Prototype to Part
The Advanced Manufacturing Engineering Department at Dixon Valve is nestled competitively in the hose coupling industry with its suitable motto “The Right Connection”. A few years ago, they invested in 3D printing to address the workings of their automated and manufacturing equipment. “We saw an opportunity to improve our efficiency by using 3D printing to rapidly develop functional prototypes for our gantry systems,” said Rodney Everett, Jr., industrial engineer. The team recommended 3D printing and the rest as they say, is history. The additive process’s ability to print custom manufacturing aids critical to tooling has become an important part of the company’s production process and has left engineers at the century-old company embracing the future of manufacturing with 3D printing.
“There’s no end in sight to what we think 3D printing can do for us. We plan to incorporate it into our production facility as much as we can going forward. The balance of strength and surface finish is unique to Stratasys equipment and materials” — Rodney Everett Jr, Dixon Valve & Coupling Company
Before their first 3D printing system, the company used traditional manufacturing processes to produce new tooling. “We produce hundreds of these parts. We now use 3D printing to rapidly and efficiently produce a variety of tools that aid in the manufacturing process,” said Everett. One of the major benefits of adopting additive manufacturing was that the cost was a direct representation of the exact amount of material needed, as opposed to the complexity of the design.
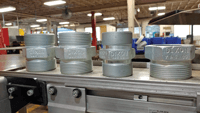
Behind-the-Scenes Workhorse
The Advanced Manufacturing Engineering Department introduced the Mojo 3D printer from Stratasys and quickly gained proof of concept for printing of its gantry locators that allowed robots to reliably load parts. As a result, Dixon Valve was able to reduce both material and labour costs of producing the gantry locators. he next step was passing the technology on to its tooling department to print fixtures and jaws. Gantry locators and fixtures and jaws continue to be Dixon’s two 3D printing mainstays. “We found we could improve our manufacturing support by incorporating 3D printing,” said Everett. We have used 3D printing to reduce the cost of manufacturing.
Dixon Valve was not looking to produce production parts via 3D printing, but wanted a product that could withstand repeated use on the production floor. “The big difference between rapid prototyping and production-grade parts is reliability and strength,” said Everett. “The Mojo provided a balance between economical printing and structural strength. We’ve combined rapid prototyping with production. The Mojo does both.” According to Everett, “There’s no end in sight to what we think 3D printing can do for us. We plan to incorporate it into our production facility as much as we can going forward. The balance of strength and surface finish is unique to Stratasys equipment and materials.” Dixon part held in place by 3D printed grippers that maximize the gripped surface area, creating a stronger holding force.