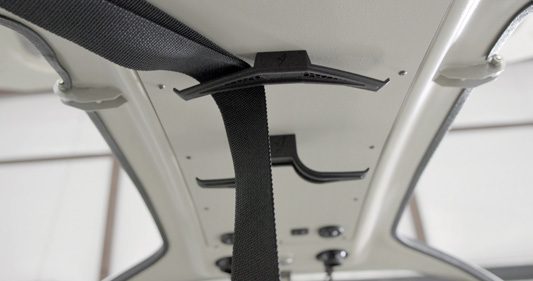
Aerosport Additive is an Ohio-based service bureau that produces prototypes and working models for the automotive, aerospace, military, electronics and consumer industries. This company turned to DLP technology to expand its portfolio.
Like many manufacturers, when it comes to producing rubber parts, Aerosport Additive had only two options: urethane casting for prototyping and low-volume production and injection molding for mass production. The first one is a multi-step process with higher costs per part. You need to create the mold master, the silicone mold and lastly, you have to cast the part – a slow and labour-intensive step. The second one involves long lead times, and high costs as tooling can easily require a month or more to produce, thus limiting the possibilities to change or refine the part.
Additive manufacturing offers a solution to all these challenges. Here’s why:
- it is tooling-free
- it eliminates long lead times associated with traditional manufacturing
- it has the ability to quickly print functional prototypes meaning more opportunities for design iteration.
Yet, fabricating rubber parts can sometimes be a challenge for additive manufacturing as well. While many materials, like TPU and TPA, could be used to produce flexible parts, matching the look, feel and performance of real rubber was all but impossible – until now.
Revolutionizing Rubber Parts Production
Adaptive3D, a Desktop Metal company, has developed Elastic ToughRubber (ETR) – a family of one-part, fast-curing photopolymer resins. With these revolutionizing materials, Aerosport Additive can now print a wide variety of rubber parts, from baffles to lattices to end-of-arm tooling and more. To produce those parts, the company has started with ETR 70, so named because it delivers parts with a Shore A70 hardness – similar to shoe soles or automobile tire treads.
That measure – tough enough for consistent use, yet soft enough to be pliable – marks a “sweet spot” for a broad range of applications.
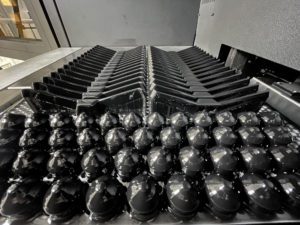
The perfect combination:
ETR resins & ETEC Xtreme 8K
The material is available exclusively on the ETEC Xtreme 8K printer. It features the largest build volume of any production-grade DLP printer, and it allows Aerosport Additive to 3D print everything from very large parts to thousands of small parts in a single build.
The system’s innovative, top-down printing method eliminates the peeling step required in traditional DLP, allowing the Xtreme 8K to deliver exceptionally fast print speeds and dramatically reduce lead times. By comparison, urethane casting may require as much as 10 days before a single part is poured, and months of lead time can be required to fabricate injection molding tooling. With the Xtreme 8K, however, Aerosport Additive can deliver parts in just days, potentially allowing the company to save enough time to add two full builds per day and take on additional jobs with the increased production capacity.

Aerosport Additive has years of experience with different additive technologies – including multi-jet fusion and SLA printers – and their decision to invest in the ETEC Xtreme 8K largely boiled down to one factor: innovative materials. And to 3D print rubber parts that could compete with traditionally-manufactured parts, the company needed to use Adapative3D’s Elastic ToughRubber, available on the Xtreme 8K only.
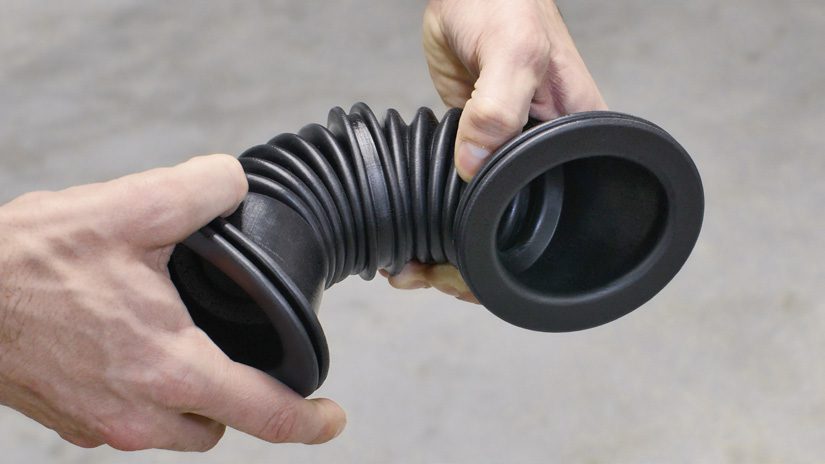