Additive manufacturing has promised a revolution in manufacturing, however much of the focus has been solely on low volume production, and is used mostly for plastic parts.
Benefits of 3D printing come with the ability to produce parts with complex geometries that have been found to be difficult – and at times, impossible to achieve otherwise and at a lower cost than traditional manufacturing methods.
Plastic 3D printed parts have many use of cases, but applications demanding specific part properties. These part properties require metal such as, stiffness, strength, corrosion resistance, machinability, or others. With metal 3D printing’s accessibility, designers, as well as manufacturers, have the ability to produce complex parts rapidly using a broad range of materials.
The Studio System leverages the most commonly used plastic 3D printing process, which is FFF. This is to produce high quality metal parts. Important applications include the following:
Functional prototyping
Jigs and fixtures
Tooling
Low volume production
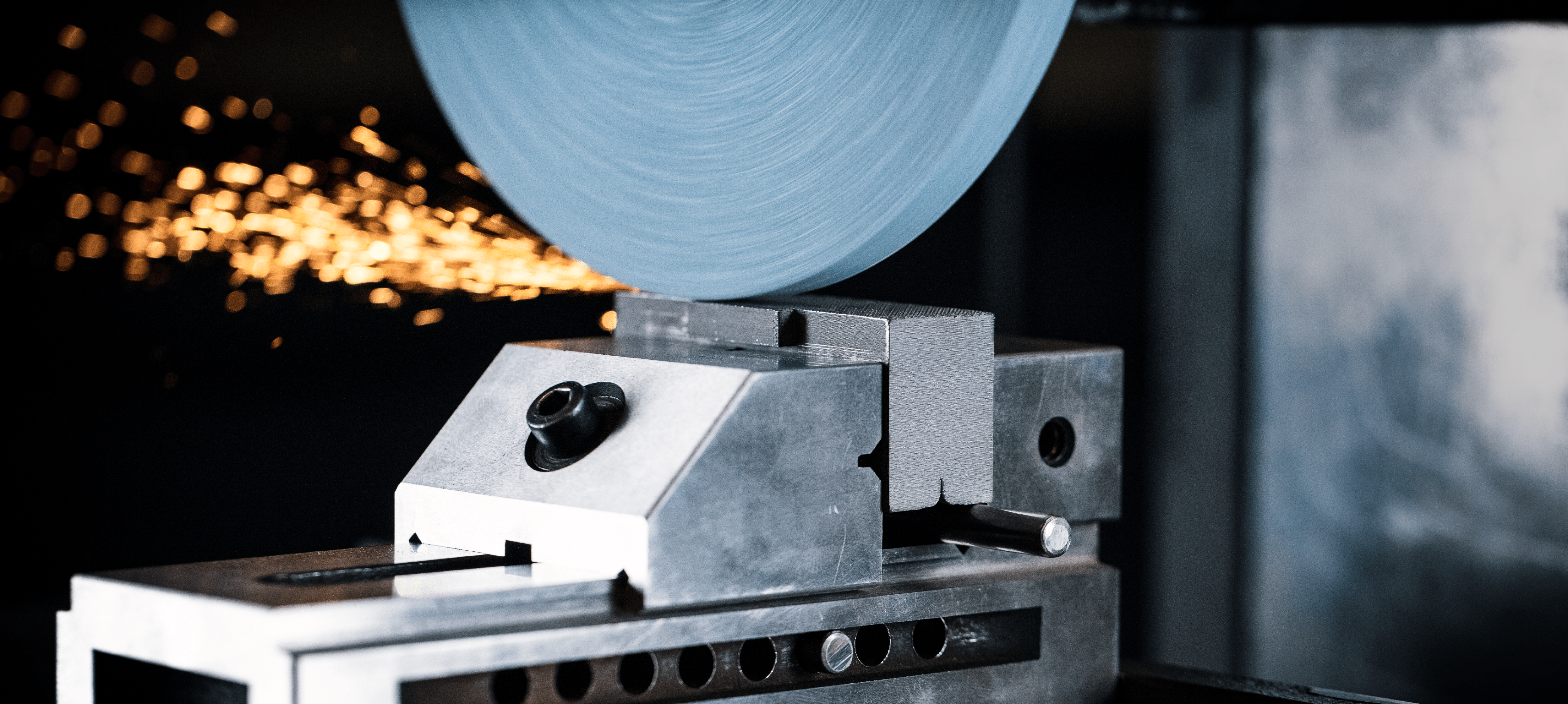
Application 1 – Functional Prototyping
Plastic 3D printed parts give users the freedom to often test form and fit, however, metal 3D printing allows users to produce functional prototypes quickly. Metal 3D printing also allows the user to iterate quickly on the part design. Functional prototyping applications require parts which adhere to specific thermal and chemical essentials. Worm gears, connecting rods, brake calipers and manifolds are all examples of the above functional prototyping applications. By getting rid of lead times, costly complex machining operations, and the need for tooling, product development and time-to-market is accelerated significantly. Expedited fabrication with in-house metal 3D printing gives engineers the ability to explore an iterative design process. This includes functional testing, something which is usually not possible with plastic prototypes.
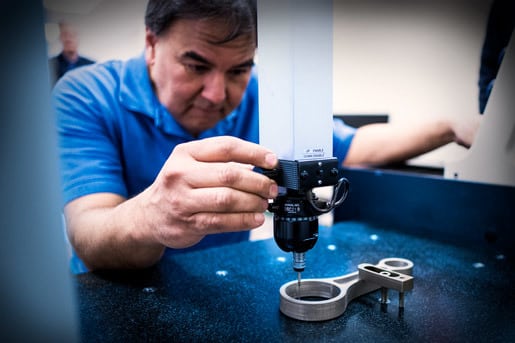
Application 2 – Jigs And Fixtures
Within the production line, jigs and fixtures have complex geometries and are often produced in low volume. Commonly, parts must be made in metal to meet both the stiffness and strength requirements. Frequent use of this results in weqar, so the ability to produce replacement parts quickly is essential to operational efficiency. These parts require repeat-ability and must meet high tolerances. Metal parts that are printed with the Studio System meet strength and durability requirements. They can be post-processed following sintering to accomplish critical dimensions. The nature of the layered BMD printing process is the ability to print assemblies combined together, which is typically not possible with traditional manufacturing.
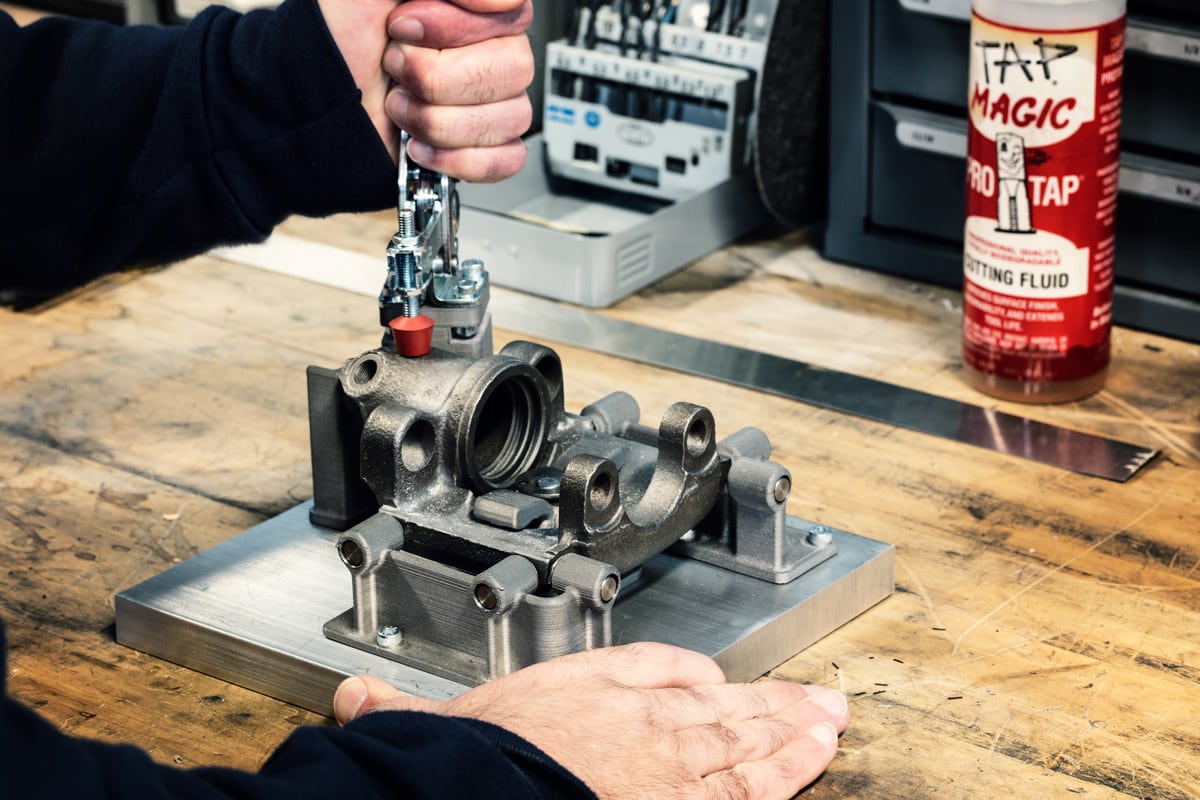
Applicaiton 3 – Tooling
Usually, custom tooling applications come with parts that have complex geometries which can be difficult, and at times, impossible to achieve with traditional manufacturing methods. One example of this is how mold cavity inserts with conformal cooling channels are designed to improve the injection mold cycle’s time and quality of the molded part. A major factor of these applications is initial tooling expenses which factor the overall part cost. Typically, these high costs make it impossible to use processes like casting, injection molding, and extrusion for smaller and customized parts. The Studio System builds reliable, extremely accurate, durable tools that can outperform a plastic.
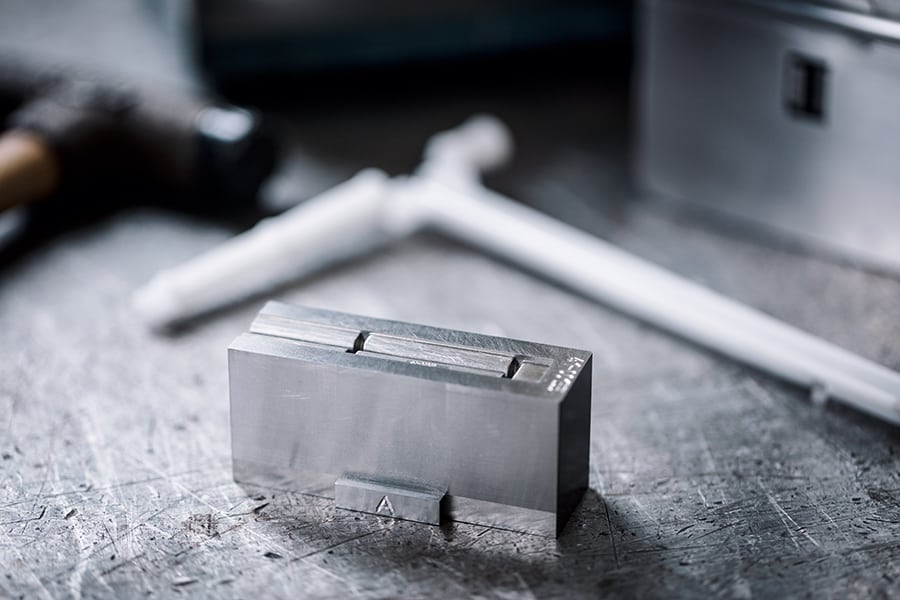
Application 4 – Low Volume Production
Quick, customized parts for low volume production come along with the Studio System, bringing many benefits into the office. Traditionally, the cost for producing metal parts is high. Specifically with geometries which require manufacturing by casting or injection molding. The Studio System results with lower lead times and the part costs don’t increase based on part complexity. Thus allowing designers to focus on the function of the part rather than the limitations of traditional manufacturability.
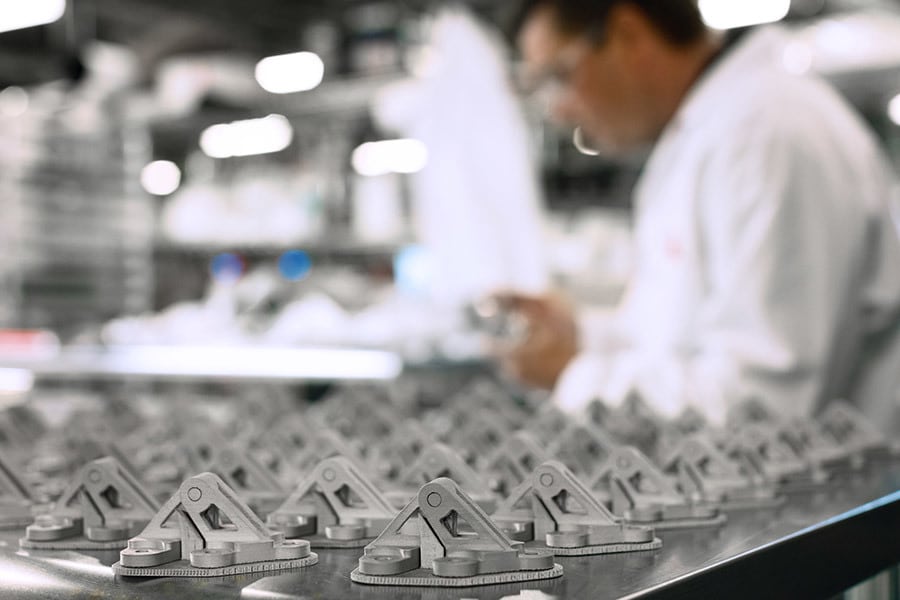
Part Performance
Parts that are printed using the Studio System have the resolution, accuracy and surface finish, similarly to cast parts. Sintered parts meet dimensions within ±0.8% and the parts can be post-processed by CNC, EDM, grinding, rumbling, media blasting, plating, welding and hear treating – to achieve critical dimensions and finish.