Overview
Built-Rite Tool & Die is a firm located in Massachusetts that combines mold-making and design. With excellent expertise in precision and mold manufacturing, they specialize in the production of molds for plastic injection molding. These molds include complex designs, requiring extensive planning and exact execution.
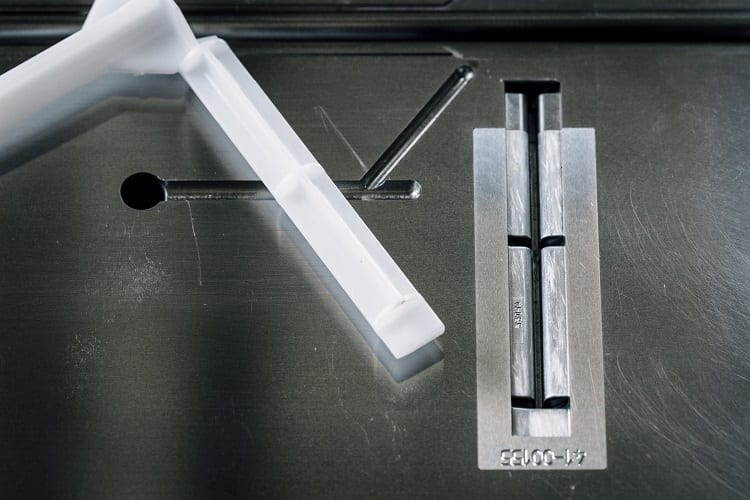
The Challenge
Both small and mid-sized businesses, such as Built-Rite, often face an extreme amount of pressure from international and domestic competitors. Overseas manufacturers offer lower prices, whereas domestic prototyping shops offer rapid turnaround times for small quantities of parts. 3D-printing allows Built-Rite to realize shorter lead times and reduced costs for turn mold services when being compared to domestic prototyping shops. Being able to iterate rapidly is crucial to winning project bids and also for meeting close deadlines.
For Built-Rite, the Studio System™ metal 3D printer launched the ability to produce rapid-turn mold assembly components, using a process which is substantially less labour-intensive compared to other equipment in their machine shop and more cost competitive than a third-party prototyping firm. Closed-cell infill is used in the Studio printer in order to lightweight parts, as well as reduce material usage without impacting the wear resistance that is needed for tooling applications.
Application Constraints |
Studio System™ Benefits |
High Tooling Extended Lead Times Complex Part Geometries |
Minimized cost-per-part and material usage Rapid iteration, in-house Potential to print complex designs |
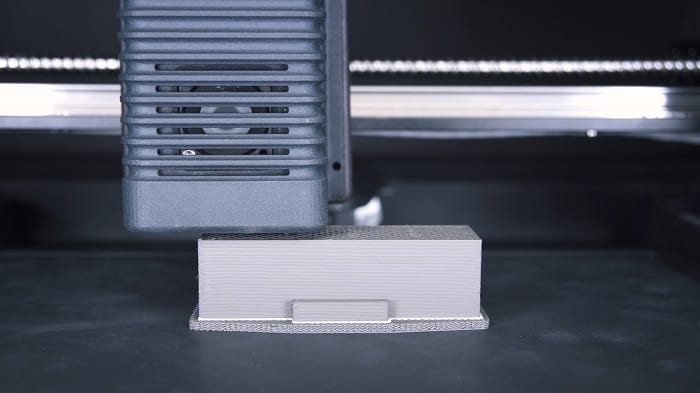
Assessment of Technology Fit
Plastic injection molding is a manufacturing process built for constructing parts in high volume. Now, how does this work? The process is done by injecting molten plastic material beneath high pressure into cavities within the mold in order to shape a part.
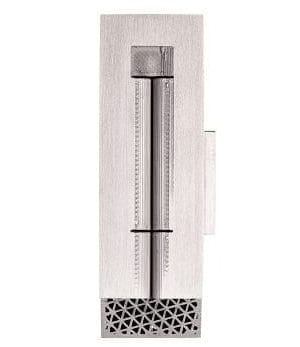
Injection molding for mass production provides a reduced cost-per-part, repeatable outcomes, and minimal waste of injected material. Nearly 32% of all processed plastics go through the injection molding process, therefore making it a ruling manufacturing method.
The mold-making process is extensive, thus calls for accurate planning, as well as accurate execution; all while adhering to client deadlines, iteration, and expectations regarding part quality. A mold is combined with multiple complex cavities, inserts, and cooling channels. Mold tools require being able to withstand repetitive impact, as well as exposure to high-temperature polymers, thus making wear-resistance a crucial feature. Some issues that may arise is high tooling costs and lengthy lead times. Design changes can have a critical impact on both time and cost, so the capability to iterate faster is significant to the overall process efficiency.
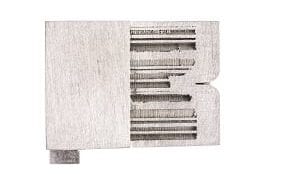
The Studio System uses a technology called Bound Metal Deposition™ where metal rods, metal powder and polymer binders, are both heated and extruded upon the build plate. This shapes a green part layer-by-layer. Furthermore, the part is immersed in the
proprietary debind fluid in the debinder, and is then sintered in the office-friendly furnace! This three-part system was built as an end-to-end solution for in-house metal 3D printing.
The Role of Infill
The mold cavity displayed below has been cross-sectioned to present the infill printed throughout the part. The top view shows the triangular infill pattern that is used to lightweight parts. The end view indicates the capability to increase part thickness selectively, where necessary. Additionally, in this case, the mold-facing
surface is thicker. This is so that post-machining is allowed, and it also maintains durability.
Part Fabrication & Comparison
Built-Rite found an existing mold cavity insert for initial testing. When compared to a third-party prototyping shop, the Studio System conquered reduced cost as well as lead times. Reduction in part weight and the amount of material used was also reduced.
COST SAVINGS |
TIME SAVINGS |
WEIGHT REDUCTION |
90% |
30% |
41% |
Part Dimensions | 2.54 x 3.57 x 7.62 |
Studio System Fabrication | |
Technology | Bound Metal Deposition™ |
Material Type | AISI 4140 steel |
Infill Spacing | 2.8 mm |
Part Mass | 320 g |
Fabrication Time | 50 hours / print 14 hours / debind 6 hours / sinter 30 hours |
Cost Per Part | $47 |
Third Party Prototyping Firm | |
Technology | CNC machining from solid metal block |
Material Type | 4140 steel |
Part Mass | 545 g |
Lead Time | 3 days |
Cost-per-part | $493 |
Evaluation
Injection molding tools need tight tolerances in order to fit the assembly correctly. They also require a polished finish on surfaces which make direct contact with the injected plastics. This is so the part could be easily ejected from the mold. When it was in its “as-sintered state,” part performance was evaluated based on two post-processing stages to observe variation on process parameters and material behaviour, and furthermore, functional testing to observe the part in useSurface Grinding
Built-Rite’s machinists ground the surface of the 3D-printed mold inserts in order to conquer necessary tolerances and surface finish. They assessed whether any unique handling was needed and determined that the parts heated closely to other tool steels and didn’t show any problem in sizing or fitting the inserts into the mold assembly.
Electric Discharge
Machinists used EDM in order to achieve the necessary surface finish on the cavity surfaces of the insert. They assessed the demand for varying the parameter setup, electrode wear, and resulting surface finish. These machinists concluded that it wasn’t necessary to vary the EDM parameters for the printed parts.The electrode wear wasn’t comparable to non-printed inserts. No notable differences in surface finishes were found.
Functional Testing
Following post-machining, the insert was installed in the mold assembly. It was then used to create plastic parts made of acetal, which is a non-abrasive, low-friction plastic material. The temperature of the plastic when it was injected into the mold was nearly 205°C (401°F), where the mold itself is kept at around 82° to 121°C. A test run of almost 100 cycles presented no flaw in the plastic parts made, and the 3D printed insert also showed no sign of wear.
Summary
Success within the original evaluation indicates the possibility of the Studio System for injection molding applications. The system allows injection mold manufacturers to better operations and realize the many benefits that come along with additive manufacturing, without having to rely on other third-party vendors. Included in this is minimized material usage and printing with closed-cell infill, which results in lower costs and the potential to lightweight parts, all while retaining the wear resistance deemed necessary for tooling applications. In response to unexpected design changes, or even short turnaround times, the Studio System allows for mold-makers to iterate on designs quicker, and at a significantly lower cost compared to outsourcing to a third-party mold service.
Follow-up testing includes leveraging design flexibility of the Studio System in order to construct mold inserts with conformal cooling channels which follow the shape of the mold cavity. This allows for uniform cooling of the plastic part instantly after injection to reduce “hot spots” as well as optimize part quality beyond typical manufacturing methods. More testing will also include printing wit H13 tool steel, a material that is often used in this application.
Discover what in-house high resolution metal 3D printing can do. Explore the Desktop Metal Studio System