Desktop Metal uses a procedure which allows both designers and engineers to embrace the many advantages of additive manufacturing by producing high-performance metal parts in house. The process includes combining the most commonly known and used plastic 3D printing method (Fused Filament Fabrication, also known as FFF), and high-quality alloys found in metal injection molding (MIM)
What Is BMD?
Bound Metal Deposition, is an extrusion-based metal additive manufacturing (AM) process where metal components are created by extrusion of a powder-filled thermoplastic media. Metal powder that is sustained together by both wax and polymer binder. They are then heated and extruded onto the build plate. This shapes the part layer by layer. The binder is later removed by the debind process and then sintered directly after printing. This causes the metal particles to densify.
Common metal AM technologies often include melting powder, or wire feedstock using lasers or electron beams. Many facilities require the accommodation of power and safety. Furthermore, support removal often calls for machining because of localized melting and rapid solidification. This creates complex stress fields within parts, with necessary rigid support structures to aid heat dissipation and resist shrinkage.
Using Studio System™ supports BMD to deliver office-friendly metal 3D printing solutions. Fabrication is not correlated with loose powders or lasers. When it comes to part removal, parts are printed with supports, that are eventually separated by ceramic interface media (or the Ceramic Release Layer™) that doesn’t bond to the metal. Supports become easier to remove by hand when the material disintegrates during the sintering process.
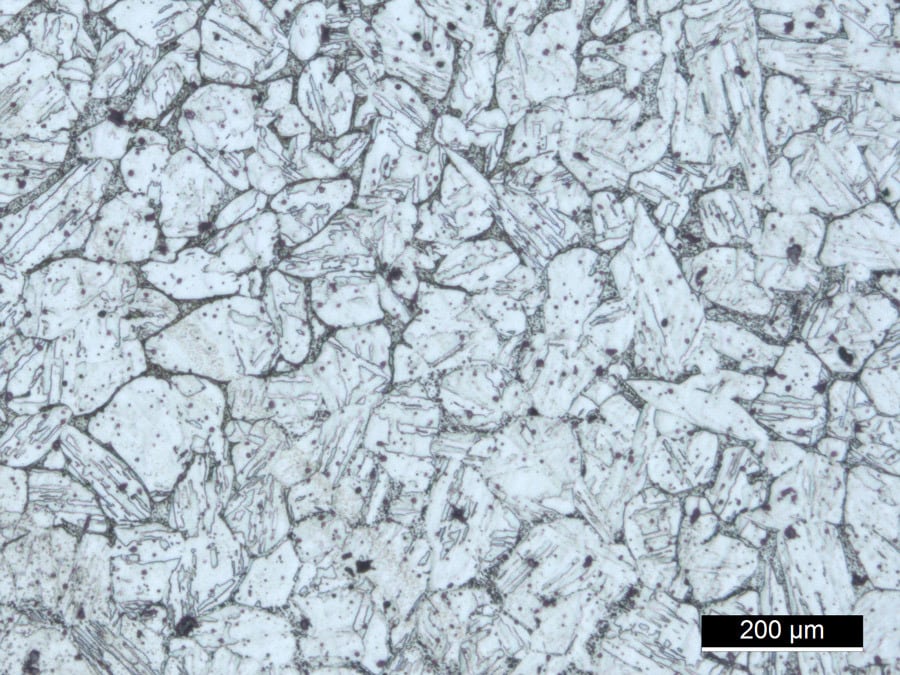
How does it work?
Extruder
Two extruders come with the printer. One focuses on printing bound metal rods, whereas the other is dedicated to the ceramic interface media rods. The media cartridges then feeds the rods which goes into the extruders. Then, it’s heated to soften the binder and later dispensed through the nozzle. To ensure extrusion is reliable, start/stops, and feature accuracy, exact toolpaths and extrusion rates are calculated.
The first thing that gets printed is the raft, following the raft comes the part with its supports. The interface layer printed between the part and the support is constructed to ensure controlled shrinkage throughout the part, while advanced support structures are designed to support the part geometry throughout the print, debind, and sinter processes completely.
In the processes second stage, the part is placed in the debinder. A significant portion (between 30 and 70%) of primary binder is removed by chemical dissolution while the remaining binder assists the part to retain its shape. Open-pore structures are created throughout the part in preparation for sintering.
In the furnace, the part is heated to melting temperatures. Remaining binder is released and metal particles fuse together. This causes the part to densify up to 96-99.8%.The part will shrink to about 17-22% during densification, however, this depends on the material. Both understanding and controlling shrinkage because of sintering is important to achieve dimensional accuracy. Optimized through dilatometry, the sintering cycle is turned to each build and material to ensure repeatable shrinkage and densification.
In order to enable Seperable Supports™, the interface layer printed between the part and its supports does not bond to the metal and prevents the part from sintering with its supports. The ceramic media disinigrates in the furnace, thus making it easy to remove parts from their supports.
Infill Role
Fully enclosed and fine voids are enabled in the BMD fabrication as it is an extrusion based process. All parts are printed with closed-cell infill, besides extremely small geometries. Powder-bed additive manufacturing methods such as SLM (which have the restrictions of opening lattices in order to remove unbound powder from the void spaces) are not compatible with closed-cell infill. Infill affects the print and debind time. The time it takes to debind a part is related to cross-sectional thickness. Infill reduces this as well as the weight of a part while maintaining the design-intent of the part surfaces.
Materials
BMD has the ability to be applied to almost any sinter-able powder that can be made up in a thermoplastic media. This includes stainless steels, tool steels, and other industrially-relevant metallic alloys that can be inconvenient to process by other AM techniques. This includes refractory metals, cemented carbides and ceramics.
Parts And Capabilities
Geometries were unavailable using the bulk manufacturing process, including MIM, press-and-sinter powder metallurgy, and the reusable mold casting techniques. However, extrusion-based additive manufacturing can now build structures and geometries. BMD results in near-net-shape parts, with the strength and accuracy required for the following:
Jigs and Fixtures
Functional prototyping
Low-volume production
Tooling
Cast VS. Printed

The yoke on the right was fabricated by the Studio System. This demonstrates the uniform surface finish and the dimensional accuracy that can be achieved with BMD.
Large Parts
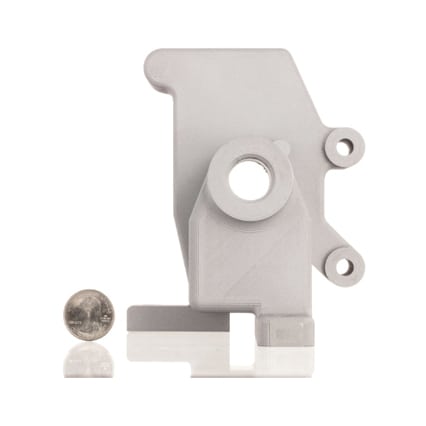
A build volume of 30x20x20 cm on the Studio System printer can accomodate a maximum part size of 25.5x17x17 cm (post-shrink)
A Wide Range of Materials
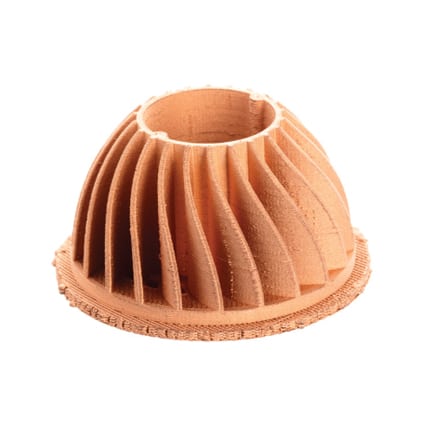
Copper can be difficult to process using powder bed fusion because of its high thermal conductivity and laser absorption characteristics. Copper media can be bound, printed and sintered using BMD.
Print-In-Place Assemblies
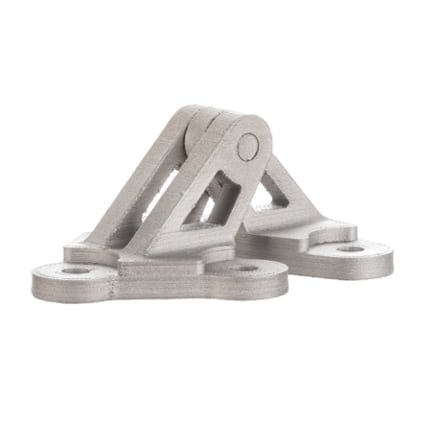
The non-sintering interface layer enables printing of encapsulated assemblies. Forming, assembly, and joining of multiple parts is how its traditionally made.
Customization
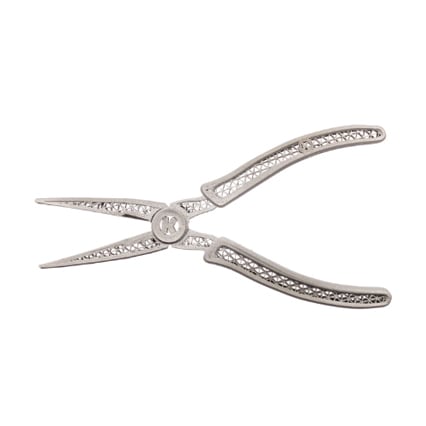
In addition to print-in-place assemblies, BMD allows part light-weighting and rapid fabrication of custom metal parts.
Complex Geometries
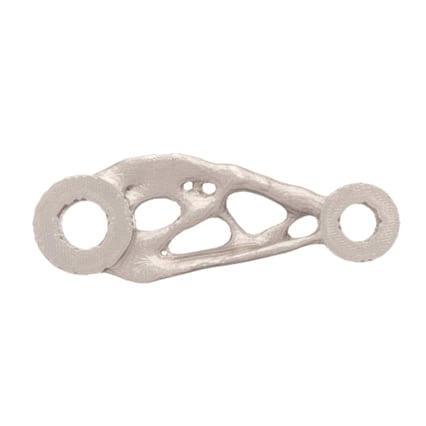
It is crucial to have the ability to print intricate geometries for topology-optimized designs, including organic designs which can be difficult, and at times impossible, to machine.