It’s generally understood that 3D printing has rewritten traditional manufacturing processes. But what isn’t as well known is how additive manufacturing frees design possibilities from the bounds of having to fit into traditional manufacturing restraints.
The difference is so profound, it has fostered new design terminology, including design for additive manufacturing (DfAM).
One of the possibilities opened up by DfAM is the ease, speed and relatively low cost of including intricate features into the part and product design.
The time and cost of refining designs to suit traditional processes, including prototyping and the limitations of machining fine features, often made creating and manufacturing them cost-prohibitive, if not entirely impossible.
But 3D printing gives engineers and designers the freedom to create very fine, detailed features, during prototyping and production runs, without tooling and machining.
DfAM – Intricate Elements Use Cases
End Effector for O-Rings
Used to install O-rings onto hydraulic fittings, the end effector was only needed in small quantities. The extensive and costly CNC machining needed for tiny, complex parts like the effector would have added significantly to the per-unit cost of manufacturing the part.
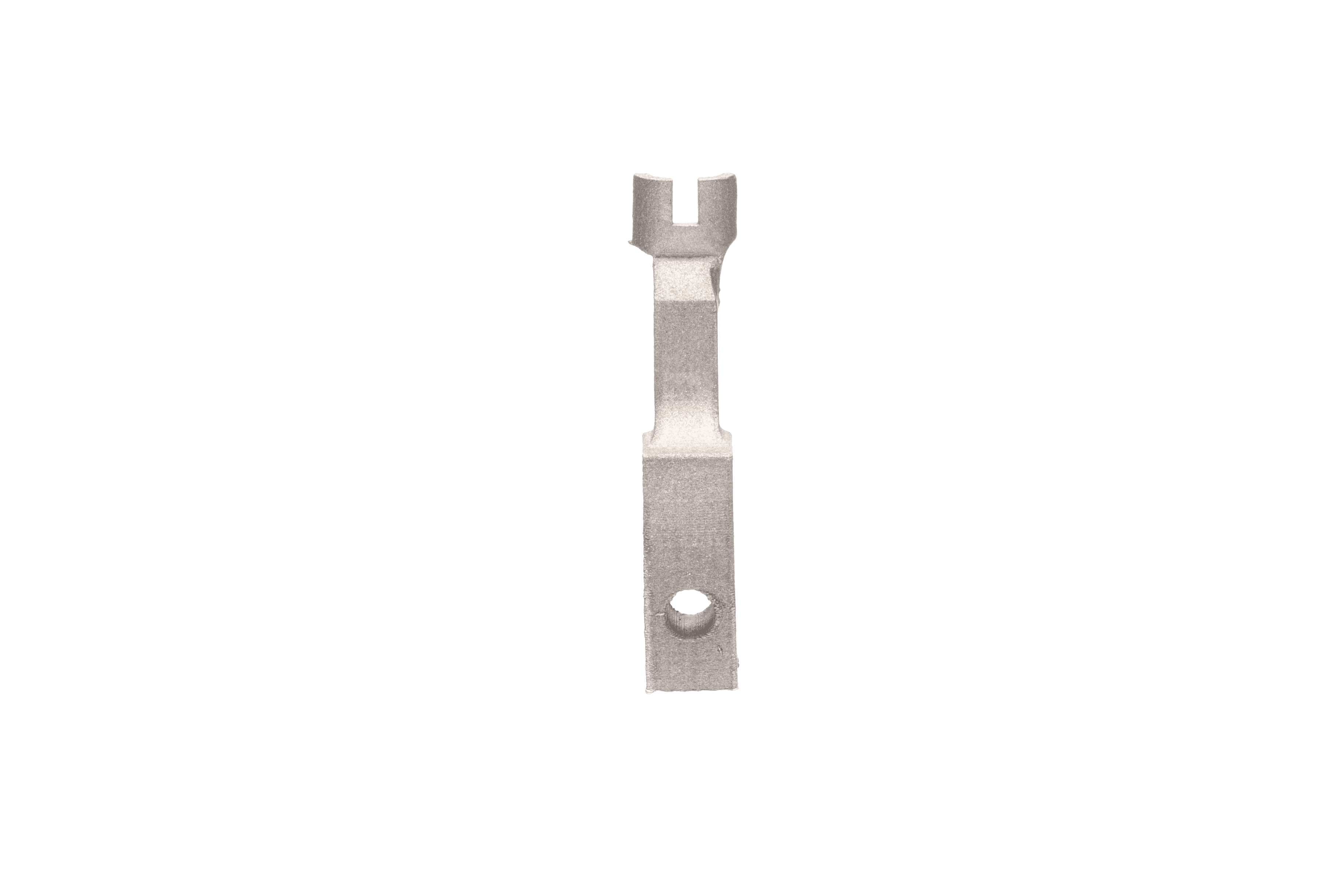
Instead, the Desktop Metal Studio System’s high-resolution printhead for 3D printing with metal slashed development and production times to make the part more cost-effective.
Hinges for Eyeglasses
3D printing made it faster and less expensive to design and build the fine detail, durability and functionality specified for the eyeglass hinge. Perhaps more remarkably, additive manufacturing allowed for printed-in-place assembly to completely eliminate the traditional part assembly process.
Hair Trimmer Blade
Made for electric hair trimmers, this blade would usually require costly stamping or injection molding to produce. The fine teeth must be precise and durable, which would require exact tooling, which would add to lead times and costs.
In addition to eliminating tooling costs and cutting manufacturing times, 3D printing allowed for mass customizations that would have been unthinkable using traditional processes.
To learn more about DfAM, check out our article “Design for Additive Manufacturing Generative Design Use Cases”.