Supporting Product Development With the Stratasys F770
Sub-Zero Group, a pioneer in the manufacturing of customized and luxury home refrigeration, with built-in and integrated appliances, has taken productivity to a higher level with their newest addition of large-format 3D printers, the new F770 by Stratasys®.
And when we are talking about customized products, we surely mean the need for special design and prototyping. Doug Steindl is a Corporate Development Lab Supervisor at Sub Zero and his passion for additive manufacturing never let him down. And the new F770, based on the well-known FDM technology by Stratasys, confirmed once again how 3D printing has so many advantages when it comes to cut production costs, increase efficiency and quality standards.
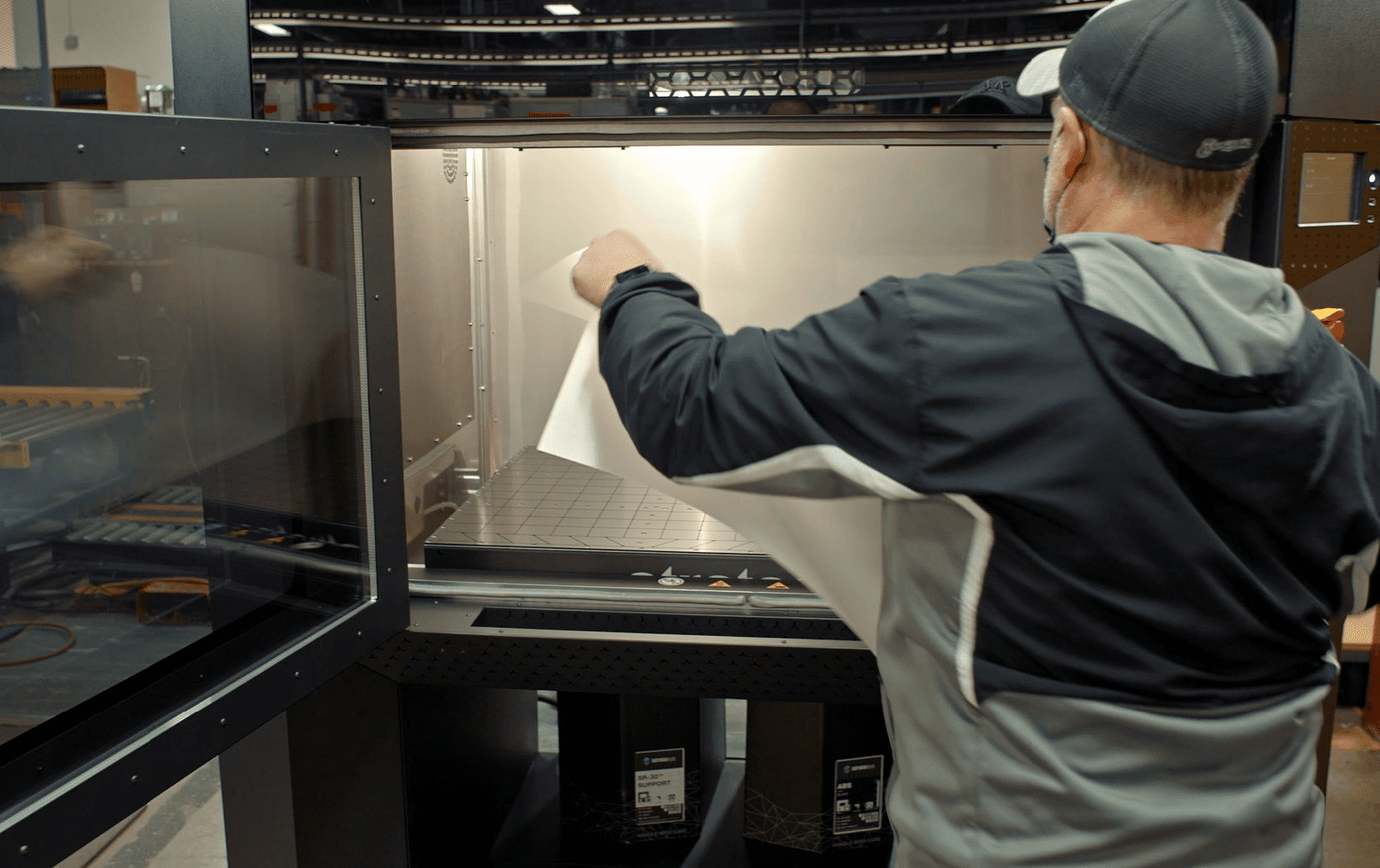
When it comes to discussing 3D printing technology, Steindl bluntly confesses: “To be honest, it’s my one love in our lab. It’s amazing what these things can do. And these printers are really, really important to us”.
Steindl supervises a team of six technicians whose role is to support the product development units of Sub Zero’s three brands – Sub Zero, Wolf and Cove by materializing ideas, concept models, prototypes, and manufacturing aids. Steindl’s lab is considered to be the epicenter of Sub Zero’s manufacturing, making it possible to create unique products at the highest standards while reducing costs. This lab includes everything that can be seen in a manufacturing facility: sheet metal forming, brake presses and machine tools. But the common denominator of this lab’s development process is its 3D printing capabilities.
Looking to Learn More About Tooling?
Download our guide to learn about the business drivers for adopting 3D printing for production tooling instead o traditionally fabricated tools.
The Bigger, The Better
In producing home appliances, the fabrication of large parts is self-implied and so are many of Steindl’s prototypes. When the 3D printer doesn’t have the capability of printing big parts, you have to invest more time and labour in post-processing. Before acquiring the Fortus 900mc™ and now the newest F770, Steindl had to print one large part into several pieces and then glue them together, or he had to outsource. Not having an in-house production capability equals to added time and costs. With Stratasys’ reliable large-format 3D printers, Sub Zero was always able to set free from the insecurity and the hassle resulted from outsourcing the 3D printing jobs.
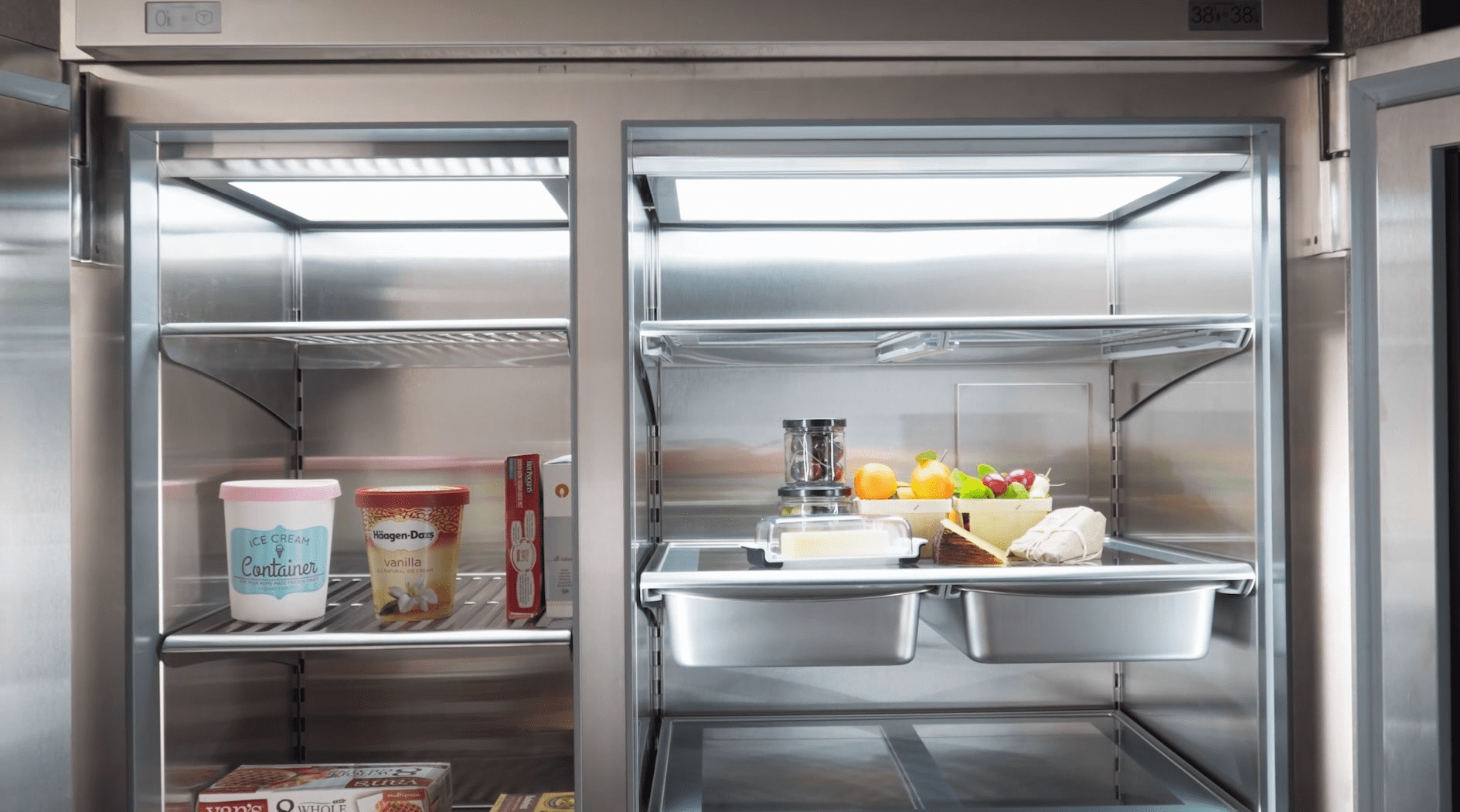
F770, the industrial-scale 3D printer, with over 13 cubic feet of build volume, is capable of printing 46 inches long parts and it is designed for an easy-to-use operation. There is no need for constant monitoring while the printer is operating, as F770 is equipped with a rapid change material canister with 200 cubic inches of filament. It is engineered to run up to 140 hours with no interruption.
“When I heard about the build size of the F770, I thought it could really be a nice addition to our lab,” says Steindl. “I think the 39 by 24 by 24 inch build size fits us very well. Big is always good – you can make small parts in a big machine but you can’t make big parts in a small machine,” he adds.
Cutting Productivity Costs
In Steindl’s opinion, the new F770 is an added capability that at the end of the day has a great impact on Sub-Zero manufacturing costs. He mentions that this 3D printer’s ability “to retain more work in-house represents a 30 to 40% cost savings”. And on top of that, the faster they can get a product out on the market, the better it is taking into consideration that Sub Zero’s lab is faced with new product builds every six weeks.
Proven Reliability
Sub-Zero is a consumer of Stratasys products for so many years now, and the efficacy and reliability that were gained in time, have given Steindl and his team the confidence to acquire the new F770.
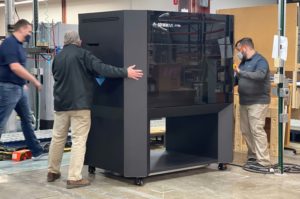
It’s one of the reasons Sub-Zero chose Stratasys FDM® printers over others, because they do their job, and let the lab’s technicians do theirs. With Stratasys equipment, we can program it, send it to the printer, start it and walk away, then come back at the end of the cycle. During all that print time, my guys can be doing other tasks.” explains Stendl. It’s just another example of how the F770 helps in a big way.