Desktop Metal® Production System™
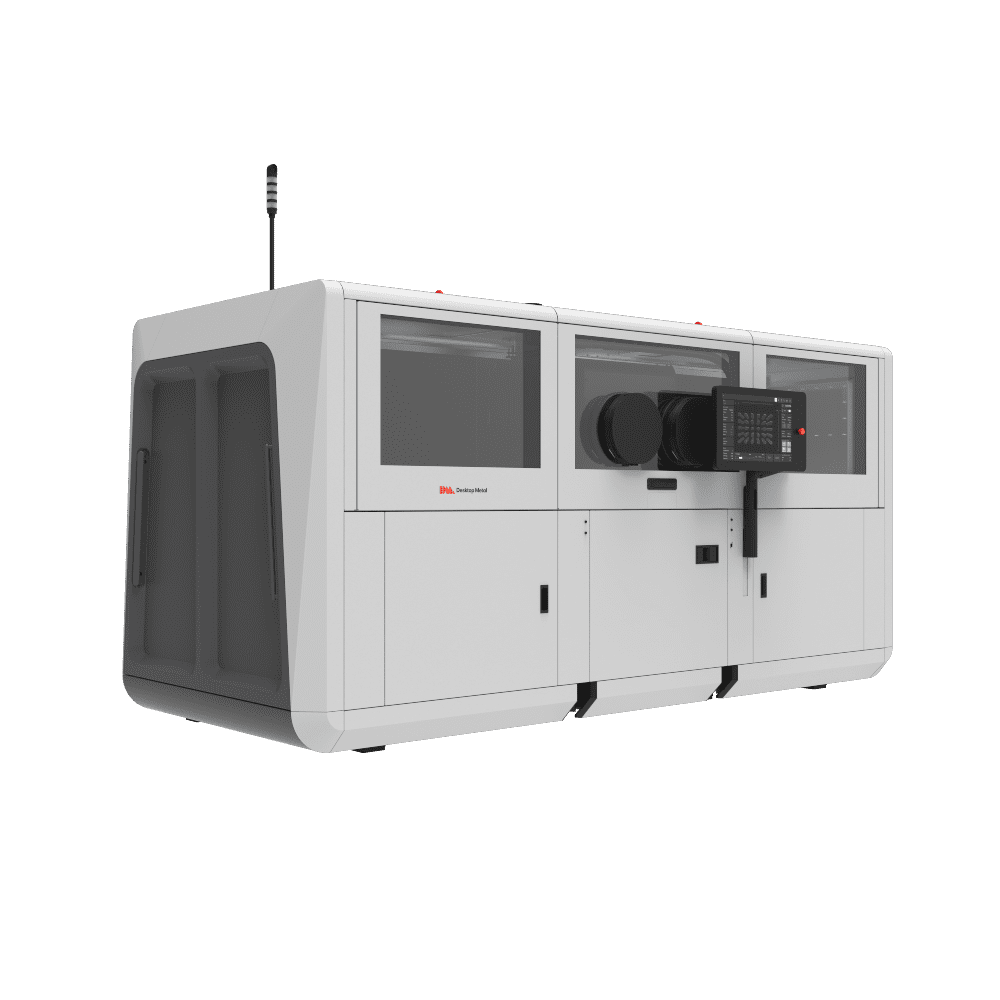
DESKTOP METAL®
Production P-1 and P-50
High-speed, high-resolution metal additive manufacturing
The Desktop Metal P-1 and P-50 Production 3D Printers are the first metal additive manufacturing systems designed for mass production. Powered by single-pass binder jetting technology, the Production System is the fastest way to produce complex metal parts at scale.
Additive Manufacturing at Scale
The P-1 and P-50 Production Systems from Desktop Metal are the first metal 3D printers designed for mass production. Powered by single-pass binder-jetting technology, the Production System enables the speed, quality, and cost-per-part needed to compete with traditional manufacturing processes.
Speak with one of our additive manufacturing specialists today to see if the Production System is right for your production workflow.
Key Features
How it Works
A single-pass starts in the powder spreader where a metering system deposits metal powder and a compacting system forms a layer as thin as a human hair. The print bar follows jetting droplets of a binding agent, millions are jetted pers second binding metal powder to form high-resolution layers. Anti-sintering agents are then deposited, making it possible for supports to fall off after sintering, saving hours of post-processing.
Depowder
When the printing is complete, the build box is transferred to crosslink for drying and strengthening of the binder.
The cycle continues with transferring the box to depowder, where the loose powder is removed and the parts are prepped for the sintering (brown parts).
Sinter
Once printed, the brown parts are densified in a microwave enhanced furnace. It combines conventional heating with microwaves to speed up sintering. A closed-loop thermo control system regulates temperatures in real-time as parts are heated to just below their melting point. Binder is removed and metal particles are fused to form a dense solid.
Exceptional Part Quality
High-Resolution Printing
The Production System’s bidirectional printing speed is combined with native 1200 DPI industrial inkjet heads that provide unparalleled feature resolution that is not possible to obtain through laser melting-based approaches.
Uniform print bed
Now, with the Production System and the proprietary constant wave spreading technology of single-pass jetting (SPJ) it is possible to maintain a consistent powder wave in front of the compaction roller during printing, which enhances the density uniformity across the powder bed.
Dense and strong metal parts
The metal parts printed with the Production System have a density up to or exceeding 99%* without the need for infill or a solvent debind step. The metal parts have similar properties in terms of strength with those resulted from castings.
Repeatability. Print with Confidence
Anti-ballistic Technology
Desktop Metal’s Production System™ ensures repeatability through anti-ballistic technology, print bar redundancy, and optical print bed inspection in real-time. Due to the patented anti-ballistic technology, engineers can reduce powder bed disturbance. This leads to reducing significantly the variability in the 3D printing process while increasing the longevity of the print bar.
Print Bar Redundancy
By using an anti-banding mechanism in which the print bar is re-aligned between layers, ensuring reliable binder deposition and suppressing defects that would otherwise affect final part quality, you can achieve full print bar redundancy. This mechanism helps with excluding hard, nozzle-based redundancy which translates into improved maintenance accessibility.
Live Optical Print Bed Inspection
The Production System™ is equipped with an overhead camera that monitors each layer using multi-angle imaging to detect print defects and nozzle performance during printing, which makes it easy to conduct parts inspection and build audits, extremely important with additive manufacturing in production environments.
Discover a cleaner and more efficient way to smooth and polish metal parts
Excellent Profitability
The DM Production System is ideal for producing complex, high-performance metal parts at high volumes. As tooling is not required, the printer can outperform traditional manufacturing processes such as casting while benefiting from additive manufacturing technology like mass customization.
In the time it takes laser-based processes to produce for example just twelve impellers, Desktop Metal’s single-pass jetting technology would have produced over 500. At up to 100 times faster than existing technologies, the Production System unlocks the cost-per-part needed for mass production.
Low-cost MIM Powders
The Production System is compatible with common MIM powders as well as a variety of other materials from the market from any reliable supplier. By making the SPJ process compatible with the more common metal powders already widely used by the Metal Injection Molding industry, the Production System™ has a mature supply chain and standards available for its raw materials.
Moreover, over 95% of the loose powder recovered during the process can be recycled, thus adding cost savings while reducing waste.
Fast Printing
The Production System™ has the capability to make parts faster, cheaper, and more complex than ever before. The system is capable of printing at speeds of up to 12,000 cubic centimeters per hour, more than 100 times faster than quad-laser metal printers and over four times faster than the closest binder jetting alternative.
The Productions System™ makes it possible to produce thousands of parts in a single print run, with prices and production rates that rival processes like casting, forging, and machining. The bi-directional, Single Pass Jetting™ (SPJ) print technology utilizes each pass of the print carriage to build parts, achieving the print speeds of up to 100x those of laser powder bed fusion systems.
Compact 3D Nesting
The 3D nesting of the printed parts is an important feature of the Production System™ printer. As parts are being printed, they are surrounded by loose powder to enable full use of the build envelope and higher productivity per build. This is possible thanks to the tooling-free binder jetting 3D printing process in which parts do not require welding to a build plate. They are arranged by software-defined positioning to maximize the build area in all axes for high-throughput builds.
Production System™ comes with the Fabricate™ software.
Materials
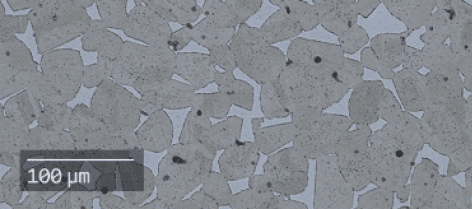
17-4 PH Stainless Steel (DM Production System)
Material: 17-4 PH Stainless Steel
17-4 PH stainless steel is a precipitation hardening steel used in a wide range of industrial applications including those with mildly corrosive environments and high-strength requirements.
Specs
- Yield strength (MPa): 655 ± 26 [as sintered]
- Ultimate tensile strength (MPa): 900 ± 20 [as sintered]
- Elongation at break (%): 10.9 ± 0.9
Application
- Manufacturing machinery
- Chemical processing
- Food processing
- Pump components
- Valving
- Fasteners
- Jigs and fixtures
Technology/Process
Binder Jetting Technology – Production System P1 & P50
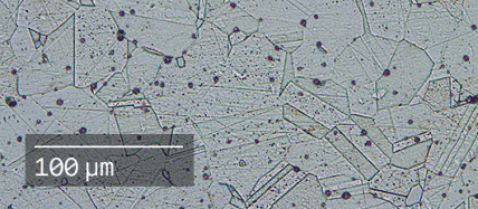
316L Stainless Steel (DM Production System)
Material: 316L Stainless Steel
Characterized by its corrosion resistance and performance at both high and low temperatures, 316L stainless steel is a fully austenitic steel ideal for harsh environments.
Specs
- Ultimate tensile strength (MPa): 510 ± 7 [as sintered]
- Yield strength (MPA): 155 ± 5 [as sintered]
- Elongation at Break (%): 75.3 ± 4.0
Application
- Chemical and petrochemical processing
- Food processing
- Laboratory equipment
- Medical devices
- Marine
- Jewelry
- Power generation
- Petroleum refining
- Water treatment
- Pulp and paper manufacturing
Technology/Process
Binder Jetting™ Technology with Production System P1 & P50
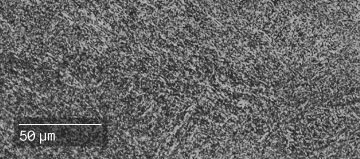
S7 Tool Steel (Production System)
Material: S7 shock-resisting air hardened tool steel
S7 is shock-resisting air-hardened tool steel characterized by its impact toughness with high hardenability as well as resistance to softening at high temperatures for hot work conditions.
Specs
After quench & temper:
- Ultimate tensile strength*: 1,790 ± 50 MPa
- Elongation at Break: 2.30 ± 0.75%
- Young’s modulus: 185 GPa
- Hardness (HRC): 51 ± 2
- Charpy impact strength**: 5.5 J
- Density: 7.5 g/cm3
* YS & UTS properties noted represent mean values across Xy orientation.
** Charpy impact specimens used were V-notched 10 x 10 mm.
Application
- Bending dies
- Cold forming dies
- Punches
- Shear blades
- Powder metal dies
Technology/Process
- Metal Binder Jetting
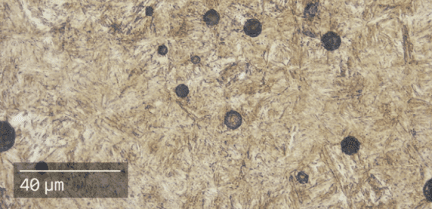
4140 Low-Alloy Steel (DM Production System)
Material: 4140 Low-Alloy Steel
4140 low alloy steel is versatile steel characterized by its toughness, high fatigue strength, and abrasion and impact resistance, making it great all-purpose steel for industrial applications.
Specs
- Yield strength (MPa): 1,455 ± 34 [quenched and tempered]
- Ultimate tensile strength (MPa): 1,880 ± 29 [quenched and tempered]
- Elongation at Break (%): 4.8 ± 1.1 [quenched and tempered]
Application
- Jigs and fixtures
- Automotive
- Bolts and nuts
- Gears
- Steel couplings
Technology/Process
Binder Jetting™ Technology – Production Systems P1 & P50
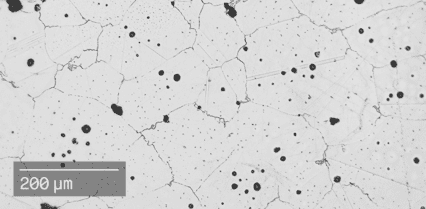
IN625 Nickel Alloy (DM Production System)
Material: IN625 Nickel Alloy
Alloy 625 is a nickel-chromium superalloy is known for its high strength, outstanding corrosion resistance, and ability to withstand extreme temperatures.
Specs
- Ultimate tensile strength (MPa): 695 ± 7 [as sintered]
- Yield strength (MPa): 295 ± 28 [as sintered]
- Elongation at Break (%): 63.0 ± 7.5 [as sintered]
Application
- Oil and gas
- Power generation
- Submarine components
- Cyrogenic environments
- Aerospace components
- High-temperature applications
Technology/Process
- Binder Jetting™ Technology Production System P1 & P50
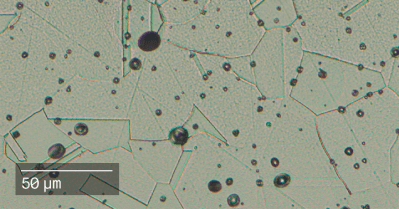
Nickel-Free Austenitic Stainless Steel (DM Production System)
Material: Nickel-free Stainless Steel
Known for its skin compatibility, excellent corrosion resistance, and good hardness and strength.
Specs
Mechanical properties, solutionized and quenched;
- Density: 7.70 ± 0.02 g/cc
- Hardness (HRC): 30.9 ± 0.9
- Surface vickers hardness*, 0.3kg load* (HV): 313 ± 12
- 0.2% Yield stress: 585 ± 12 MPa
- Ultimate Tensile Strength: 1020 ± 15 MPa
- Elongation: 56 ± 7.5%
- Young’s Modulus: 198 GPa
- Charpy Impact**: 400 J
* Surface hardness measured 100 microns from the surface in a polished section
** 5x10mm un-notched bar
Application
- Biological implants
- Medical devices
- Jewelry
- Watches
- Wearables electronics
Technology/Process
- Metal Binder Jetting
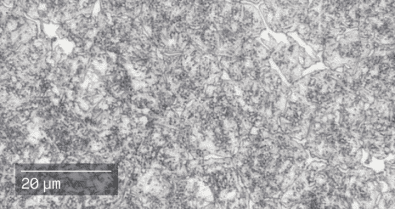
440C (DM Production System)
440C (High Carbon Martensitic Stainless Steel)
440C is a high carbon martensitic stainless steel. Thanks to its high carbon content, it has exceptionally high strength, hardness, and wear resistance, especially after heat treatment.
Specs
Mechanical properties, as sintered:
- Hardness (HRC): 58 ± 1
- Density: 7.64 g/cc
- UTS (Ultimate Tensile Strength): 1104 MPa, X-axis
- Elongation: 0.6%
- Charpy Impact*: 4.33 ± 0.5, XY axis
*Charpy impact specimens are 5x10mm cross-section un-notched. End-use material performance is impacted (+/-) by certain factors, including but not limited to part geometry and design, application and evaluation conditions, etc.
Application
It is an ideal material for various applications that require a long lifetime in demanding environments.
- Bearing components
- Manufacturing cutting tools
- Surgical instruments
- Valve components
- Molds and dies
Technology/Process
- Metal Binder Jetting
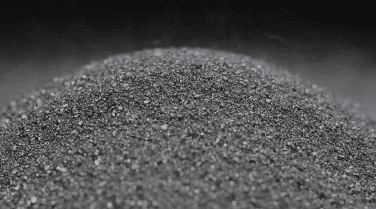
Silver (Ag) | DM Production System
Material: Silver (Ag)
Silver (Ag) is a precious metal often known for its aesthetic luxury appeal, but it also has the highest electrical and thermal conductivity and reflectivity of any metal.
Specs
Mechanical properties after sintering:
- Density: 10.02 (g/cm3)
- Surface roughness*:
- 2.89 ± 0.4 µm(top value)
- 7.36 ± 0.9 µm (training value)
- Ultimate tensile strength (UTS):
- 183.53 ± 28 MPa
- Average, largest pore size:
- 30, 35 µm
- Ring crush strength:
- 500 ± 100 MPa
*The measured surface roughness is the average of the top & trailing surface.
Material is open source and can be procured using Desktop Metal specification.
Application
- Jewelry
- Wearables
- Consumer electronics
- Communications
Technology/Process
- Metal Binder Jetting
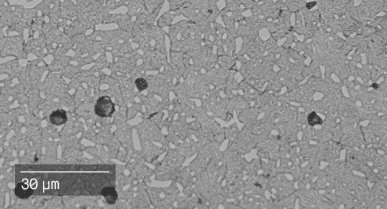
D2 Tool Steel (DM Production System)
Material: Corrosion Resistance Tool Steel
D2 Tool Steel is characterized by its high hardness after heat treatment, wear-resistance and compression strength, dimensional stability, and machinability when annealed.
Specs
- Transverse Rupture Strength (GPa): 2.2 ± 0.2, ASTM B528
- Quenched Hardness (HRC): 63, ASTM E18
- Tempered Hardness (HRC): 57, ASTM E18
- Charpy Impact Strength¹ (J): 1.2, ASTM E23
- Density: 7.70 g/cm³
- Surface Finish²: 3-8 (µm Ra)
¹Charpy impact specimens used were V-notched 10 x 10 mm.
²Surface roughness measured in Z direction after sintering & sandblasting.
Application
- Cutting components
- Conformally cooled injection moulding inserts and cavities
- Cold forming tooling components
Technology/Process
- Binder Jetting Technology – Production System P1 & P50
Open Material Platform
The Productions System™ is compatible with common MIM metal powders that offer the flexibility to manufacturers to buy the materials from an established, competitively priced supply chain.
Proprietary Binders
Experts and materials scientists at Desktop Metal have developed binders that support a broad array of alloys and that can maximize the rate of success through every stage of the binder jetting process. These binders make possible the jettability during printing, green part strength during depowdering, and clean burn-off prior to sintering.
Inert, closed powder environment
The advantage of the Production System is that it has a closed powder environment inerted to <2% Oxygen that safely supports both reactive and non-reactive metals in a controlled way. By being isolated from the ambient conditions, it makes the powder have consistent characteristics and quality, leading to part uniformity and repeatability.
Part Gallery
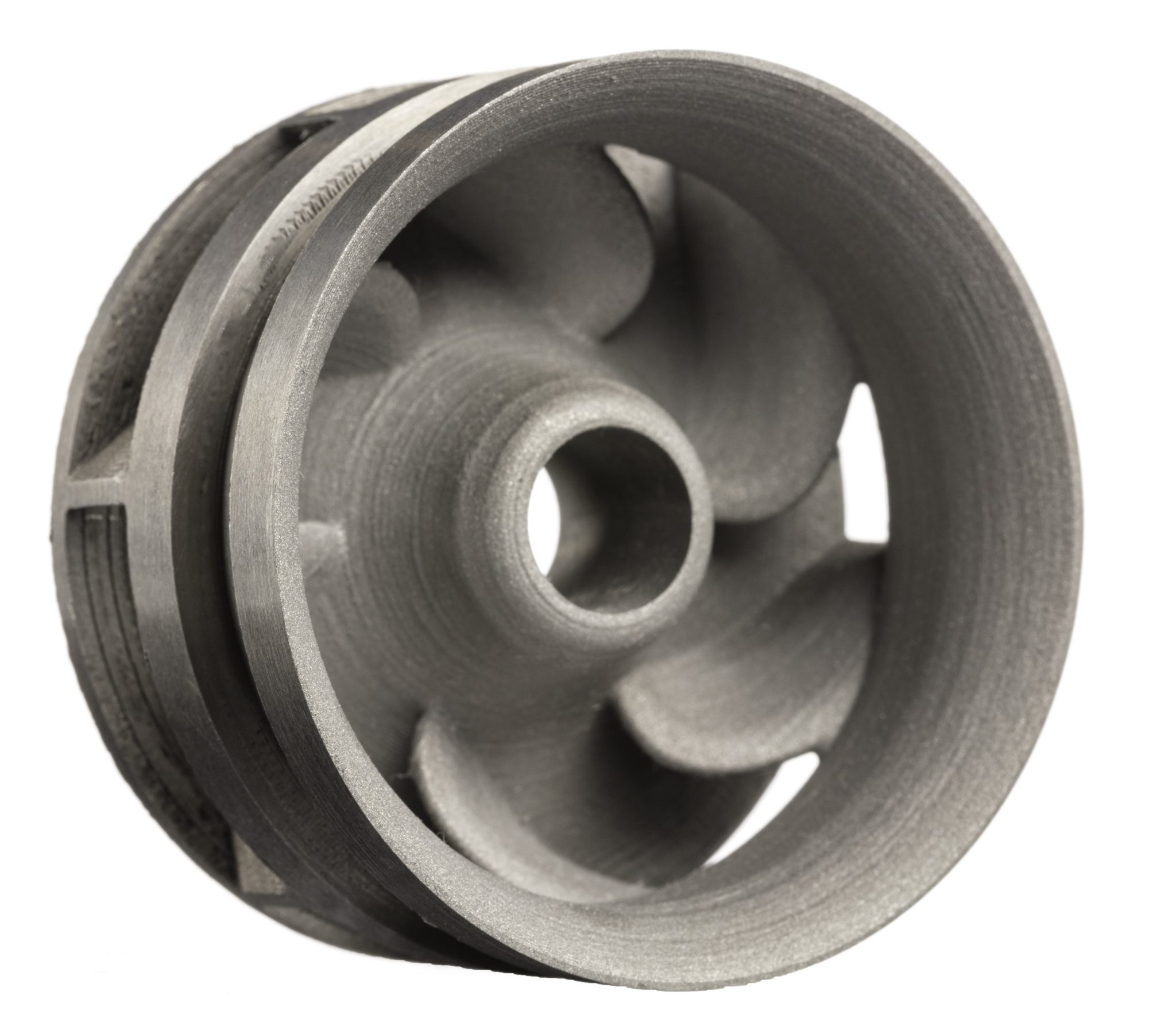
BMW Water Wheel
Manufacturing - Automotive 17-4 PH
The waterwheel is an integral part of BMW’s engine cooling system — see full description.
Full Description
This integral part of BMW*‘s engine cooling system was originally made of several plastic parts, so BMW redesigned it for printing on a laser-based system. However, the process was too slow and expensive for mass production.
The Production System ensures higher throughput, allowing the part to be manufactured at a competitive price.
*Part developed by German Touring Car Masters (DTM)
Specs
- Size (mm): 63 x 63 x 34
- Cost per part ($): 9.74
- Parts per build: 170
- Annual throughput: 63,230
Technology/Process
Single Pass Jetting™
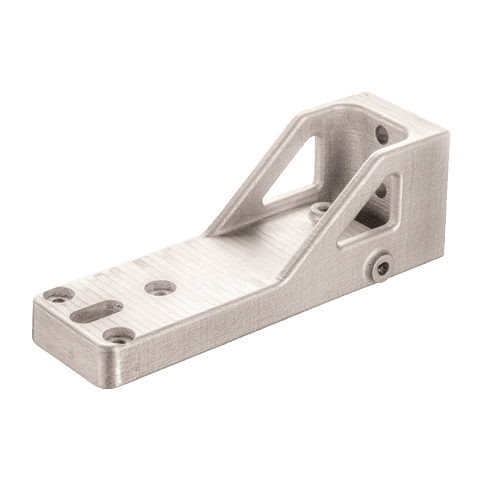
Automotive Fixture
Manufacturing - Automotive 17-4 PH
This custom manufacturing fixture was created for use on an automotive industry production line.
Full Description
Because of complex internal conformal cooling channels that span the base and the wall, this fixture would normally be manufactured in multiple pieces and welded together. Scaling up if the production volume increases would be too expensive and time-consuming.
Using the Production System, this fixture was printed as a single part with cooling channels intact, thus reducing part cost, lead time, and manufacturing complexity.
Specs
- Size (mm): 127 x 51 x 38
- Cost per part ($): 19.18
- Parts per build: 110
- Annual throughput: 41,500
Technology/Process
Single Pass Jetting™
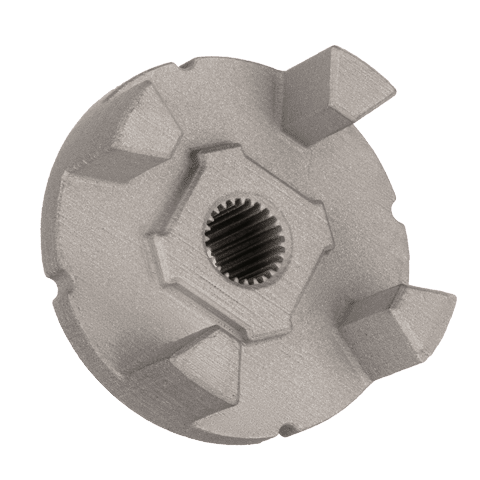
Power Steering Joint
Manufacturing - Automotive 17-4 PH
This part is designed to power transfer in an electric power steering system.
Full Description
This joint is used for power transfer between an electric power steering motor and the steering shaft in an automobile. The Production System made it possible for this part to be produced with no tooling, allowing for accelerated lead time and flexible design.
Specs
- Size (mm): 36 x 36 x 22
- Cost per part ($): 1.89
- Parts per build: 1,140
- Annual throughput: 470,424
Technology/Process
Single Pass Jetting™
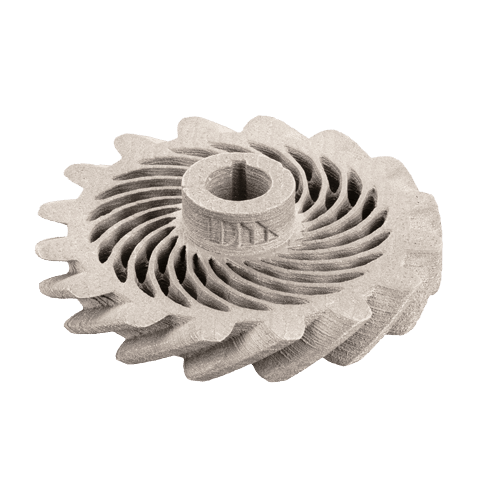
Ntopology Gear
Engineering Design 17-4 PH
The nTopology gear features a complex internal lattice structure only achievable via 3D printing.
Full Description
This part features a complex lattice structure used to lightweight the part while still providing strength.
With Production System™ you can manufacture complex geometries that cannot be produced any other way.
Specs
- Size (mm): 63 x 63 x 12.5
- Cost per part ($): 6.09
- Parts per build: 460
- Annual throughput: 165,980
Technology/Process
Single Pass Jetting™
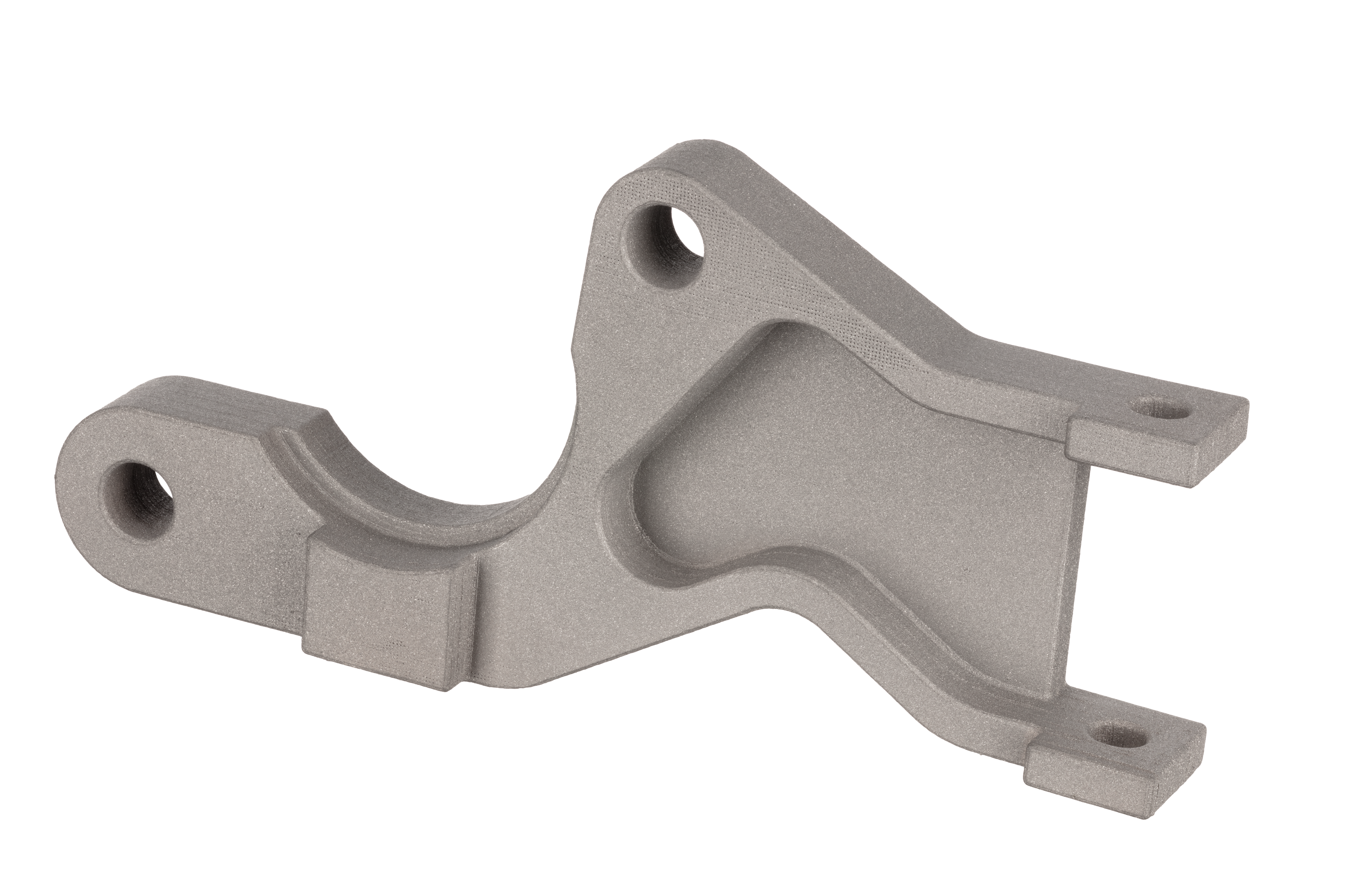
Parking Shift Bracket
17-4 PH Stainless Steel
This bracket is used in the parking brake assembly of a continuously variable transmission.
Full Description
With traditional powder metallurgy techniques, this part would need a complex die and multiple operations to be produced. The Production System™ enables the redesign of this part to consolidate an assembly into a single part with no tooling, and reduced lead times and costs.
Specs
- Size (mm): 93 x 44 x 12
- Cost per part: $2.84
- Parts per build: 680
- Annual throughput: 248,980
Technology/Process
- Binder Jetting Technology™
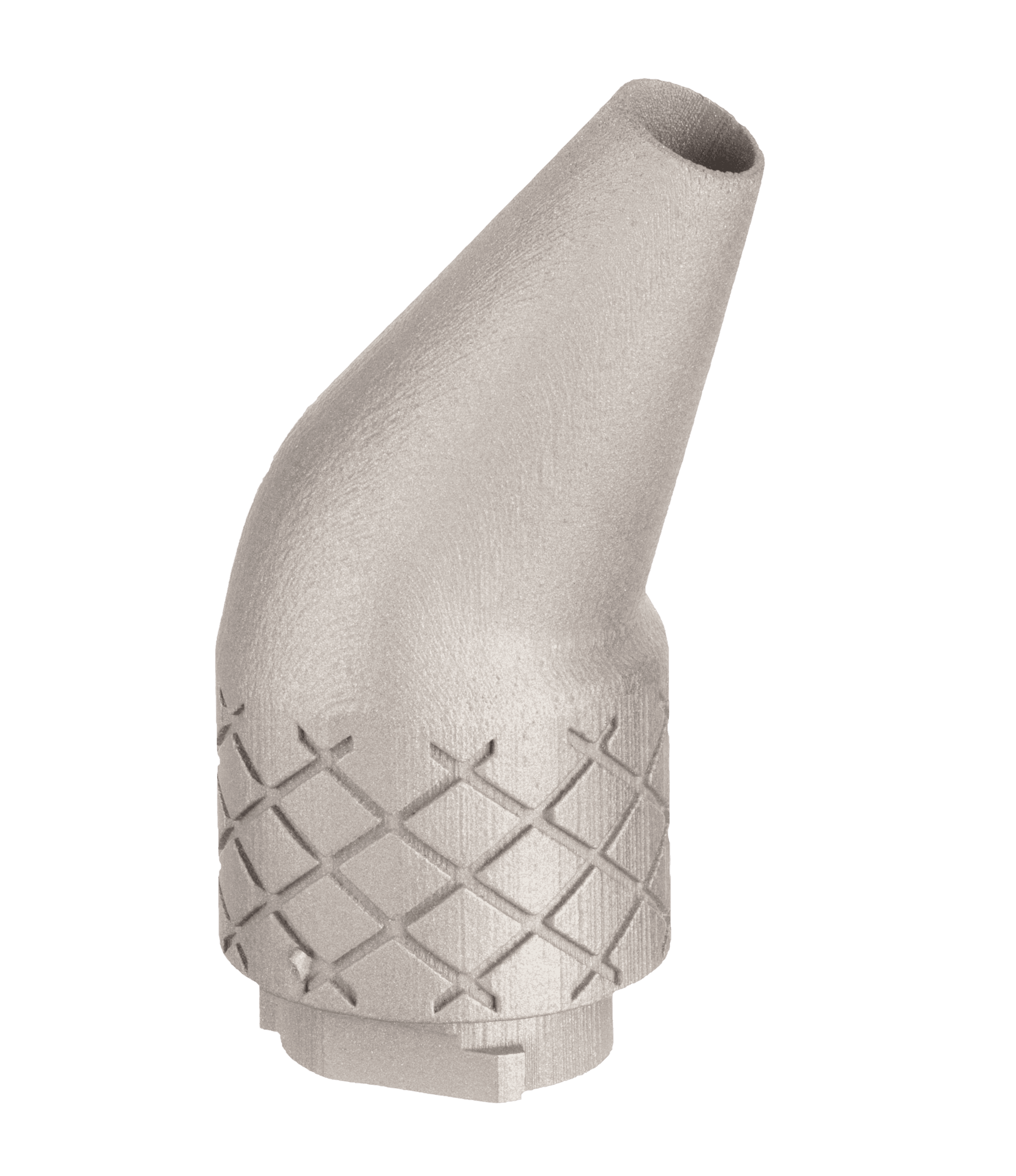
Surgical Tool Nozzle
Healthcare 17-4 PH
Nozzle used during surgery; customized for each patient.
Full Description
To produce this surgical nozzle in the traditional way, complex machining operations with multiple fixturing setups would be needed. With Production System™, all those steps can be eliminated which means diminishing costs.
This nozzle is specifically designed for each patient with a customized internal channel. With no tooling, the ProductionSystem allowed for this part to be mass customized and manufactured.
Specs
Size (mm): 27 x 47 x 21
Cost per part ($): 1.91
Parts per build: 860
Annual throughput: 400,140
Technology/Process
Single Pass Jetting™
Models
Production System 1 (P-1)
Production System™ 1 is an open platform binder jetting solution for process and materials development as well as serial production of small, complex parts. Just like the P-50, P1 supports both non-reactive and reactive metal powders using the same Single Pass Jetting™ technology. You can obtain the mass-production-level quality and consistency with enhanced process flexibility to support serial production or direct process transfers to the P-50.
Production System 50 (P-50)
The Production System™ P-50 is designed to be the fastest way to 3D print metal parts at scale, based on Desktop Metal’s patent-pending Single Pass Jetting™ technology.
Engineered with an inert environment to process low-cost MIM powders across non-reactive and reactive metals, the Production System™ P-50 offers the reliability and consistency required for high-volume, end-use applications.
P1 |
P50 |
|
Print technology |
Single Pass Jetting™ | Single Pass Jetting™ |
Print direction |
Uni-directional | Bi-directional |
Binder jetting module |
2 Piezo-electric printheads (4,096 nozzles) | 8 Piezo-electric printheads (16,384 nozzles) |
Max. build rate (65 µm layer thickness) |
1,350 cc/hr (82 in3/hr) | 12,000 cc/hr (732 in3/hr) |
Resolution |
1200 dpi | 1200 dpi |
Part tolerance |
± 0.5% | ± 0.5% |
Layer thickness |
30 µm - 200 µm (green) | 30 µm - 200 µm (green) |
Build box envelope |
200 x 100 x 40 mm (7.9 x 3.9 x 1.6 in) | 490 x 380 x 260 mm (19.2 x 15.0 x 10.2 in) |
Chamber environment |
CDA or Nitrogen inerting (<2% Oxygen) | CDA or Nitrogen inerting (< 2% Oxygen) |