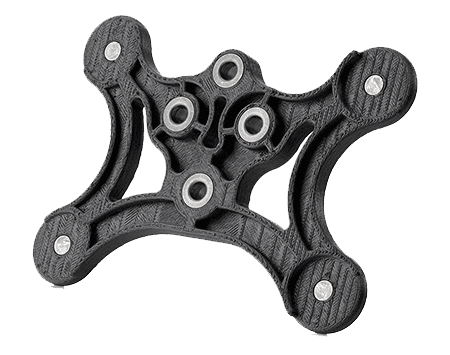
High-Performance Prototypes That Are Light-Weight And Carbon-Fiber Reinforced
Nylon 12CF delivers the highest strength and stiffness-to-weight ratio of any our FDM materials, suitable for markets like aerospace, automotive, industrial & recreational manufacturing
Overview
Nylon 12CF is an FDM thermoplastic that is filled with carbon to provide structural characteristics. Build high-performance prototypes that stand up to the rigorous testing required of production parts. The combination of Nylon 12 resin and carbon fiber produces the strongest thermoplastic in FDM technology as it boasts the highest flexural strength of FDM thermoplastics. Its unique stiffness and strength allows manufacturers to replace metal components in jigs, fixtures, and production parts.
Material Performance
FDM Nylon 12CF, a carbon-fiber reinforced thermoplastic, meets the demanding needs of the production environment, allowing the replacement of metal tooling for applications such as forming and end-of-arm tooling
IZOD IMPACT,
NOTCHED
85 J/m XZ axis
Heat Deflection
Temperature
143°C
Flexural
Strength
142 MPa XZ axis
58 MPa ZX axis
Tensile
Strength
63 MPa XZ axis
29 MPa ZX axis
Material Highlights
Characteristics
- Lightweight strength, carbon-fiber reinforced
- Impact-resistant
- Chemical-resistant
- Dimensionally stable
Options
- Available in Black
- Compatible with Fortus 450 systems only
Uses
- Drill guides
- Press-fit inserts
- Tough functional prototypes
- Jigs and fixtures
- Tooling
- Production parts
Advantages
- Toughest FDM material
- Carbon-fiber reinforced
Performance Scale
Strength | |
Flex | |
Aesthetics | |
Speed |
Material Colours
Technical Specifications
Mechanical Properties | Test Method | English XZ Axis | English ZX Axis | Metric XZ Axis | Metric ZX Axis |
Tensile Strength, Yield (Type 1, 0.125”, 0.2”/min) | ASTM D638 | 9,190 psi | 4,170 psi | 63.4 MPa | 28.8 MPa |
Tensile Strength, Ultimate(Type 1, 0.125”, 0.2”/min) PSI | ASTM D638 | 10,960 psi | 4,990 psi | 75.6 Mpa | 34.4 MPa |
Tensile Modulus(Type 1, 0.125”, 0.2”/min) PSI | ASTM D638 | 1.1 Msi | 0.33 Msi | 7515 MPa | 2300 MPa |
Tensile Elongation at Break(Type 1, 0.125”, 0.2”/min) % | ASTM D638 | 1.9% | 1.2% | 1.9% | 1.2% |
Tensile Elongation at Yield(Type 1, 0.125”, 0.2”/min) % | ASTM D638 | 0.9% | 1.1% | 0.9% | 1.1% |
Flexural Strength(Method 1, 0.05”/min) PSI | ASTM D790 | 20,660 psi | 8,430 psi | 142 MPa | 58.1 MPa |
Flexural Modulus(Method 1, 0.05”/min) PSI | ASTM D790 | 1.5 Msi | 0.3 Msi | 10,620 Mpa | 1830 MPa |
Flexural Strain at Break(Method 1, 0.05”/min) PSI | ASTM D790 | 3% | 3% | 3% | 3% |
IZOD Impact, notched(Method A, 23 °C) ft-lbf/in | ASTM D256 | 1.6 ft-lb/in | 0.4 ft-lb/in | 85 J/m | 21.4 J/m |
IZOD Impact, un-notched (Method A, 23 °C) ft-lbf/in | ASTM D256 | 5.8 ft-lb/in | 1.6 ft-lb/in | 310 J/m | 85 J/m |
Thermal Properties | Test Method | English | Metric |
Heat Deflection (HDT) @ 264 psi | ASTM D648 | 289°F | 143°C |
Melting Temperature | 433°F | 223°C |
Electrical Properties | Test Method | Value |
Volume Resistivity (kOhms) | ASTM D257 | 5.4E+03 – 3.9E+04 |
Melting Temperature | ASTM D257 | 3.3E+03 – 6.9E+04 |
Other | Test Method | Value |
Specific Gravity | ASTM D792 | 1.15 |