FreeFoam™
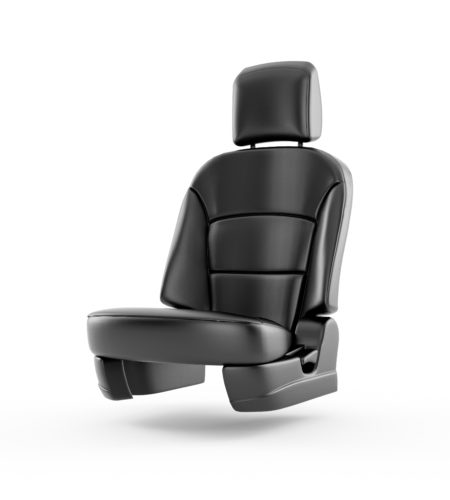
ETEC DLP
FreeFoam™
Produce durable and dimensionally accurate closed cell foam parts without tooling
FreeFoam™ is an expandable photopolymer resin that contains dispersed heat-activated foaming agents that can be 3D printed into parts with Digital Light Processing (DLP) 3D printing technology. After printing, FreeFoam parts are briefly placed into an oven which creates closed cells that expand the part from 2 to 7 times its original size.
A Revolution in the
Foam Industry
Remove the barriers and waste associated with
traditional foam manufacturing
FreeFoam resin enables a range of benefits where foam is prevalent, including in the automotive, furnishing, footwear, and sporting goods industries. With the ability to 3D print closed-cell foam parts without tooling, you are able to reduce waste and increase design complexity and part performance. FreeFoam will be available in a range of grades and is 3D printed similar to other photopolymer resins using Digital Light Processing (DLP) technology.
Applications
FreeFoam Process Workflow
3D printing foam parts with FreeFoam material has a similar workflow to other DLP resins.
DESIGN + PRINT
Design complex foam lattice structures with any design engine
and 3D print the parts on the ETEC Xtreme 8K DLP 3D printer
CLEAN + POST PROCESS PARTS
Remove excess resin from the 3D printing process
PLACE PARTS IN OVEN
Heat parts in an oven at 160-170°C (320-340°F). Parts expand 2-7 times the original size, depending on material grade, in minutes
FOAM PARTS ARE COMPLETE
Foam parts are complete with the right density and sizing
Material Highlights
Material Characteristics
Hardness (Shore A) –
60 ± 10, ASTM D2240
Volumetric Expansion Factor (m³/m³):
3.6 +/- 0.3, A3D Internal
Expanded material density (g/cm³):
0.28 +/- 0.04, A3D Internal
Tear Strength (kN/m):
> 10, ASTM D624 Die C
Uses
Foam replacement
Cushions, padding, and support
Shock and pressure absorbing applications
Footwear, apparel and consumer goods
Packaging and transport
Seating, furniture and mattresses
Industries
Industrial goods
Consumer goods
Healthcare
Education
Aerospace
Transportation and Automotive
Performance Scale
Strength to Weight Ratio | |
Flex and Compression | |
Tear Strength |
Material Color
Technical Specifications
Standard/Test Method |
Value |
||||
Hardness (Shore A) |
ASTM D2240 | 60 ± 10 | |||
Volumetric Expansion Factor (m³/m³) |
A3D Internal | 3.6 +/- 0.3 | |||
Expanded material density (g/cm³) |
A3D Internal | 0.28 +/- 0.04 | |||
Elongation at break (%) |
ASTM D638 Type V | 125 ± 25 | |||
Tensile Strength (MPa) |
ASTM D638 Type V | > 4 | |||
Tear Strength (kN/m) |
ASTM D624 Die C | > 10 | |||
Operating temperature (°C) |
ASTM D4065 | -55 to 105 | |||
Compression Set (%) @ 25°C |
ISO 1856-A | < 15 | |||
Volatile Organic Compounds (VOC) (µg/g) |
GMW-15634 | < 400 | |||
Semi-Volatile Organic Compounds (SVOC) (µg/g) |
GMW-15634 | < 250 | |||
Burning Rate (mm/min) |
UL 94-HB | < 95 |