3D Printed Tooling- A Quick, Flexible Design Solution
The Hager Group production site in Saverne specializes in energy management systems and home automation- they are continuously working to improve their process and increase responsiveness by remaining innovative while also reducing their production time and keeping their costs low. In order to remain both innovative and productive, they decided to look to additive manufacturing as a means to accomplishing their company goals.
The Hager Group decided to purchase a Stratasys® FDM® 3D printer in order to easily and cost-effectively print parts that meet industrial requirements with advanced tooling. The company required a solution that was both safe and easy-to-operate so that they could keep up with production orders. The Hager Group selected the Fortus 380mc™ 3D printer– an industrial-level, high-performance 3D printer that allowed the company to utilize production-grade thermoplastics.
“At Hager Group, we need to create intricate parts — something that is time-consuming and costly with traditional machining methods, and not always feasible with just any 3D printing solution,” says Alexandre Callegher, Mechanical Engineer at Hager Group. “By installing a Fortus 380mc 3D printer in-house, we now have an advanced system that provides dependable results throughout the tooling process.”
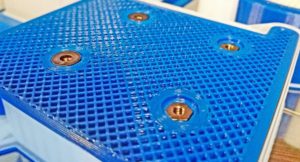
In the past, when a part had to be replaced or produced on the production floor, the team was not able to be reactive due to the long outsourcing process that had to take place. This was a problem for the company as it caused a stop in production, delayed productivity and increased costs.
“We needed a method that could create complex, functional and lightweight parts efficiently — this is where FDM-based 3D printing fits perfectly, which is why we have integrated it across all of our operations here in Saverne,” explains Callegher. “The 3D-printed parts have led to a significant cost reduction compared to machining the part out of aluminum, as well as a 50 percent reduction in overall weight. We estimate that we have seen a ROI within 18 months.”
“By installing a Fortus 380mc 3D Printer in-house, we now have an advanced system that provides dependable results throughout the tooling process.”
– Alexandre Callegher Mechanical Engineer, R&D Department, Hager Group
3D Printed Tooling – Made Faster and Lighter
In the past tools would have been manufactured in aluminium- this process was very costly and timely and also left the team with tight design constraints and little flexibility.
Introducing an in house production oriented and high-performance solution, allows the company’s team to design parts efficiently, timely and cost-effectively. 3D printing gets rid of the drawing stages and mechanical restraints found in traditional manufacturing and thereby saves the team up to three days of lead time.
“We now regularly produce customized, low volume tools within 24 hours of an engineer’s request — a fraction of the cost and weight of an aluminum tool. In comparison, when outsourcing traditionally manufactured tools, the process took two weeks,” says Callegher.
Another benefit found with 3D printing with FDM Technology™ is a decrease in tool weight. FDM additive manufacturing grants the team with the ability to 3D print lightweight tools by using the honeycomb structure – this is now doable faster and more cost-effectively than ever before when using traditional manufacturing methods.
The Hager Group is so happy with the abilities of additive manufacturing that when they were asked to replace the rotating support for an antenna that is used for testing Bluetooth frequency- they used 3D printing.
Looking to Learn More About Tooling?
Download our guide to learn about the business drivers for adopting 3D printing for production tooling instead o traditionally fabricated tools.
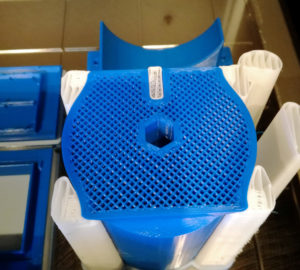
Expanding Beyond the Production of 3D Printed Tooling
After seeing all the benefits of using the Stratasys 3D printing technology, the Hager Group is looking for other opportunities beyond the production of 3D printed tooling to utilize the technology.
According to Callegher, “FDM technology has altered the way we work to the extent that we are planning on commercializing small series products incorporating 3D-printed parts. Over the next couple of years, we intend to print 120 thumb-sized caps with an electronic device integrated with resin to hold in place. Before our investment, we did not foresee the commercial benefits. Stratasys 3D printing has opened our eyes to the ways in which we can fully develop what we do here in Saverne.”