The famous, televised BattleBots is a robot combat tournament which summons teams of engineers worldwide to design, build, and control a robot. They must creatively demonstrate their engineering skills, strategy, and driving ability. Every robot is required to weigh no higher than 250 lbs with at least one independently-powered weapon. The robots challenge and fight one another in a closed arena that is confined by a bullet-proof glass, going directly up against one another in order to avoid elinination and reach the championship title.
It’s best to keep in mind that when designing a robot, teams must examine, and consider, several factors that will determine the robot’s ability to beat the competition, all while withstanding a wide range of obstacles that have been built into the arena. Some of the considerations are the following:
Weight
Precision of motion
Materials
Controlability
Impact resistance
Effectiveness of the robot’s weaponry
Each components design is important to the tobot’s all around performance while the limited development timeline leaves small room for iteration.
Team SawBlaze, which is made up of MIT engineering students and graduates, is a massive challenger whose robot’s weaponry includes a diamond abrasive rescue saw blade and a flame thrower. The blade sits on a controllable and rotating arm. The arm positions the saw at either the front or back of the robot. This stabilizes the machine while allowing a bi-directional offensive. Green flames at 350°C are released by the flame thrower in the direction of the SawBlaze’s target. This delivers a “slash and burn’ blow to the opponent.
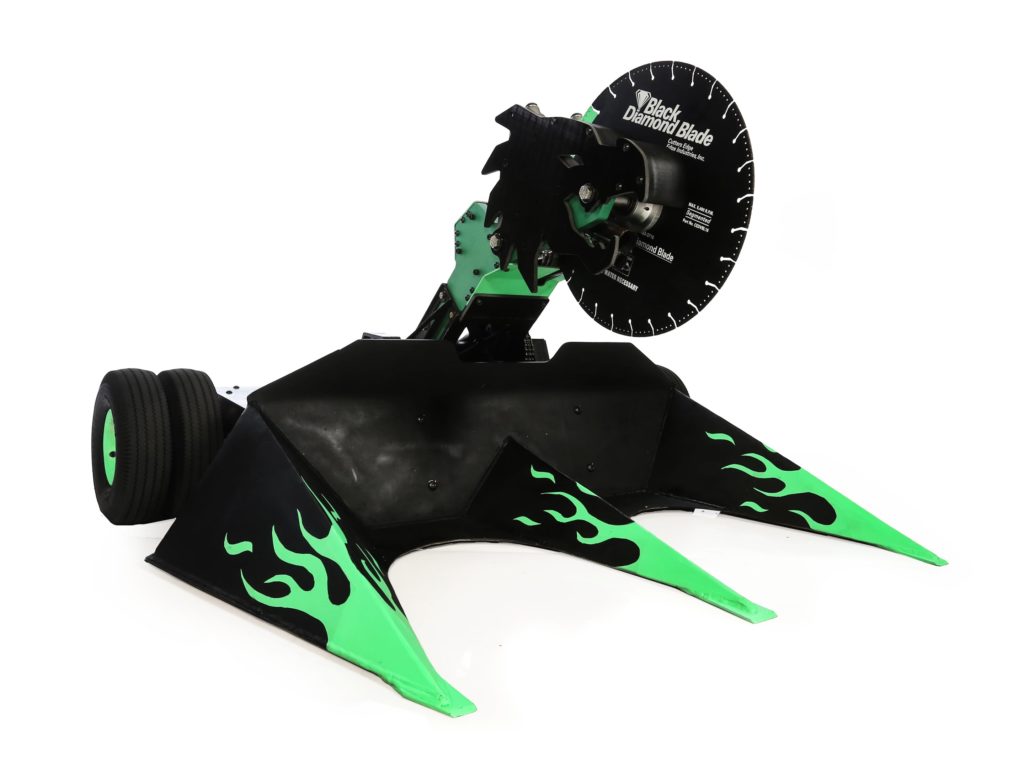
The Challenge
The 2018 season showcased the shortest build calendar ever, thus allowing nearly a month to construct and ship the robot. Every individual component plays a massive role in the robot’s potential to perform. Therefore, the more design iterations the team is able to produce prior to the final build, the better. Jamison Go, Mechanical Engineer at Desktop Metal, as well as SawBlaze team captain, noticed a possibility to better the benefits of metal 3D printing with the Studio System – including design flexibility, rapid iteration in-house, high-performance materials, and finally, minimized production costs, so that there’s more time spent fine-tuning custom parts for the robotic assembly.
“In contrast to most BattleBots robots that apply brute force, SawBlaze applies precision damage. This strategy is much more difficult to execute. Working against a limited development timeline, our processes must be extremely efficient in order to achieve an optimized and consistent strength-to-weight ratio as the robot moves and comes into contact with the competition.”
– Jamison Go, SawBlaze Team Caption
The Part
One of the very many components of the SawBlaze robot is the backstop; a sub-assembly which straddles, as well as protects, the blade. Many loads are applied during battle, the backstop requires stiffness, strength, hardness, corrosion, resistance, and heat resistance.
- As a structural component, it requires being able to resist bending and lateral motion; all while being as lightweight as possible.
- SawBlaze considered many fabrication processes in order to print the dual end pieces which would later be assembled with the metal cross-bar.
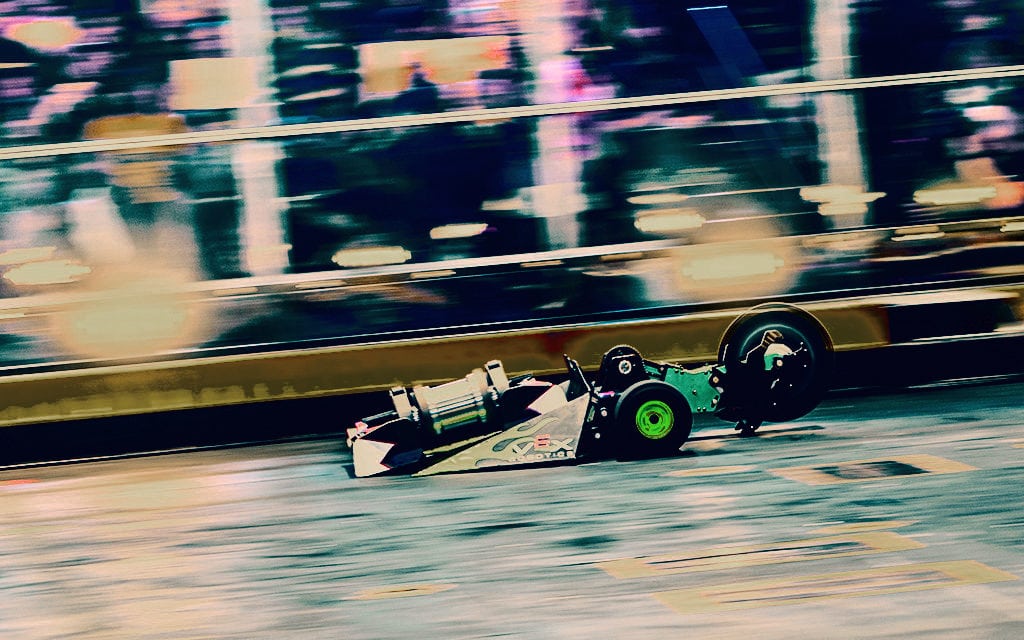
Process Comparison
Due to limited time-frame and budget, the fabrication method is crucial to consider, especially for custom parts like the backstop. Both cost and lead time introduced with third-party manufacturers leave nearly no room to iterate, while the design limitations of machining in-house would jeopardize part performance and introduce a crucial opportunity cost because of the number of manual steps deemed necessary.
The issue of achieving lightweight strength made the backstop an ultimate candidate for metal 3D printing. The team created the part using “cut-outs” and gained closed-cell infill throughout the part to eliminate excess material and reduce its weight in techniques which are impossible using traditional manufacturing methods.
Studio System |
CNC Service Provider |
DMLS Service Provider |
$56 |
$606 |
$1285 |
3 Days |
2-3 Weeks |
2 Weeks |
Both ends of the backstop were printed in AISI-4140 low-alloy steel using Studio System. Then, it was fastened to each end of a metal cross-bar.
The Results
The SawBlaze team found the ability to leverage the many benefits of in-house metal 3D printing in order to create a strong part that was arena-ready, all while slashing part cost by 90-95%, and reducing the part’s weight. The Studio System was used during the tournament to print backstop, which functioned flawlessly – withstanding repeated and varying stresses without failure. SawBlaze has achieved their many fights and won multiple battles – it’s very first win being a knockout in just 94 short seconds!
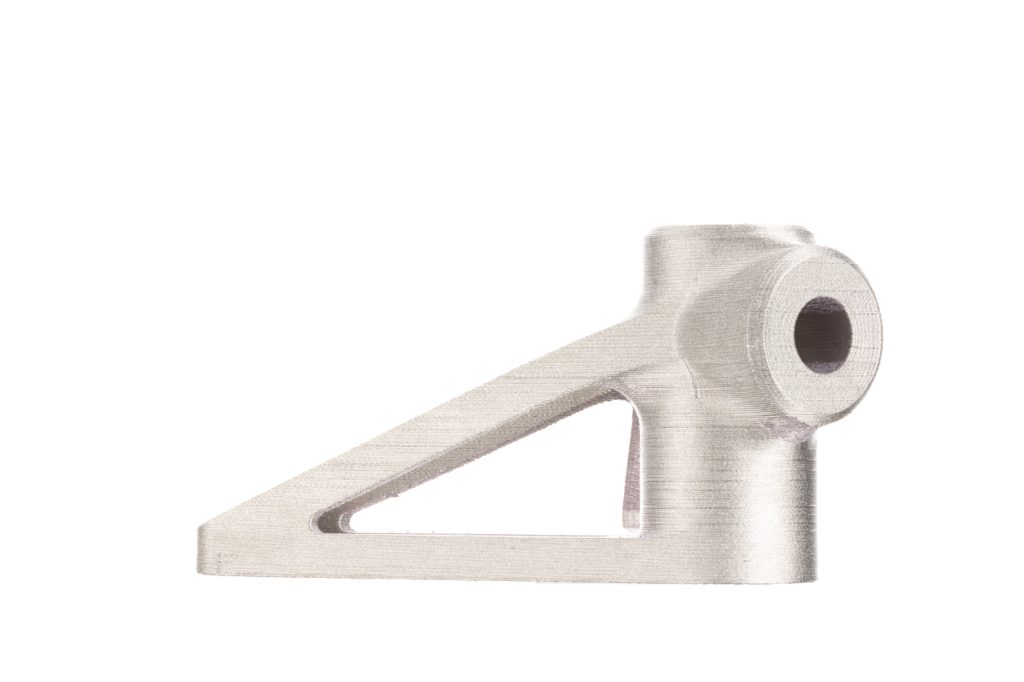
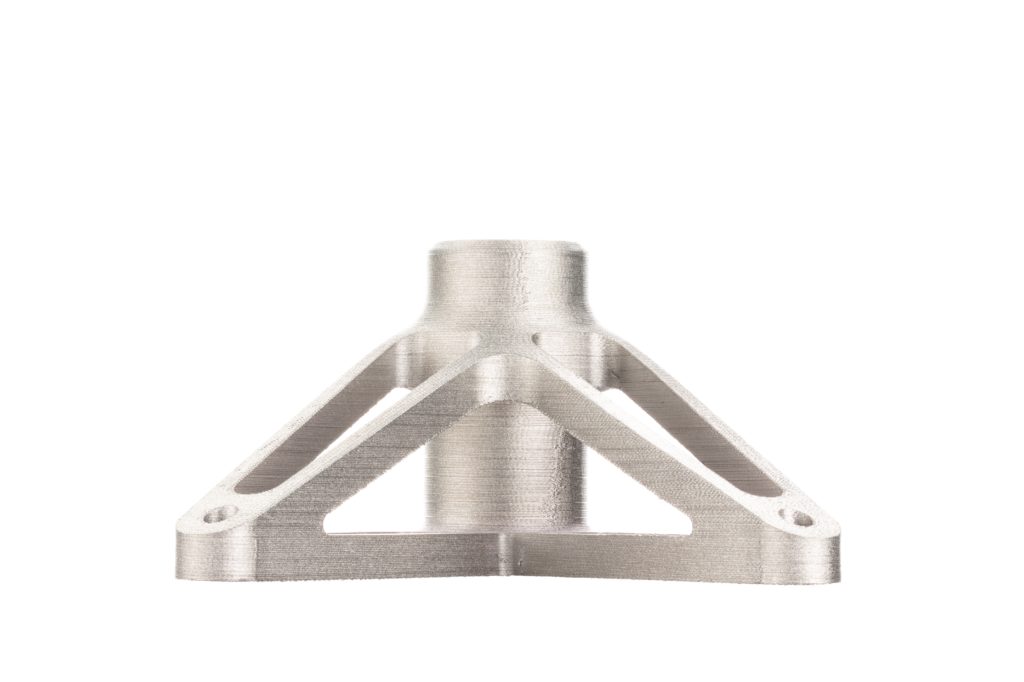
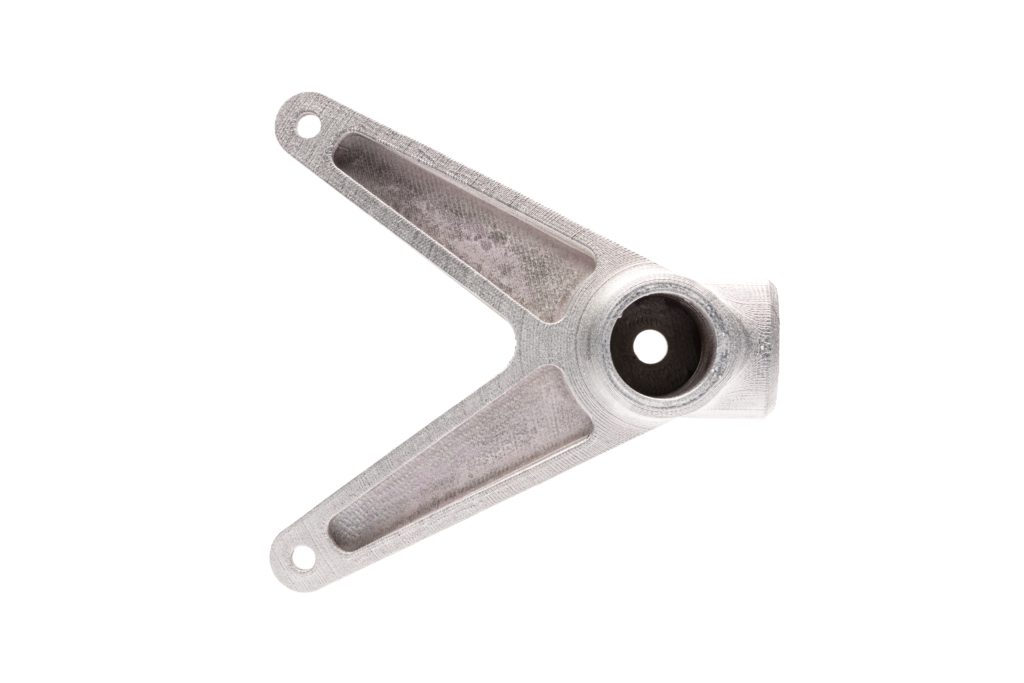