Two-fold Opportunity.
Customized production at scale.
We partner with notorious Additive Manufacturing players to ensure your parts are meticulously produced with every print job.
Improved patient outcomes with 3D-printed wearable orthotics & prosthetics.
At Proto3000, we can produce medical and prosthetic devices with fairly complex geometries that are more effective, lighter and more cosmetic. Whether you need a completely unique prosthetic or require short or mid-production runs, we can help you!
Better for Everyone
Why produce insoles, orthotics and prosthetics with 3D printing?
Manufacturers
Reduce manual labour ♦ Consistent repeatability ♦ Higher accuracy ♦ Ease to scale.
Clinicians
Faster patient turnaround ♦ No need for plaster molds ♦ No molds shipping ♦ Less fitting adjustments.
Patients
Better fit, less bulky ♦ Lightweight & breathable devices ♦ Comfortable for daily usage
An End-to-End Solution
From production to post-processing, we have you covered!
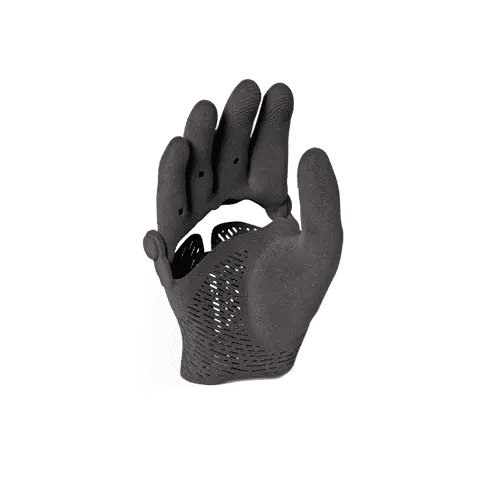
RAW
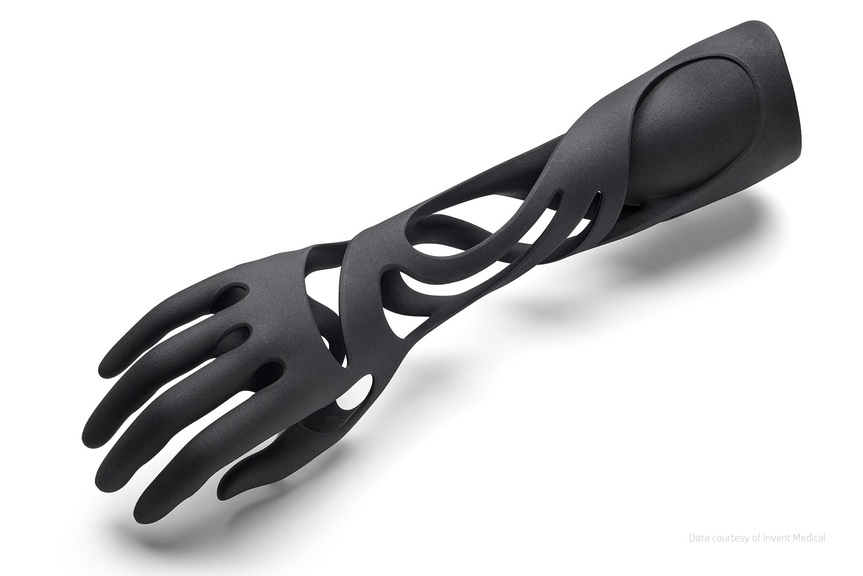
DYE
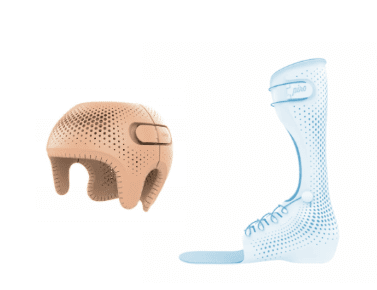
PAINT & OTHERS
How the process works.
Connect & Consult
Our team of experts works with clinicians and medical experts to design & develop the best orthotics and prosthetics.
Design & Development
We then use the provided inputs and powerful industry-leading software tools & materials to help you produce innovative assistive devices.
No more conventional orthopedics!
3D Print | Manufacture
We recommend options from a range of different additive manufacturing processes and materials that meet your application requirements and performance objectives.
Inspect & Ship
Thanks to our technological capabilities, we can print out directly the final products. Our production team rigorously checks each part for conformity and accuracy.
Applications
- Wearables and soft-touch elements
- Gaskets, seals, masks, belts, plugs, and tubes
- Protective sports equipment
- Padding, dampers, cushions, and grippers
- Soles, splints, orthotics, and prosthetics
- Insoles
- Knee braces
- Wrist & Back supports
- Collars
Materials
Based on each project, our Service Bureau can recommend the best materials on the market that withstand the required properties and functionalities. See below a list of some of the most commonly used powders in the Prosthetics and Orthotics industry.
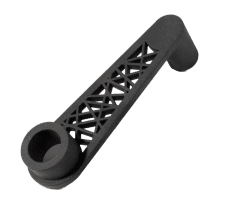
Formlabs® Nylon 11
Material: Ductile, high-impact
Nylon 11 Powder is a high performance, bio-based nylon material for functional prototyping and small batch production.
Specs
- Ultimate Tensile Strength: 49 MPa
- Tensile Modulus: 1.6 GPa
- Elongation at Break (X/Y): 40%
- Flexural Strength: 55 MPa
- Notched Izod: 71 J/m
- Heat Deflection Temperature (HDT) @ 1.8 MPa: 46ºC
Application
- For parts that need to bend or resist impact
- Impact-resistant prototypes, jigs, and fixtures
- Thin-walled ducts and enclosures
- Snaps, clips, and hinges
- Orthotics and prosthetics*
Technology/Process
- SLS (Selective Laser Sintering)
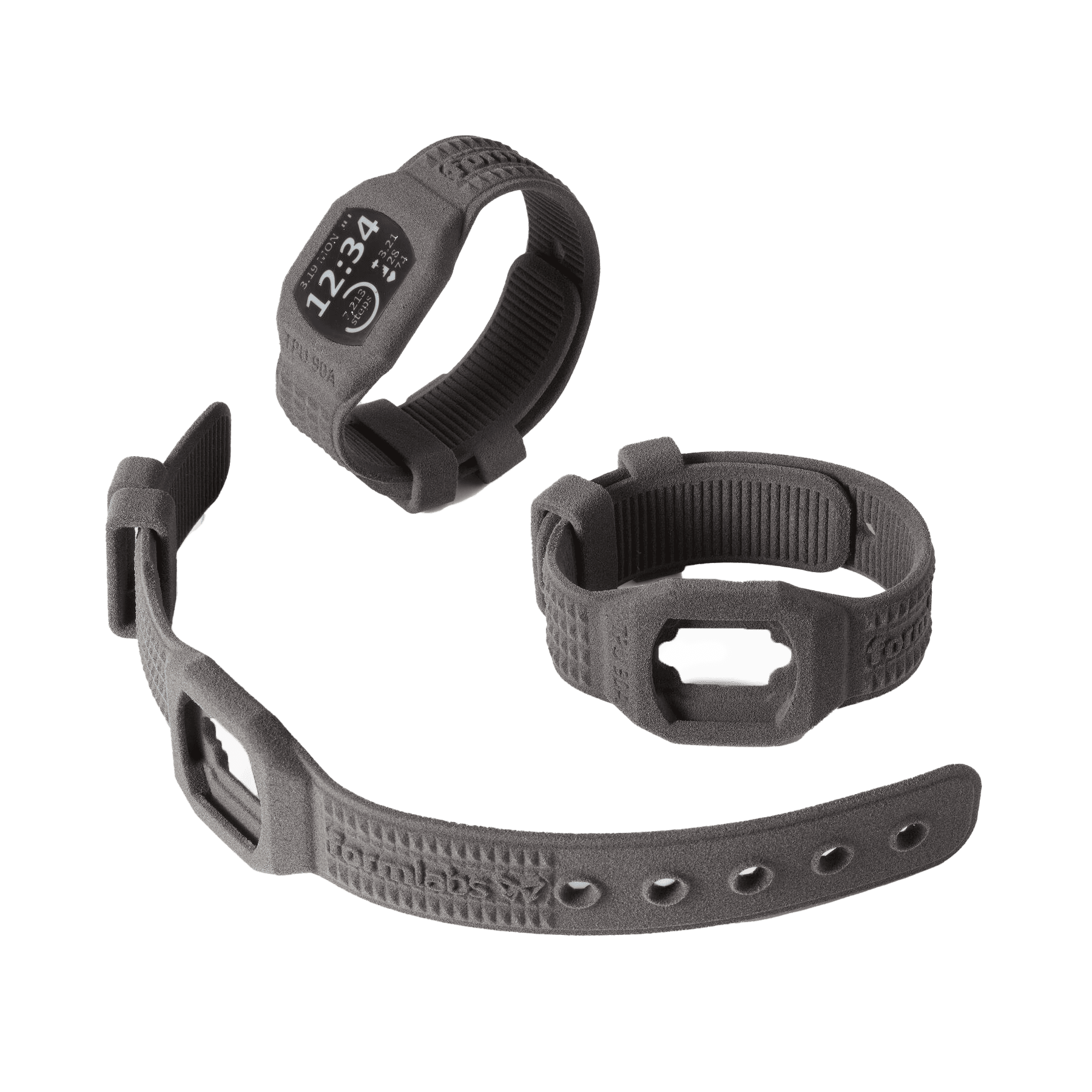
Formlabs® TPU 90A
Material: Tough SLS Elastomer
TPU 90A Powder provides the perfect balance of flexibility and strength, allowing you to create durable prototypes and end-use parts that are both safe for the skin and withstand daily use.
Specs
Material Properties*:
- Ultimate Tensile Strength: X/Y: 8.7 MPa; Z-axis: 7.2 MPa
- Tear Resistance: X/Y: 66 kN/m; Z-axis: 39 kN/m
- Elongation at Break: X/Y: 310%; Z-axis: 110%
- Shore Hardness: 90A
Certifications/Tests:
- Samples printed with TPU 90A powder have been evaluated in accordance with ISO 10993-1:2018, and have passed the requirements for the following biocompatibility risks:
- ISO 10993-5: 2009 Non-cytotoxic
- ISO 10993-23:2021 Non-irritant
- ISO 10993-10:2021 Non-sensitizer
*Material properties may vary with part geometry, print orientation and temperature.
Application
- Wearables and soft-touch elements
- Gaskets, seals, masks, belts, plugs, and tubes
- Protective sports equipment
- Padding, dampers, cushions, and grippers
Technology/Process
- SLS (Selective Laser Sintering)
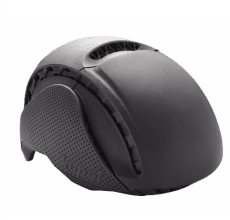
Nylon 11 (HP High Reusability PA 11)
Material: Polyamide 11 (Nylon PA 11)
Thermoplastic polymer, known for its toughness, chemical and high-temperature resistance. It is commonly used to produce functional prototypes, end-use parts, and tooling.
Specs
- Tensile Strength:
- 50 MPa/7250 psi (XY axis)
- 50 MPa/7250 psi (Z axis)
- Powder Melting Point (DSC): 202° C / 396° F, ASTM D3418
- Particle size: 54 microns, ASTM D3451
- Bulk density of powder: 0.48 g/cm³, 0.017 lb/in³
- Density of parts: 1.04 g/cm3, ASTM D792
- Biocompatibility – meets USP Class I-VI and US FDA guidance for Intact Skin Surface Devices
Application
- Healthcare
- Prostheses, Insoles
- Consumer Goods
- Sport goods
- Snap fits
- Living hinges
- Industrial
- Education
Technology/Process
HP Multi Jet Fusion (Powder Bed Fusion)
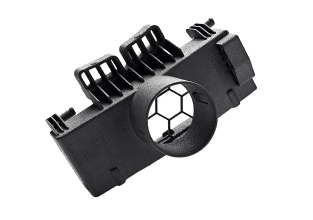
Nylon 12 (HP High Reusability PA 12)
Material: Polyamide 12 (Nylon PA 12)
HP 3D High Reusability PA 12 is a robust thermoplastic that produces high-density parts with balanced property profiles and strong structures.
Specs
- Powder Melting Point (DSC): 187° C or 369° F, ASTM D3418
- Particle Size: 60µm
- Bulk Density of Powder: 0.425 g/cm3 0.015 lb/in, ASTM D1895
- Tensile Strength: 30 MPa
- Elongation at Break: 20%
- Young’s Modulus: 1600 MPa
- Charpy Impact Notched Test: 35kJ/m²
Application
- Consumer goods and electronics
- Low-high volume production
- Rapid prototyping
- Manufacturing aids
- Tooling, end-of-arm tooling, robotics
- Medical
- Porthotics, prosthetics
Technology/Process
HP Multi Jet Fusion (Powder Bed Fusion)