Overview
Lumenium – A Virginia-based company is developing a new family of internal combustion engines. The Inverse Displacement Asymmetrical Rotational (IDAR) engine is a novel, and complete singular design for constructing powerful, efficient, internal combustion. It’s one of a kind geometry allows dramatic, yet efficient work output from a small, light weighing engine which consumes less fuel and produces lower emissions.
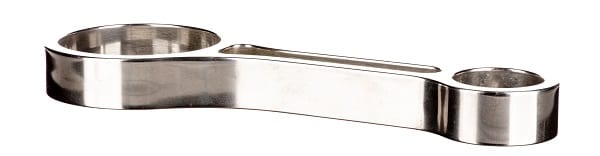
The Challenge
For the company, the ability to iterate rapidly has an uninterrupted impact on time-to-market and engine performance. As of right now, Lumenium uses an in-house CNC machine and wire electrical discharge machining (EDM). This is done to produce prototype parts, however, the process is pretty time consuming as well as costly. The company is seeking a quicker, cost-effective approach to prototyping parts within the engine assembly.
Parts within the IDAR engine are required to withstand the extreme heat and stress inherent to internal combustion engine operation. Every component must adhere to different and specific requirements. This includes high dimensional accuracy, strength beneath dynamic loads, and low thermal expansion. The weight of every part is crucial to consider for overall power density and efficiency. Lumenium is able to meet these requirements and tackle complex part geometries; such as internal cooling channels to improve engine performance, because of additive manufacturing. Using the Desktop Metal Studio System, Lumenium has the ability to bring this technology into their existing workspace for quicker design iteration, as well as functional prototyping.
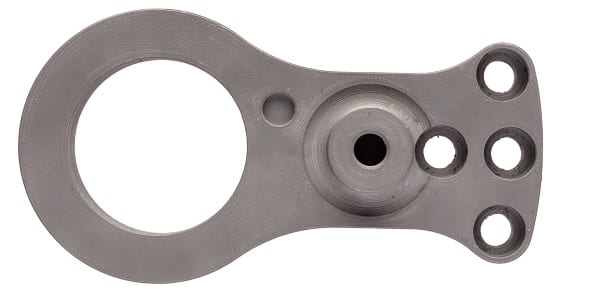
The Application
Internal combustion engines make up the $350 billion market with three categories of engines:
- Traditional piston engine
- Novel opposed piston engines
- Rotary engines
Lumenium’s IDAR engine technology adds a fourth category which showcases a paradigm shift in the power of production. The engines operate beneath a large amount of heat and stress, therefore engine components require being able to withstand dynamic loading conditions, combustion forces of 1500 psi, and combustion temperatures of 1500°C.
Designing a complex product that includes extremely high-performance necessities has led to many generations of engine designs, all with a long conceptual phase of designing, prototyping, and iterating. The ability to perform multiple design iteration has a compelling beneficial impact on the engine’s final performance. Full engine development cycle for each generation of the IDAR engine can take between three to five years. Recognizing a quicker, cost effective approach to prototyping is crucial to IDAR engine development. The ability to also lightweight parts while adhering to other mechanical property needs directly impacts engine performance.
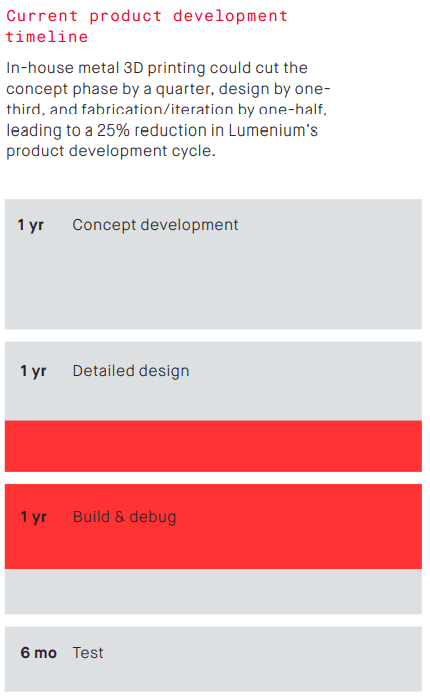
Printing VS. Machining
Lumenium makes about 20 prototype parts every month. Nearly 95% are manufactured in-housing, using five-axis CNC machining; as well as wire EDM. Machining complex geometries using CNC comes with many complex tool paths and sometimes, an additional 80 different machining operations. Every operation calls for re-programming. Re-programming often includes custom fixturing and an operator to realign the part. The amount of overall machining operations is notably less, even if post machining is necessary. Programming the CNC machine demands a trained and dedicated operator, which could potentially take weeks for a single, more complex job – from designing to creating the CNC tool path, to fixturing to machining. Certain parts require post-processing by outside vendors which can add three weeks to the fabrication.
The remaining 5% of the prototype parts, which are traditionally conventional, round parts, are sent to an outside machine shop where lead times average about three weeks. Extensive lead time restricts Lumenium’s ability to iterate on the design, therefore, having an immediate influence on engine performance.
Additionally, to extending lead time and high costs, machining offers only limited options using light-weighting parts. Weight is very important to engine performance where a 50% reduction in engine weight could possibly double the rated engine speed (RPM) and power output. In order to eliminate weight using machining methods, engineers can do little beyond selecting a lightweight material. Without changing the material, reducing weight via machining can usually require altering the part geometry, which will inevitably add time and complexity; thus resulting in weak points within the part structure. Early versions of the engine used parts machined from solid blocks of aluminum, a lightweight alloy. Although, aluminum grows as temperature maximizes, which is an unfavourable property for engine components that operate at high temperatures. Steel as a common of thermal expansion that is about 68% less than aluminum.
The Studio System prints parts with closed-cell infill. This is an internal lattice structure printed throughout the part. Users can adapt infill spacing in order to meet strength and weight requirements. Parts printed using infill will have an unquestionable lower thermal transfer. Thus, eliminating part weight while maintaining strength, which allows Lumenium to pursue steel as part of their solution.
Part Comparison
Lumenium submitted three parts for introductory benchmarking. These parts piece together in a sub-assembly of the IDAR engine and some modifications were made in order to adapt the design for 3D printing with the Studio System. For each of the three parts, the Studio System was proven to be a quicker and less costly solution than the machined alternative. In order to showcase the fabrication process and benefits, let’s examine the saddle carrier.
Lumenium Printed PartsA. Saddle carrier Part Requirements
|
![]() |
COST SAVINGS |
TIME SAVINGS |
WEIGHT PRODUCTION |
74% |
43% |
39% |
STUDIO SYSTEM FABRICATION | |
Technology | Bound Metal Deposition™ |
Material Type | AISI 4140 steel |
Infill Spacing | 2.8 mm |
Part Mass | 933 g |
Fabrication Time | 4 days |
Cost-Per-Part | $148 |
PREVIOUS MANUFACTURING METHOD | |
Technology | CNC Machining from solid metal block |
Material Type | 4340 steel |
Part Mass | 1518 g |
Lead Time | 7 days |
Cost-per-part | $980 |
Design Guidelines
Self-supporting Angles: “The Teardrop”
In most cases of extrusion based 3D printing methods, including Bound Metal Deposition, horizontal holes need internal support structures in order to retain the shape. Although adapting the shape of the hole can dispose the requirement for supports. Lumenium altered the design, changing the round holes to a more angular shape (example being a teardrop) which don’t ask for support structures during fabrication.
Adjustable Shell Thickness
The Lumenium saddle design includes serrations along the top and bottom edges, which mate with the swing arms. The serrations assist in the component withstand engine forces and machining these crucial features which allow for a smooth and authentic mating surface that can’t be achieved by printing by itself. When using Fabricate, users can adjust shell thickness selectively. it’s important to keep in mind that this doesn’t change the dimension of the part. Alternatively, it thickens the solid shell around the part to avert exposing the part’s infill during machining. Lumenium boosts the shell thickness of only the top and bottom facing features to 5.2 mm. This is to account for material which would be removed during machining of serrations.
The Role of Infill
The weight of an internal combustion engine is crucial to its ability to perform. Using Studio System, the company can leverage features such as the closed-cell infill to lightweight parts with an internal lattice structure. This is because they can use strong metals, such as stainless steel or titanium, which has the ability to adhere to additional part necessities.
- Machined steel part: 1500 g
- Printed steel part (with infill): 933 g
- Machined aluminum part: 522 g
Post-Processing
After being fabricated, Lumenium performed crucial post-processing steps on the printed parts, including CNC machining and wire EDM. Compared to a strictly machined part, the amount of post-processing steps is less and almost relatively easier to perform due to less fixturing and programming necessary. The company machined the saddle’s important surfaces, adding serrations to the top and bottom, and drilled, as well as threaded, holes. After its completed, Lumenium bolted together the saddle and swing arm.
Summary
For Lumenium, rapid prototyping is crucial for product development and maturation as the IDAR engine approaches commercialization. Both the design and function of each part within the assembly is significant, therefore the ability to clarify and iterate rapidly has a direct impact on the overall engine performance. Earlier methods of machining individual prototype parts; whether it’s in-house or by an outside machine shop, are time-consuming and expensive. The time and cost savings the system delivers are demonstrated by the printed saddle, swing arm, and connecting rod.
When users consider the time associated with programming CNC machines, labour costs, and design limitations, the Studio System would eliminate Lumenium’s design iteration in half. Three to five years of full development cycle can save a significant amount of time on the impact of the product development cycle, as well as the revenue model.
Discover what in-house high resolution metal 3D printing can do.
Explore the Desktop Metal Studio System
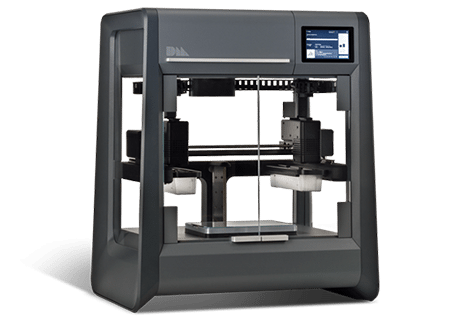