“Each year our use of additive manufacturing has increased, most notably tooling for composites and flight parts.”
– Dan Campbell, Program Manager and Group Lead for additive manufacturing research, Aurora Flight Sciences
Aurora Flight Sciences is proving to be a leader of the development and manufacturing of advanced unmanned aerospace vehicles and systems. With four US-based locations and 500 employees, Aurora is not your ordinary aerospace company. As a matter of fact, their comparatively small size allows them to take the lead in adapting the evolving requirements of the aerospace defence industry. Aurora has created a record-breaking, ultra-long endurance unmanned aircraft (Orion); an optionally-piloted aircraft (Centaur); a number of small man-portable unmanned aircraft systems (UAS); and large solar aircraft. They were also recently awarded the DARPA X-plane contract with their exclusive and innovative LightningStrike VTOL concept. Aurora’s Aerostructures business sector provides complex and massive composite assemblies and structures to a wide range of OEMs including Sikorsky (CH-53K, MG-60R, S-92, S-97), Northrop Grumman (Global Hawk & Triton UAS), Gulfstream (G5000), and Bell (525)
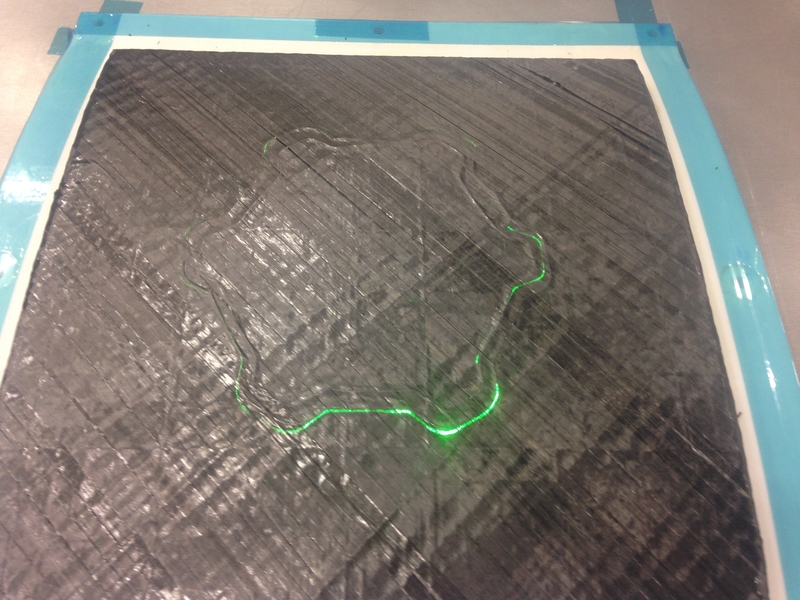
Aurora Flight Science is continually creating and innovating because of its use of additive manufacturing in almost every aspect of the business. It’s known that the aerospace industry has been using a variety of 3D printing technologies like FDM for years, however, they have been among the additive manufacturing leaders for far longer with mainstream prototyping applications such as production parts, composite tooling and even the very first jet-powered UAV demonstrator. The advantages of additive manufacturing were instantly clear to Aurora as they had the ability to incredibly reduce their development and design cycle, lead time, and save in the overall cost. AM has proven to be very advantageous as some parts can be printed in as little as days or even hours and with great cost reductions compared to olde, traditional manufacturing methods.
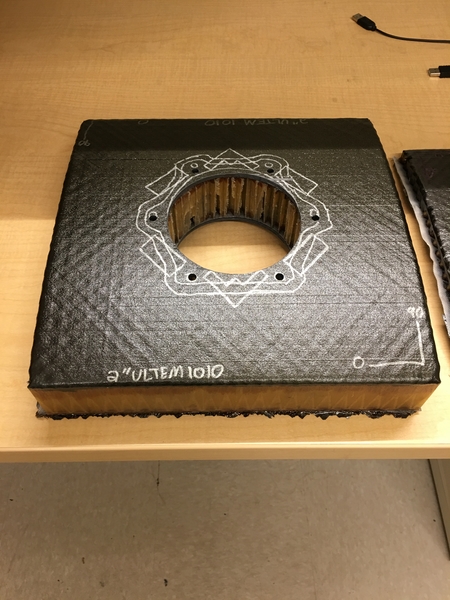
In addition to production parts and composite tooling, Aurora Flight Sciences is using FDM in research and development programs to produce multi-functional composite structures. Dr. Konstantine Fetfatsidis, Director of Advanced Composites Pursuits/Programs at Aurora, is developing a NASA program that brings together FDM with automated fiber placement (AFP).This technology approach encourages the self-healing of micro-cracks to assist in prolonging the life of big composite vessels which will eventually carry mankind into deep space. Small continuous thermoplastic (PLA) sacrificial filaments (300-400 micron diameter) are printed directly between piles of carbon fiber composite materials laid down by the AFP system. When the resin in the composite has gelled, a post-cure cycle at a moderately increased temperature allows the PLA (that is coated with a catalyst) to be de-polymerize, leaving empty hollow channels embedded in the composite. These channels are then filled with a two-part chemistry so that when a micro-crack penetrates the channels, the fluids will spill into the crack, combine together, and start to cure.
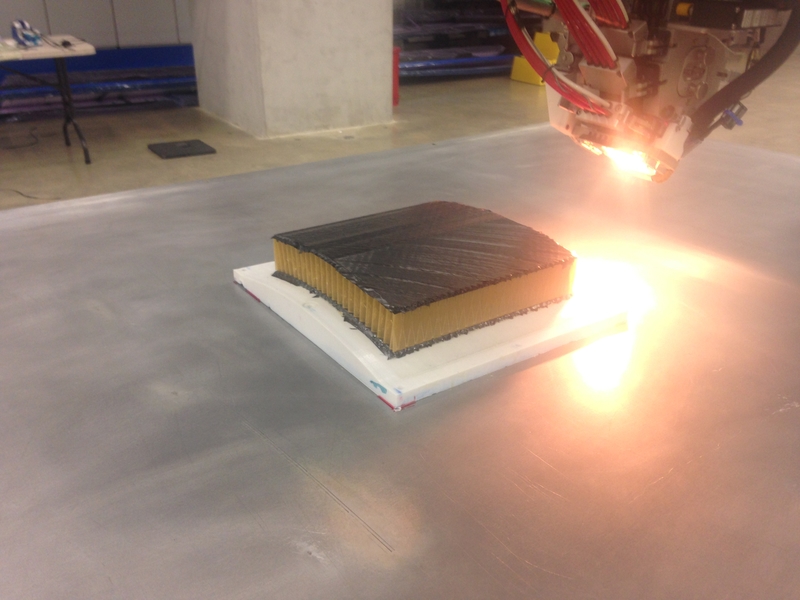
The decision of where to store the healing agent pushed Aurora to evaluate how 3D printed honeycomb cores that could be customized in shape and size for structural performance while also performing as a reservoir for storing fluids needed for thermal management and self-healing applications. Conclusively, Aurora has used its AFP system to lay-up sandwich composites, employing 3D printed cores and embedded 3D printed features, onto low-cost FDM composite tooling that has commonly been used for drill operations and trims. Within the following months, Aurora will be working up the evaluation to illustrate the manufacture of a five-foot diameter dome section that has a core and lay-up mold 3D printed with ULTEM 1010 resin by Stratasys.
Aurora Flight Sciences is a perfect example of a company that makes strategic decisions to take advantage of additive manufacturing (especially FDM) in their daily operations, and by doing this has realized a great number of benefits. Aurora has also positioned themselves to act as a leader in technology as they continue to focus their energy on creative research and development projects that have proven to push the boundaries of technology and the ways in which we traditionally think. Additive manufacturing continues to enable the progress of innovation and design and will continue to propel technology advancements across automotive, aerospace and other demanding manufacturing industries-so let us get ready for takeoff!
![]()
What to Learn More about Tooling with Additive Manufacturing?
Download our guide to discover the business considerations for using additive tooling in production