
|||
Ultimate Tensile Strength |
24 MPa | 38 MPa | 41 MPa | ||
Tensile Modulus |
1.8 GPa | 2.9 GPa | 3.1 GPa | ||
Elongation at Break |
20% | 9.4% | 7.1% | ||
Flexural Strength |
36 MPa | 72 MPa | 75 MPa | ||
Flexural Modulus |
1.3 GPa | 2.7 GPa | 2.7 GPa | ||
Notched Izod |
19 J/m | 22 J/m | 22 J/m | ||
Unnotched Izod |
227 J/m | 241 J/m | 257 J/m | ||
Work of Fracture (Wf) |
N/A | 311 J/m2 | 277 J/m2 | ||
Heat Deflection Temp. @ 1.8 MPa |
45 °C | 71 °C | 83 °C | ||
Heat Deflection Temp. @ 0.45 MPa |
55 °C | 94 °C | 111 °C | ||
Glass Transition Temperature (Tg) |
101 °C | 130 °C | 144 °C | ||
Hardness, Shore D |
74D 80D (post-cured) |
||||
Viscosity (25 °C) |
4500 - 5000 cP | ||||
Flammability, Smoke Toxicity and Gas Toxicity |
*Material properties may vary based on part geometry, print orientation, print settings, temperature, and disinfection or sterilization methods used. Data for tensile samples were measured on Type I tensile bars printed on a Form 3+ printer with 100 µm Flame Retardant Resin settings, washed in a Form Wash for 10 minutes in ≥99% Isopropyl Alcohol, and post-cured at 70°C for 60 minutes or 80°C for 120 minutes in a Form Cure.