Materialise e-Stage
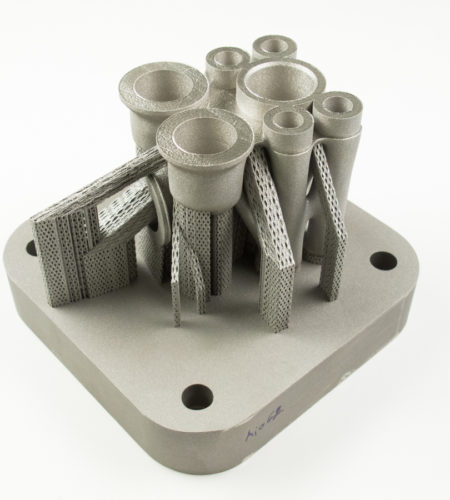
FILE PREPARATION AND OPTIMIZATION SOFTWARE
Materialise e-Stage
Automate the creation of support structures when 3D printing with resin and metal 3D printers
Materialise e-Stage is a powerful software tool built to maximize additive manufacturing productivity. Designed to work with both polymer resin and metal-based 3D printers, e-Stage will eliminate human error, reduce material usage, and shorten finishing work when creating support structures for complex geometries.
Save Time and Costs by Generating Minimalist Support Structures Automatically
Whether you have one machine or 50, by automating your support generation you will reduce material costs and save an impressive amount of time on support generation and post-production finishing. 3D printer users around the world use Materialise e-Stage with a wide range of Stereolithography , DLP, vat-photopolymerization, DMLS (direct metal laser sintering), and EBM additive processes to simplify the way their parts are manufactured.
With e-Stage you can:
- Reduce finishing time by 30%
- Decrease operation time by 95%
- Significantly reduce material consumption
- Eliminate human errors
- Increase success rate of builds and improve party quality
- Automatically create support structures that have minimal contact points and are needle-thin
- Maximize the build volume by nesting parts in the Z axis
Materialise e-Stage for Metal
Productivity at every stage
Reduce data preparation time for metal 3D printed builds by up to 90%, finishing time by up to 50%, and significantly reduce material use
Data Preparation
No need to spend too much time on editing metal supports.
Materialise e-Stage for Metal 3D Printing, saves time on support design up to 90%.
Build Process
Build process means placing the parts directly onto the platform, thus a faster build time. Afterwards, a wire EDM can be used to remove the parts from the build plate.
Support Removal
Up to 50% reduction in support removal time.
To ensure that you can easily break off support, Materialise e-Stage generates needle-thin contact points. The flexible grid structure makes it possible to remove parts from the support structure without any tools.
Finishing the Parts
Up to 20% reduction in part finishing time
With Materialise e-Stage, support structures are generated only where needed and even avoid contact with the part as much as possible to keep finishing work to a minimum.
Metal Production Improvement
Reduce the risk of build crashes
Since the support generated by e-Stage is created automatically, human errors are excluded.
Every surface that should be supported will be supported. The software also takes into account the force of the recoater (‘horizontal top load’ parameter) in order to prevent crashes caused by the recoater. In addition, it will reinforce the support connections of tall, thin parts to ensure a proper stabilization and prevent deformations while building. You can change the size of these connections in the parameter sets (‘horizontal connection height’ parameter).
Lower the powder consumption
Using the support volume estimation function, you can measure how much material is used. It is always less than it seems due to the lightweight nature of the scaffolds. By using gusset parameters, you can force part-to-part connections in order to lower the powder consumption even more. The support structure of this vacuum gripper was reduced by 63% when applying gussets. In addition, printing gussets requires less time than printing a full structure.
Maximize your build platform
Materialise e-Stage allows you to nest parts in the z-direction without touching part surfaces. You can generate one e-Stage file for all your parts, without taking into account the distance between the parts beforehand. One file per part is also possible. In that case, you can maximize your build space by limiting the width of the support structure with the ‘maximum offset around part’ parameter.
Increase the lifetime of your wire EDM
The open structure of e-Stage prevents powder from getting trapped. Since the wire EDM doesn’t get into contact with the powder, it wears less.
Fully control the support structure
In most cases, the support structure that e-Stage for Metal generates completely meets the needs of our users. In case you would like to change something, though, that is possible. You can still edit and remove the connection points after placement or even add new ones. Once the connection points have their final position, you can easily generate the corresponding support structure.
Materialise e-Stage for SLA and DLP
Productivity at every stage
Materialise e-Stage has a very powerful algorithm that leads to significant cost savings, especially labor costs. It has been proven that the data preparation time for Stereolithography builds can be reduced by up to 95%, whereas the finishing time can be reduced by up to 25%.
Time-saving
Spending hours editing support structure could be history. Materialise e-Stage is fully automated, due to an intelligent algorithm and extensive parameter set. Reduce the time spent on the support design up to 90%.
Less material
By using gusset parameters, you can force part-to-part connection in order to lower resin consumption and the build time of a part.
Up to 50% reduction in support removal time.
To ensure that you can easily break off support, Materialise e-Stage generates needle-thin contact points. It’s never been so easy with the support removal.
Up to 20% reduction in part finishing.
With Materialise e-Stage, support structures are generated only if it is the case. The structures will even avoid contact with the part as much as possible to limit finishing work.
Production Improvement for SLA and DLP
Reduce the risk of build crashes
Since the support generated by e-Stage is created automatically, human errors cannot occur. Every surface that should be supported, will be supported.
The software also takes into account the force of the recoater (‘horizontal top load’ parameter) in order to prevent crashes caused by the recoater. It will also reinforce the support connections of tall, thin parts to ensure a proper stabilization and to prevent deformations while building. You can change the size of these connections in the parameter sets (‘horizontal connection height’ parameter).
Decrease resin consumption
By using gusset parameters, you can force part-to-part connection in order to lower resin consumption and the build time of a part.
Improve resin drainage
Due to the open diamond structure of e-Stage, the resin is not trapped within the support structure.
Maximize your build platform
Materialise e-Stage allows you to nest parts in the z-direction without touching part surfaces. You can generate one e-Stage file for all your parts, without taking into account the distance between the parts beforehand. One file per part is also possible. In that case, you can maximize your build space by limiting the width of the support structure with the ‘maximum offset around part’ parameter.
Easily remove the build from the build plate
The notches in the foundation make it easy for a saw to go through the foundation (for SLA machines). A base plate can be created for a homogeneous distribution of the forces on the build plate. You can easily remove it afterward with a small tool (for DLP machines).
System Requirements
CPU |
CPUIntel® CoreTM i5 (2500, 2400) |
Memory |
Memory4 GB Dual Channel DDR3 SDRAM at 1333Mhz |
HD |
HD320 GB SATA hard drive (7200RPM) |
Video Card |
Video CardIntegrated Video, Intel® HD Graphics (1DP & 1VGA) |
Operating System |
Operating SystemWindows 7 Professional, 64-bit |