Based in Karnes City, Texas, PGV Industries has more than three decades of experience in manufacturing equipment for the oil and gas, aerospace, robotics, and automation industries. Along with traditional manufacturing via CNC machining, the company is now moving into next-generation manufacturing by integrating production-level metal 3D printing into its capabilities.
The Challenges
After more than three decades of manufacturing parts using traditional methods – particularly CNC machining – for a wide range of customers, PGV is very familiar with the challenges manufacturers face:
Tooling Costs & Lead Time
Traditional volume manufacturing – whether machining, casting, or forging – requires “hard” tooling and fixturing which often costs tens of thousands of dollars and weeks or months to fabricate.
Lack of Agility
Beyond cost and lead times, though, the need to fabricate tooling can have significant impacts on a company’s ability to quickly respond to new or changing customer requirements. With these constraints, manufacturers often struggle to quickly respond to new or changing customer requirements, and as a result, changing part designs become a daunting proposition.
For many of the same reasons, iterating on existing designs can be equally challenging. While many companies may print prototypes in plastic, those parts can only be used to test form and fit – functional testing requires creating metal parts, a process that is both expensive and time-consuming.
Inventory Management
The long lead times needed for traditional manufacturing also create challenges for inventory management. Providing customers with spare or replacement parts in a timely fashion requires manufacturers to warehouse and track vast inventories of parts, in addition to the tooling and fixturing required to produce them.
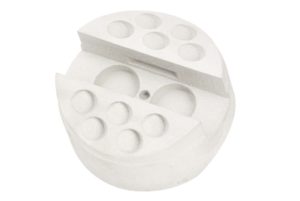
With the growth of metal 3D printing in recent years – both in its abilities to create complex, end-use parts and its adoption by industry – PGV saw in the technology a way to address each of those challenges. And in the Desktop Metal Shop System, they found the ideal system to do it.
The Shop System™ Solution
The Desktop Metal Shop System’s impact at PGV has been undeniable. In addition to reducing costs and lead times, the system has enabled PGV to grow its business by freeing up internal production capacity and simplified inventory management – all of which add up to more agile, efficient operations.
Expanded business & services
The increased speed of production enabled by the Shop System allows PGV to be far more agile, taking on small- to medium-sized jobs that might previously have been no bid due to high tooling costs and long lead times. While it would normally take as many as five processes to machine some downhole tools, the Shop System dramatically simplifies the process, freeing up PGV’s internal machine shop to take on other jobs. The lack of tooling also makes it easy for PGV customers to keep pace with the ever-changing world. With no need for tooling, the company can quickly update part designs to meet customers’ evolving needs or create new designs without the long delays associated with traditional manufacturing.
The system allows the company to create parts, test them under real-world conditions, then iterate on designs based on the results, and do it all in less time than it would take to create traditional, hard tooling.
Reduced physical inventory by 50%
By opening the door to on-demand production of parts, the Shop System allowed PGV to reduce their parts inventory by as much as 50%. Rather than warehousing and tracking large numbers of parts, designs can be stored in “digital warehouses,” and be retrieved and printed only when needed.
Reduced lead times by 50–80%
With the transition from machining to binder jetting, the company saw similar reductions in lead times. Jobs that had once required as many as 5 unique machining steps were reduced to just a single step. Depending on the part, lead times were cut by anywhere from 50 percent to as much as 80 percent.
Why Desktop Metal®’s Shop System?
Among the key factors for the company were the excellent material properties displayed by Shop System parts. In key characteristics like strength, ductility, and hardness, parts produced on the Shop System meet or exceed those of traditionally-manufactured parts, ensuring they can stand up to the tough conditions they’ll face in downhole operations. The print quality of Shop System parts means PGV rarely needs to post-process parts – they can go straight from the furnace to end-use applications in the field. Cost – particularly per-part cost – was also an important consideration. By eliminating the need for tooling, the Shop System helps PGV to realize thousands in savings in tooling costs, while still delivering high-quality, end-use parts.
Application examples
Downhole Tool Slip
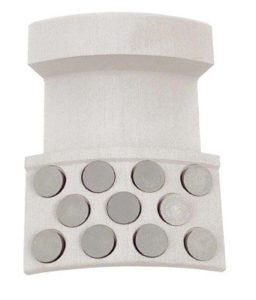
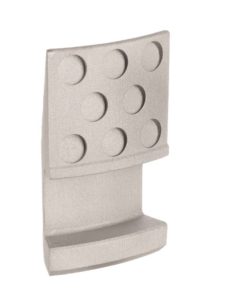
These slip parts are key components in a production packer used in oil and gas extraction. After being lowered into place, the wedge-shaped slips are pressed into place, causing the
“buttons” on the face of the slip to bite into the inside casing of the well, forming a tight grip so the tool won’t release or move while under pressure. Once in place, tools slips can face intense pressure, so it was critical these parts be strong enough to withstand those forces. The excellent material properties of Shop System parts ensured these tool slips are able to perform under real-world conditions. Because the Shop System eliminates the need for tooling, PGV is able to manufacture these slips in far less time than it would take to machine the parts, allowing the company to dramatically reduce their inventory of spare parts. The company is also able to easily adjust the design of this part to suit different scenarios and send the new design into production without delays.