Gaining Efficiency and Reaching New Heights
GKN Aerospace is a well-known multi-technology tier-one aerospace supplier and distributes to over 90% of the worlds engine and aircraft manufacturers. Over the last 30 years, GKN Aerospace has also gained prominence as a leader in the use of 3D printing, also known as additive manufacturing, for military, space, and commercial markets. GKN’s Filton manufacturing site is where they produce and supply prototypes and production tools to a multitude of areas of their business. The company was tasked with reducing costs when it came to production line downtime, while at the same time delivering prototypes are both fully functional and ultra-realistic. Rachel Trimble, GKN’s additive manufacturing polymer specialist looked to additive manufacturing, and using 3D printed tools as a solution to GKN’s challenges – she believed the 3D technology could meet both the company’s goals and also prepare them for the future.
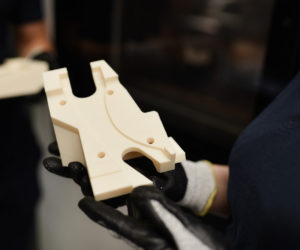
Using 3D Printed Tools to Reduce Costly Production Downtime
Any stop in production is an expensive interruption for GKN. For instance, in the case when a traditionally manufactured part breaks, merely replacing it ends up taking a lengthy period of time and comes at a high price. Typically an engineer would have to wait weeks for a new part, and this halt in production is something that the company cannot afford. Trimble explains that the use of 3D printing will remove this challenge and will thereby better the receptivity to the engineer’s manufacturing needs and work requirements. In a particular situation, GKN engineers had used additive manufacturing to print small tools to make protective masks that were to be utilized when producing metal parts. Since the masks were not available commercially, there was a backlog of parts needed. Luckily, the team had the ability build 3D printed tools that were used to make the masks in both an effective and efficient manner – this process greatly alleviated the challenges the team was having and helped to reduce the backlog.
Looking to Learn More About Tooling?
Download our guide to learn about the business drivers for adopting 3D printing for production tooling instead o traditionally fabricated tools.
Revolutionized, Optimized, Customized
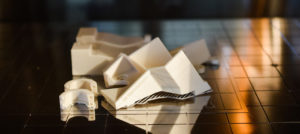
GKN definitely appreciates both the cost and time savings that additive manufacturing provides, however, the benefits don’t end there. Trimble has stated that one of the greatest benefits of additive manufacturing is the creative freedom it provides its users with. In the past when using traditional manufacturing, GKN engineers were limited by the physical and economical restraints- today, the GKN team can build 3D printed tools that were once unthinkable to produce.
Freedom in the work environment, as well as the processing freedom for the production line operators, are yet other great benefits of using additive manufacturing. Timble states that the additive manufacturing technology allows for the creation of accurate, advanced 3D printed tools that are not restricted by shape or size-this allows the tools to be tailored to specialized jobs and thereby improved the performance of their operations. In specific situations, the engineers at GKN have noted a great reduction of 40% in concessions and certain jobs even were able to reduce from two operates to one.
In order to accomplish its goals, GKN relies greatly on the Fortus 900mc™ 3D Printer.
“The Fortus 900mc offers the largest build size of any FDM® 3D printer, enabling us to quickly produce tools to meet any requirements. We’re already utilizing this technology to design and 3D print previously inconceivable tools, which then enable us to manufacture extremely complex parts that would be uneconomical or just physically impossible by any other means,” said Trimble.
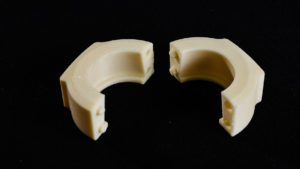
Fully-functioning and Realistic Prototypes
Other than tooling, GKN often uses its Fortus 900mc for rapid prototyping. A great example of this is when the GKN team used additive manufacturing to create a fully functional aircraft windscreen housing.
“In a matter of hours, we were able to produce a prototype of this windscreen housing on the Fortus 900mc,” said Trimble. “The prototype produced was so realistic and so accurate that the launch team was not only able to go ahead with the event but the feedback received confirmed that the 3D printed housing was almost indistinguishable from the real thing.”
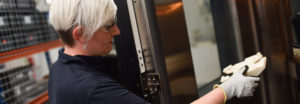
Looking Forward
Timble foresees a great shift towards the use of FDM additive manufacturing for flight-critical, high value, end-use composite parts.
“By harnessing Stratasys additive manufacturing for tooling and prototyping, we are enjoying both time and cost savings, among other benefits, all while simultaneously preparing ourselves for the future,” said Trimble.
Want to Learn more about Production-Grade 3D Printed Tooling? We think you’ll love our article The Business of Additive Manufacturing: Why Using 3D Printing for Manufacturing Tooling Just Makes Sense