Custom luxury items require quality and craftsmanship. With Desktop Metal®’s Shop System™, EAC Ornaments can meet customer expectations for customizability, appearance and price.
Founded in 1992 with a focus on the manufacturing of metal accessories for the footwear and leather goods markets, EAC over the last decade diversified its services to include metal accessories for swimwear and lingerie, as well as luxury leather goods, luxury packaging, cosmetics and interior design.
Today, EAC is vertically-integrated, from the 3D design studio up to up to their precious metal plating facility and ornaments final achievement (glueing, enamelling and specific packing) at their Romanian sister company. They work closely with customers to design, prototype and manufacture custom accessories that meet the requirements of each designer’s collections.
Currently, EAC uses a variety of on-site manufacturing methods – including Zamack die casting, hot and chemical stamping of brass and lost wax casting – each of which comes with its own set of challenges.
Like other traditional manufacturing methods, each requires custom tooling that is both expensive and time-consuming to produce, and even slight design changes require the fabrication of new tooling – creating further delays and increasing costs.
The high cost of the tooling also makes low-volume manufacturing a challenge because if EAC wants to keep per-part costs low, they must produce thousands of a particular part to amortize those tooling costs.
By investing in metal 3D printing, EAC hopes to get the best of both worlds:
- a system that eliminates the costly and time-consuming process of fabricating tooling, and is capable of producing parts in large volumes
- maintaining per-part costs low.
With Desktop Metal’s Shop System, they were able to make it possible.
It’s in the DNA of EAC to offer our customers creatively designed products. We have been teasing the benefits of additive manufacturing for our customers, and with the Shop System, that is now a reality – we can partner with our customers and fulfill their designers’ dreams and most creative ideas. Going forward, additive manufacturing should be the future of metallic ornaments, both for the creativity it brings to designers and for the eco-friendly approach and spirit that is involved with the industry.
—
Patrick Chouvet
CEO, EAC Metal Ornaments
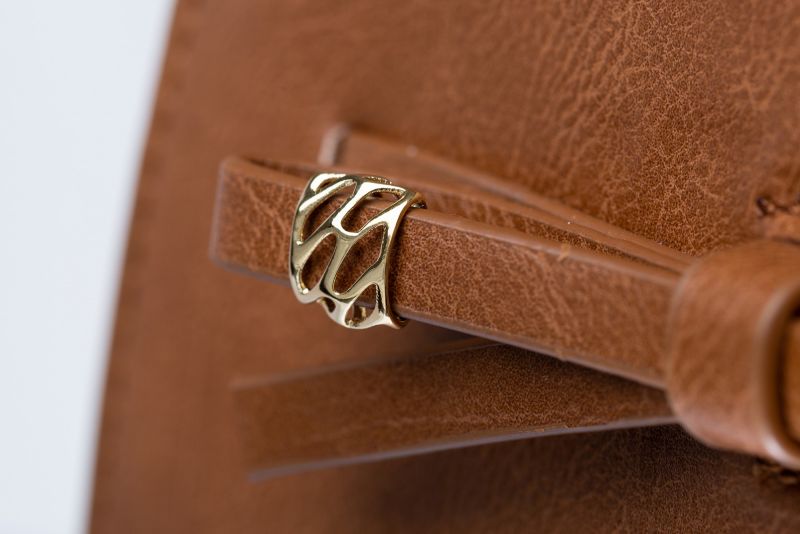
The Shop System also helped EAC reduce the time needed to craft and assemble custom jewelry by 250 hours. The company can now produce 17,600 individual pieces per week, with no assembly required.
And because the Shop System allows for the creation of far more complex geometry than traditional manufacturing methods, EAC is able to work closely with customers to develop distinctive accessories that set their brand apart.
The tooling-free nature of additive manufacturing not only helps reduce the cost of creating those complex parts, but also makes it easy for EAC to adapt as customer demands change from season to season. Designs can be quickly fine-tuned or new parts created before being sent directly to the printer.
The Shop System’s design, which is intended for mid-volume manufacturing, also offers benefits to EAC. And since the parts are supported in the powder bed, there is no need to spend time and labor machining away support structures, further reducing per-part costs.
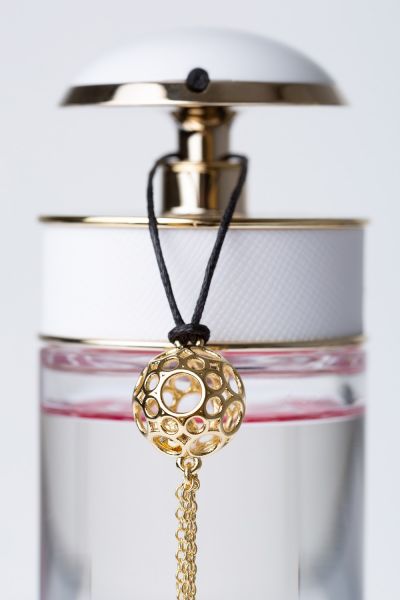