Last year, we wrote about how we helped the University of Waterloo’s Formula SAE team produce their best race car possible with the help of 3D printing. Today, we’re happy to share with you our collaboration with the Concordia University’s team of Mechanical Engineering students.
Based out in Montreal, QC, the school’s Mechanical Engineering team had set out to complete the engineering cycle from product development, manufacturing, and to testing & validation of the ergonomics and driver interface of a Formula SAE vehicle. As part of their senior design project, the students focused on improving the race car components such as the pedal system, seat and clutch of the driving interface. Their first challenge was determining the optimal placement for a driver within a Formula SAE chassis. Taking into account various positions for the pedal, steering wheel, seat, and headrest, the team went above and beyond to measure every little detail in an effort to improve ergonomics, reduce weight, and validate the entire system. The result was a 2-pedal system made entirely from aluminum and 30% lighter than previous iterations.
The Process
Utilizing 3D printing technology was the obvious choice for Concordia University’s Engineering team. Additive manufacturing provided the opportunity to explore new material combinations for optimizing design. Max Kassimov, a member of Concordia’s Mechanical Engineering and Formula SAE team told us, “Often times when working with ergonomics and human interfaces, the designs can become very intricate and have very weird shapes that are not as easy to manufacture using conventional materials such as metals. We decided that the best option would be to incorporate plastics for components that have direct contact with the driver and 3D printing allowed us that luxury without sacrificing ergonomics and the driver’s comfort”.
3D printing technology has helped the Formula SAE team explore a different approach to manufacturing tools and engineering processes. Proto3000 helped provide 3D printed pedal faces and hand clutch levers to allow the Concordia team to easily accommodate multiple drivers, minimize weight, and ultimately print a perfect model that maximized grip and comfort for their drivers.
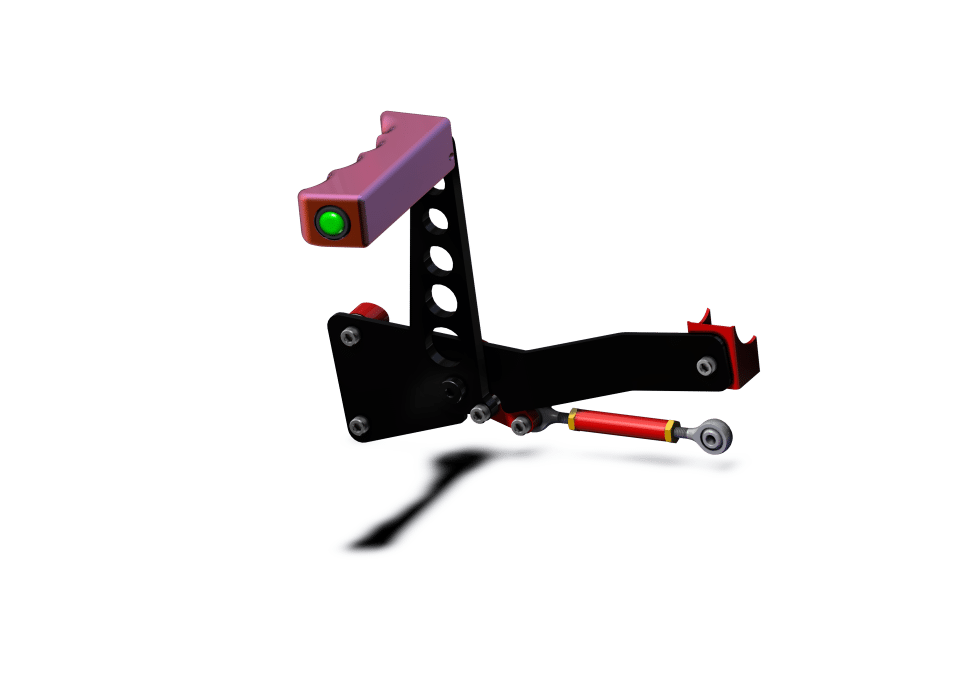
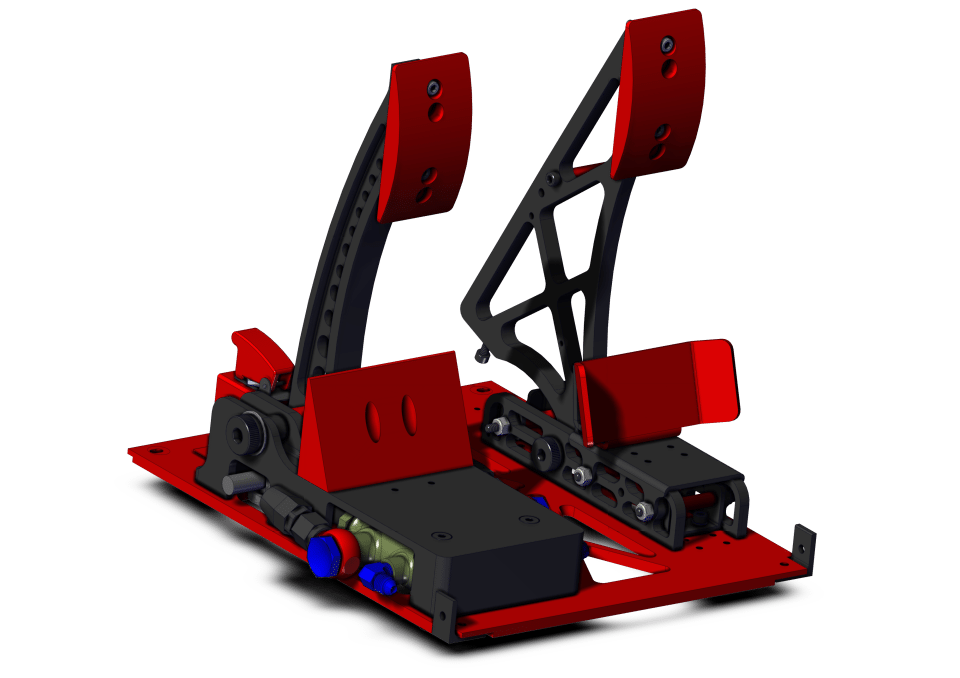
The Result
The team’s first test was conducted in Florida where their 3D printed parts were immediately tested and to their delight, they performed perfectly with sufficient grip. The 3D printed pedals were also subjected to a fatigue test where cycles of 100 to 450 lbs were applied a thousand times as the only point of contact between the pedal system and the actuation piston. Again, the parts survived without problems as a testament to the Engineering team’s design and the strength of the 3D printing material. Concordia’s SAE team even attracted the attention of other teams as the Florida International University are now beginning to look into 3D printing technology after seeing the polycarbonate prints in action. Kassimov states, “The polycarbonate material survived without any problems in the sunny and humid environment as the team returned to Montreal without any failures.. . Overall we were very happy with the 3D printed components and I have no doubt that the SAE teams of Concordia University will be continuing to use 3D printed parts in the future”
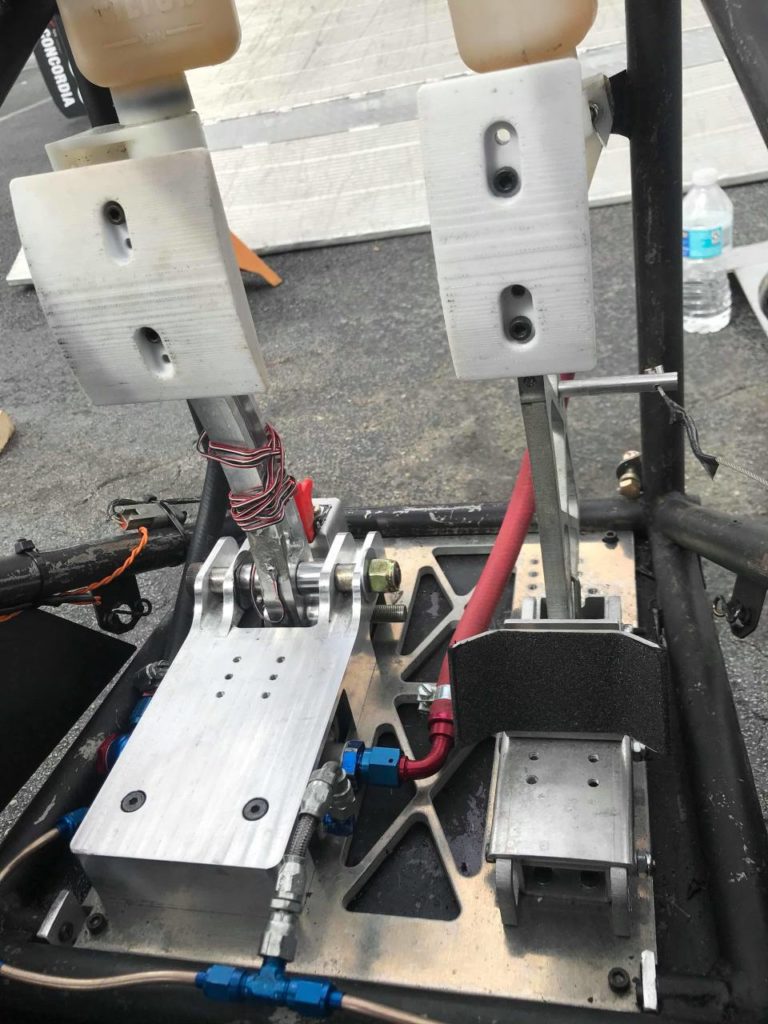
He adds, “working with Proto3000 was extremely easy as they were of great help. When we first approached them with our ideas and components, they quickly suggested the best materials we could use for each application and other alternatives. The team was great at communicating and were open to helping us and providing support”.