A Business Built On Customization
Customization is the name of the game for Utah Trikes, a producer of trikes, quads, and custom wheelchairs. The company is located in Payson, Utah. Ashley Guy, President and CEO of Utah Trikes, has firmly believed in personalization from the beginning. “We started making our quad using existing frame platforms and built custom two-wheel drive rear ends that we’d add on and effectively turn the trikes into quads. That grew into something where suddenly everybody who wanted something customized came to us.”
“I no longer have to constrain my designs because of prototyping limitations. Now I can focus on designing better, more functional parts.” – Ashley Guy, Utah Trikes.
Customers Require Drive Innovation
Customization comes with challenges, mainly time, and cost. “The production run might only be 100 parts and it’s hard to get your cost down with such a small run,” said Guy. Utah Trikes’ following step was to try to solve its manufacturing issues. “We have some CNC machines we ran pretty much nonstop,” Guy said. “But this was always a hassle without committing to jigs and fixtures, which meant a lot of man hours to prototype.” Parts could potentially become more complicated. It became more difficult for Utah Trikes to outsource.
Utah Trikes required ability to make prototype pieces they could legitimately test, which would ultimately be more time and cost efficient. This is when 3D printing become prominent to Guy. “I was intrigued but had no idea what I was looking for. But it didn’t take long for Guy and his team to see what 3D printing could do for them.”
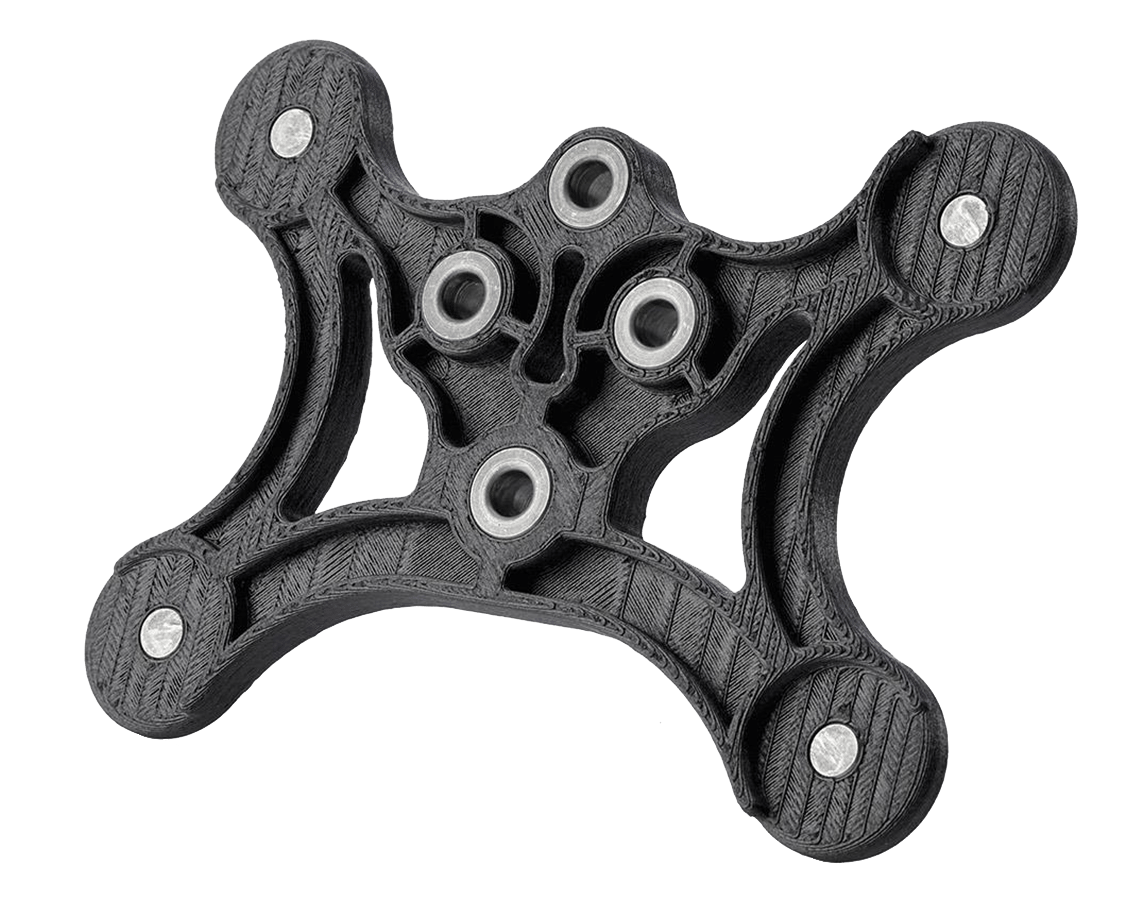
A Whole New Way To Design
Additive manufacturing begins the design process is no longer impeded by machining restrictions. “I no longer have to constrain my designs because of prototyping limitations. Now I can focus on designing better, more functional parts, without worrying about how to shape the aluminum or how to lay up carbon fiber onto the molds,” said Guy.
The ability to rapidly switch from design to in-use part means designers at Utah Trikes now have the ability to spend more time on perfecting designs. Guy has ensured the entire team at Utah Trikes has accessibility to CAD software. This is so they can easily design to fit their designs. “Even the machinists can design to fit their needs, then simply print it out,” Guy said. “It’s taken me a while to wrap my brain around the idea that we can now design for functionality rather than machining.”
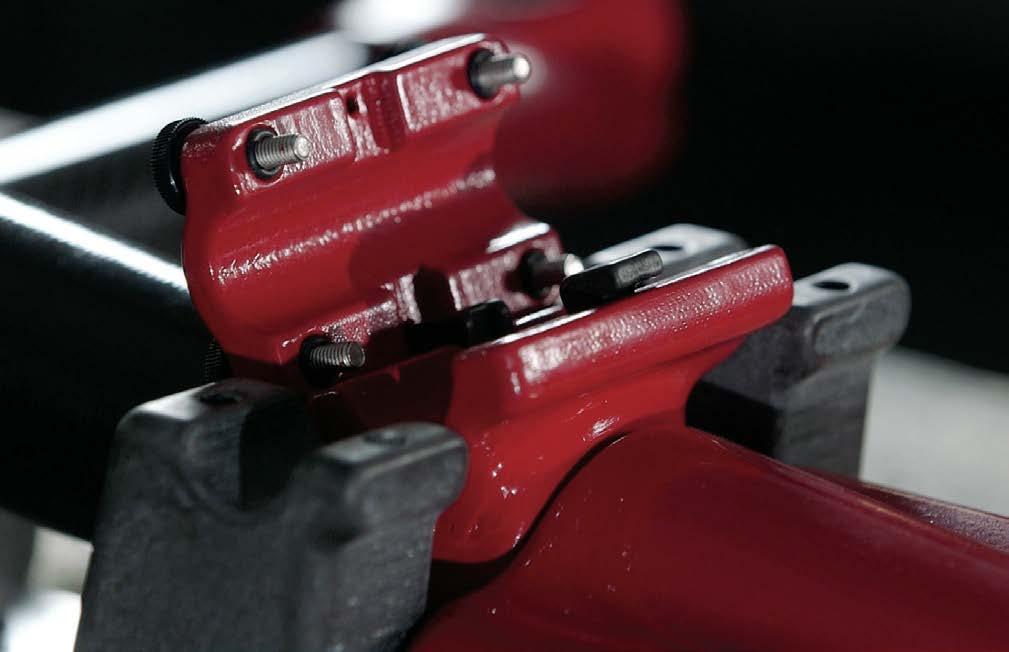
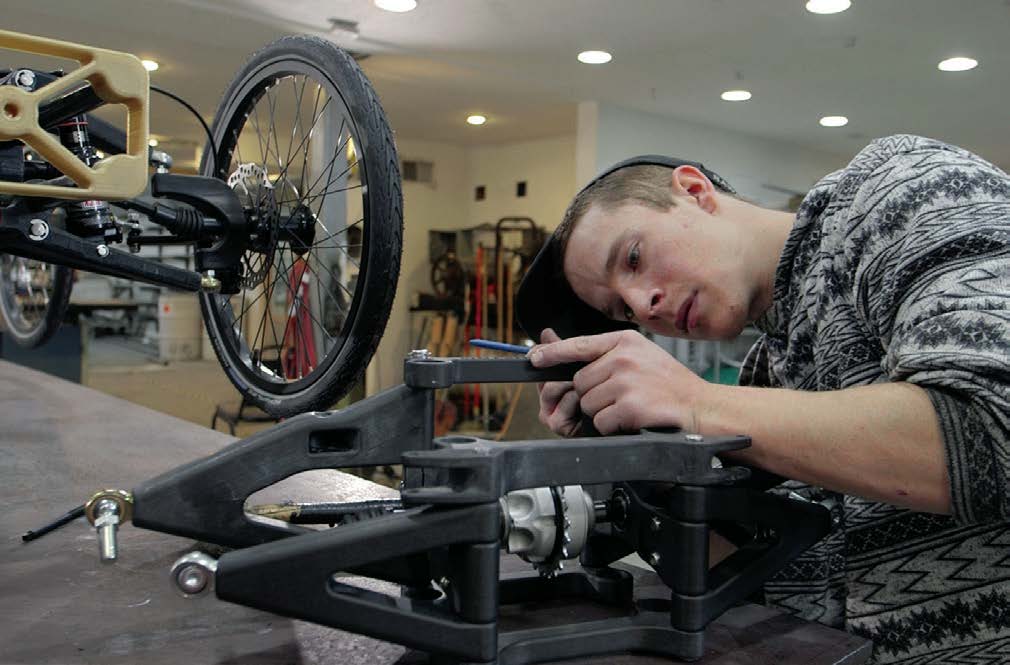
Carbon-Fiber Nylon – A Game Changer
There was still an issue of being able to test new designs. Guy held an investigation which led him to Stratasys’ Fortus 3D printers. “We started out using Nylon 12 material and it got us about 75% of the way there,” Guy said. “We made a quad prototype using parts printed with other materials that were either too brittle or too flexible.” It was not until Guy attempted to use FDM Nylon 12 Carbon Fiber when he realized he had found a tool that would change his business.
“The FDM Nylon 12CF is fantastic. It’s changing everything for us,” Guy said. He cites the strength of the material, as well as its soluble support as game changers. Additionally, “We can take the part and put it into our tumbler overnight and it comes out with a smooth, polished finish,” said Guy.
The new Carbon-fiber version of FDM Nylon 12 was perfect, according to Guy. “Let’s face it, when it came down to bolting a part on a trike and heading down a hill on it, it was only the Stratasys FDM Nylon 12CF that held up.” A pedal-powered wheelchair in production at Utah Trikes has 450 distinct parts, 120 of those parts are 3D printed. It’s also a game-changer for the custom manufacturer is their ability to both design and print on site. It has cut production time from two months to two weeks! This reduces costs 8-10 times.
“Stratasys FDM Nylon 12CF parts can be printed faster, with superior stiffness- to-weight performance and with better repeatability than any other 3D printing technology we’ve seen.” Guy cites the superior mechanical properties of FDM Nylon 12CF Carbon Fiber and its ability to be used in all stages of the manufacturing process, from rapid prototyping to jigs and fixtures to final production parts for short-runs and custom orders. “With FDM Nylon 12CF, we’re able to make parts we wouldn’t otherwise be able to make.”