Ready for Additive Manufacturing 2.0
cDLP 3D printing technology (Continuous Digital Light Processing) is a vat-polymerisation additive manufacturing process that enables high-volume and scalable part production. Through combining the energy of light with long-chain material chemistry and industrial-grade materials, the cDLP 3D printing process is an effective way to produce complex end-use parts with the speed and economics comparable to traditional manufacturing methods like injection molding.
For a range of industries and applications, cDLP 3D printing technology is transforming production workflows. Speak to one of our polymer additive manufacturing experts to discover ways to implement this technology in-house, or work with our production
Key Benefits
Applications
What is DLP 3D Printing and How Does it Work?
The Process
DLP (Digital Light Processing) 3D printing is a process in which a DLP projector light source cures photosensitive material/resin. At the heart of the DLP process is a DLP chip; a precision device made up of millions of microscopic mirrors which can be individually controlled to produce clear and crisp images.
Want to see it for yourself?
CDLM Domeless 3D Printing
To print continuously (without peeling) requires flowing oxygen through a permeable film just above the print bed to create a “dead zone”. Within this “dead zone,” the polymerization process is inhibited ensuring the
layer being printed adheres to the layer above and not the printing bed film. This “dead zone” is what enables continuous printing, where the build plate can continually move in the Z-axis, leading to faster, more
reliable prints.
On competitor “dead zone” printers, by comparison, air pressure from the flowing oxygen causes the film to dome up. Printing parts on that domed surface greatly impacts resolution along the Z-axis, as well as the
ability to print flat parts on the build plate.
ETEC’s CLDM technology uses over 200 thousand pillars to hold the film perfectly flat, resulting in significantly better Z‐axis resolution and allowing for the printing of flat parts straight to the bed with no supports.
Powered by Oxygen
Oxygen (O2) inhibits polymerization and that particular small area, where the oxygen and the photopolymer blend on the surface, is called the dead zone. This translates into a thin layer of material that doesn’t cure or harden, even when directly exposed to light. Therefore, in order to successfully build continuously, the projector light needs to be strong enough to accurately and rapidly transfer through the dead zone and cure the resin. This dead zone proved to be beneficial because it can be used as a no-stick zone, meaning that the parts no longer have to be peeled from the material tray in between exposure layers. This approach allowed for 3D printing in free space.
Despite the discovery of the dead zone’s benefits, over the years, continuous 3D printing saw another challenge that needed to be overcome in order NOT to compromise speed, part accuracy, or isotropic properties. To continuously 3D print in free space, the usual practice was to deliberately insert oxygen into the process to create a dead zone by adding the O2 below a thin rectangular piece of oxygen-permeable film that was covering the entire build area. Thus, the film was allowing just enough oxygen to penetrate to create a dead zone on which to free-print.
Competing Continuous
3D Printers
EnvisionTEC’s Advanced
cDLM Technology
Materials
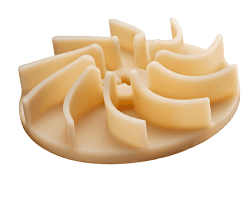
E-Toughflex
Material: Hard plastics
E-Toughflex features very high flexural modulus and strength, as well as hydrophobic properties.
Full Description
E-ToughFlex is ideal for producing tough end-use parts with a beautiful surface finish similar to ceramic and good abrasion resistance.
Specs
- Tensile Strength: 67.5 MPa
- Tensile Modulus:1340 MPa
- Elongation at Break: 16%
- Impact Strength (Notched): 20 J/m
- Heat Deflection Temperature: at 1.82 MPa 58° C
Application
- Consumer Goods
- Education
- Medical Devices
- Manufacturing
Technology/Process
- DLP (Digital Light Processing)
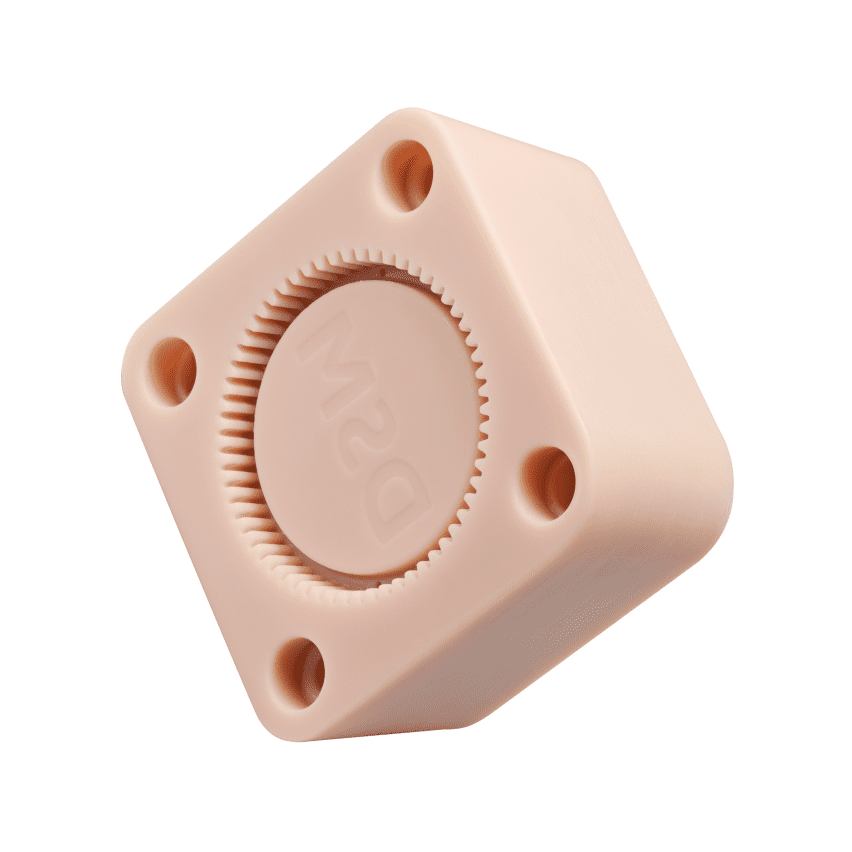
E-Perform
Material: High-temperature plastics
E-Perform is high stiffness and high heat tolerance material, ideal for producing 3D printed injection molds.
Full Description
Printed E-Perform molds can resist wear from highly abrasive materials, such as fiber-filled plastics.
Key features:
- High heat tolerance
- High stiffness
- Fast printing, easy processing and finishing
- High Accuracy
- Excellent detail resolution
Specs
- Tensile Strength: 87 MPa
- Tensile Modulus: 9000 MPa
- Elongation at Failure: 1.4 %
- Heat Deflection Temperature: at 1.81 MPa 160°C
Application
Ideal for end-use parts that require steady performance in high pressure and harsh environments, such as parts for wind tunnel testing.
Technology/Process
- DLP (Digital Light Processing)
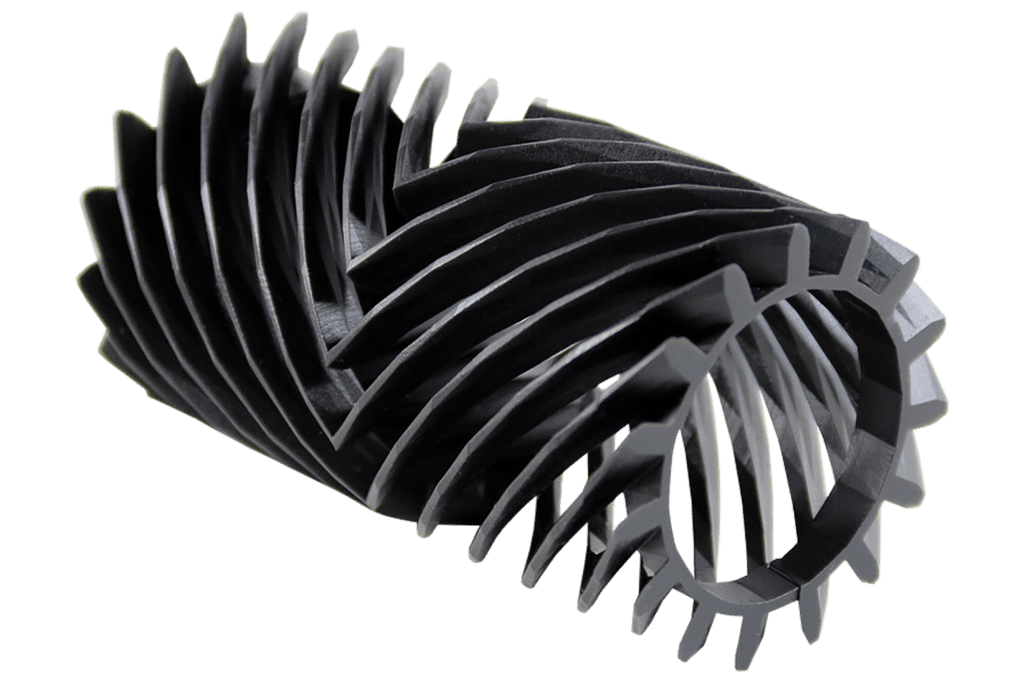
LOCTITE® 3955 FST HH
Material: LOCTITE 3955 FST HH
This 3D printing material is a high-performance, high modulus product that ensures excellent flexural and tensile properties with outstanding flame retardance.
Full Description
Henkel® LOCTITE 3955 FST HH displays high HDT (heat deflection temperature) enabling it to be used in harsh environments without deformation or deflection. It passes flammability standards such as UL94 V-0 and AirBus AITM2-0002. It has been tested in QUV exterior weathering conditions (ASTM G-154-Cycle 1) for 1600 hours with less than a 15% change in flexural properties.
Specs
- Tensile Stress at Break: 77 MPa
- Young’s Modulus: 3673 MPa
- Elongation at Failure: 2.5%
- Flexural Stress at Break: 138 MPa
- Flexural Modulus: 5200 MPa
- Flexural Strain at Break: 2.9%
- Heat Deflection Temperature at 0.455 MPa (Green): 59.2°C
- Heat Deflection Temperature at 0.455 MPa: >250°C
- Heat Deflection Temperature at 1.82 MPa: 197°C
- Viscosity @ 65°C: 800-1100 cP @ 25°C
Application
- Aerospace
- Automotive
- Consumer Goods
- Manufacturing
Technology/Process
cDLM – Continuous Digital Light Processing
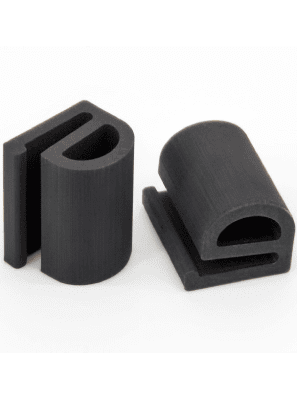
LOCTITE® IND402
Elastomer
This material maintains excellent tensile strength with high energy return and does not require secondary thermal post-processing.
Full Description
E-IND402 is a single component elastomer material with excellent green strength and does not require thermal post-processing.
Key Features:
- Elastomeric behaviour
- High resilience
- Good rebound performance
Specs
- Hardness: Shore A 76
- Tear Strength: 28 kN/m
- Elongation at Break: 230%
- Tensile Stress at Break: 5.5 MPa
Application
Ideal for elastomer applications that require lattice structures, such as vibration isolators.
- Aerospace
- Automotive
- Consumer Goods
- Manufacturing
Technology/Process
- DLP (Digital Light Processing)
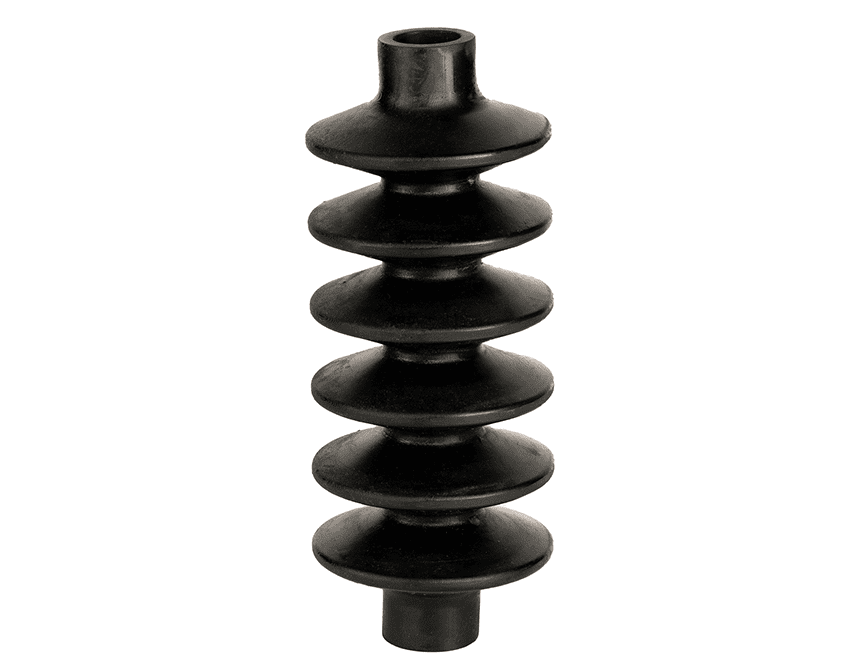
Elastic ToughRubber™ 90 | Adaptive3D
Elastomer
ETR 90 is a high-strength rubber material. It is the toughest 3D printing elastomer on the market that can mimic the leading injection molded thermoplastic polyurethanes.
Full Description
Key Features:
- One-part, one-pot (no mixing required)
- High elongation
- Extremely tough
- Feels and performs like rubber
- Large part size possible, high resolution, smooth surface
- Available in black colour
Specs
- Hardness: Shore A 90
- Tear Strength: 38 kN/m
- Elongation at Break:190%
- Tensile Stress at Break: 14 MPa
Application
- Aerospace
- Automotive
- Consumer Goods
- Manufacturing
- Dampening components
- Seals & baffles
Technology/Process
- DLP (Digital Light Processing)
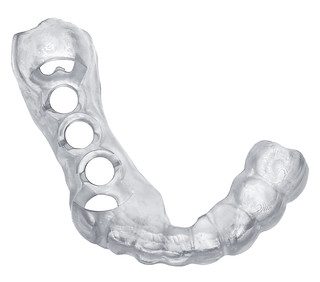
E-Guide Soft
Biocompatible 3D printing resin
E-Guide Soft is a high-performance, high modulus, biocompatible 3D printing resin boasting excellent flexural and tensile physical properties.
Full Description
Stiffness combined with toughness makes this material ideal for use in a wide variety of impact-resistant medical devices.
Specs
- Flexural Strength (ASTM D790): 36-44 MPa
- Flexural Modulus (ASTM D790): 1240-1280 MPa
- Elongation at Break (ASTM D638): >90%
- Hardness, Shore D (ASTM D2240): 80
- IZOD Impact Notched (ASTM D256): 63-65 J/m
- Youngs Modulus (DIN EN ISO 527-1:1996): 340-360 MPa
- Ultimate Tensile Strength (DIN EN ISO 527-1:1996): 19-21 MPa
- Strain at Break (DIN EN ISO 527-1:1996): 80-120 MPa
- Ultimate Flexural Strength (DIN EN ISO 20795-2:2013): 35-39 MPa
- Flexural Modulus (DIN EN ISO 20795-2:2013): 1000-1200 MPa
- Water Sorption, µg/mm3 (DIN EN ISO 20795-2:2013): Passed
- Water Sorption, µg/mm3 (DIN EN ISO 20795-2:2013): Passed
- Cytotoxicity (ISO 10993): Passed
- Irritation (ISO 10993): Passed
- Sensitization (ISO 10993): Passed
Application
- Medical devices
- Manufacturing
Technology/Process
- cDLM – Continuous Digital Light Processing
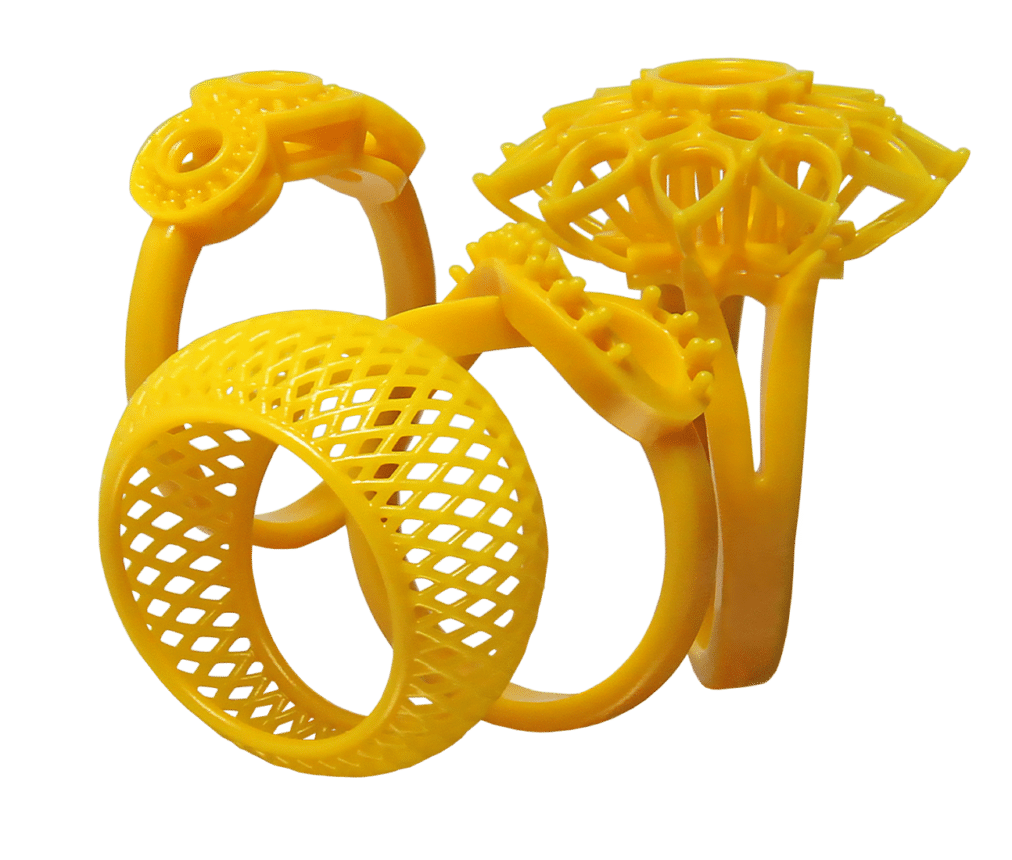
Easy Cast 2.0
3D Printing resin for castable models
Easy Cast 2.0 is a photopolymer with the highest wax content available in 3D printing today. It is a material for the high-speed printing of castable models.
Full Description
Easy Cast 2.0 C is a material developed for printing exclusively on EnvisionTEC’s patented cDLM printers. Because the continuous digital light processing technology has almost zero separation forces during printing, it allows for 90% liquid wax content in the formulation. Consequently, patterns printed in Easy Cast 2.0 C feature burnout similar to injection wax.
Specs
- Viscosity: 200 cP @ 30°C
- Density: 1.08 g/cm3
- Temperature @ 5% Weight Loss: 263°C
- Ash Content (after 900°C): 0
Application
- Jewelry
Technology/Process
- cDLM – Continuous Digital Light Processing
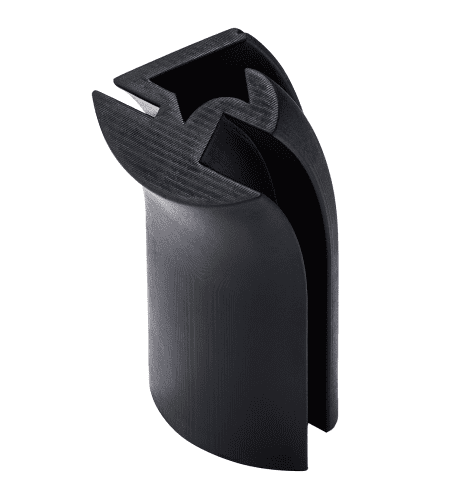
Elastic ToughRubber™ 70 | Adaptive3D
Elastomer
ETR70 is a tough, high-strength rubber with shore A70 hardness and extremely high elongation material, ideal for the rubber, polyurethane, and foam industries.
Full Description
This material may be used as an EVA ( Ethylene-Vinyl Acetate) rubber substitute for high-quality 3D prints that are tough and flexible as well as usable and functional. Excellent for vibration isolation parts, ETR70 has exceptional damping properties and excellent elongation, which makes it great for applications like gaskets and housings.
Key Features:
- One-part, one-pot (no mixing required)
- Extremely high elongation
- Extremely tough
- Feels and performs like rubber
- Large part size possible, high resolution, smooth surface
- Available in black colour
Specs
- Hardness: Shore A 70
- Tear Strength: 31 kN/m
- Elongation at Break: 400%
- Tensile Stress at Break: 7.6 MPa
Application
- Aerospace
- Automotive
- Consumer Goods
- Manufacturing
Technology/Process
- DLP (Digital Light Processing)
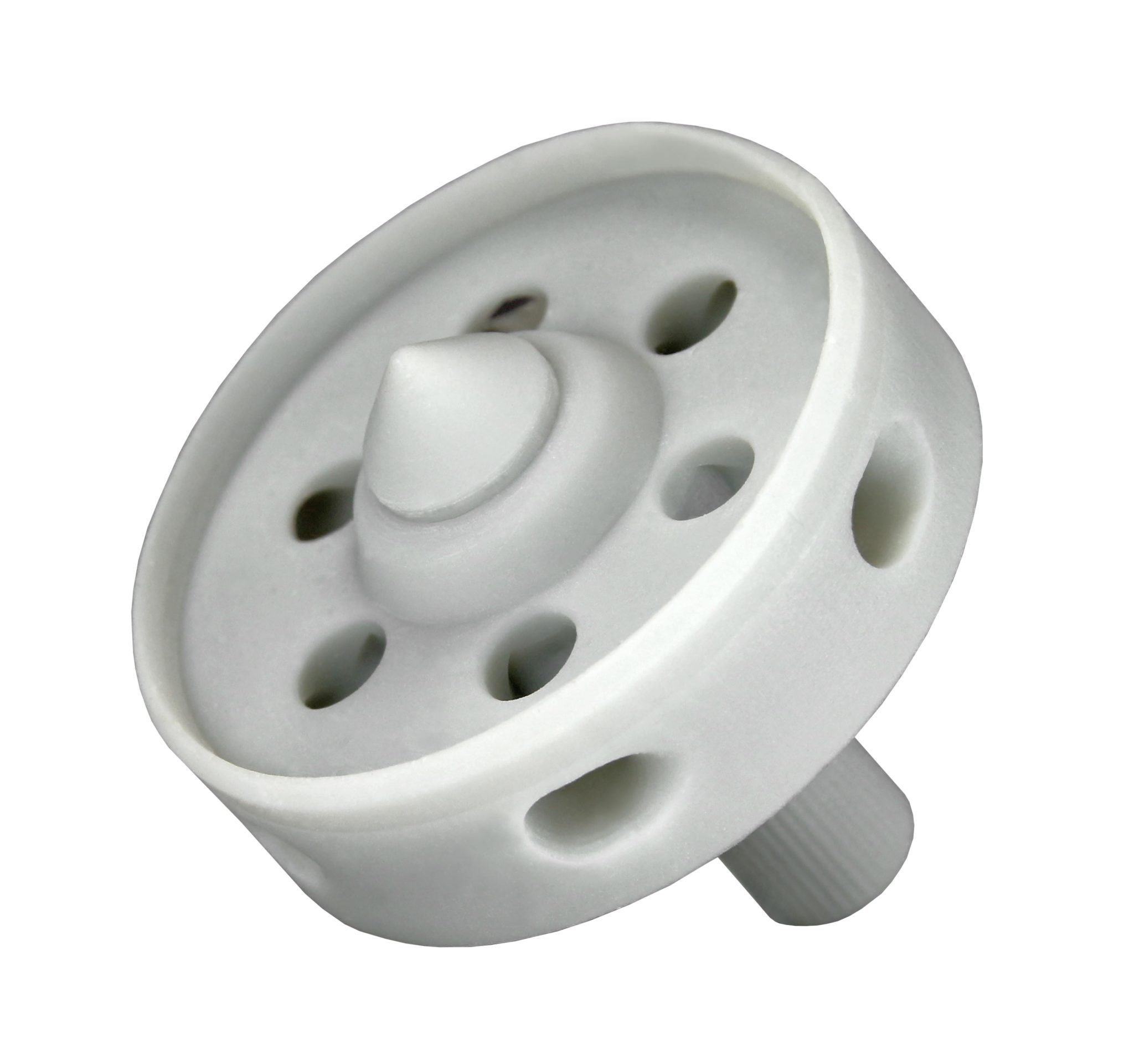
Q-View
Ideal resin for prototyping
Q-View resin is ideal for providing fast design verification models and is capable of high printing speeds for the full build envelope.
Full Description
Designers and can create custom pieces and prototypes for their customers in record times for final fit and design verification. It can also be used as a pattern when built in high resolution to produce a silicone mold.
Specs
- Tensile Strength at Break: 5160 psi (ASTM Method D 638-10)
- Tensile Elongation at Break: 3.7% (ASTM Method D 638-10)
- Tensile Modulus: 217 psi (ASTM Method D 638-10)
- Flexural Strength at Break: 11 800 psi (ASTM Method D 790)
- Flexural Modulus: 332 psi (ASTM Method D 790)
- Durometer D Hardness: 85 D Shore (ASTM Method D 2240)
- Izod Impact Strength: 0.392 ft-lbf/in (ASTM Method D 256-10)
- Heat deflection temperature at 264 psi: 43.3° C (ASTM Method D 648-07)
- Heat deflection temperature at 66 psi: 70° C (ASTM Method D 648-07)
Application
- Entertainment
- Jewelry
- Consumer Goods
Technology/Process
- cDLM – Continuous Digital Light Processing
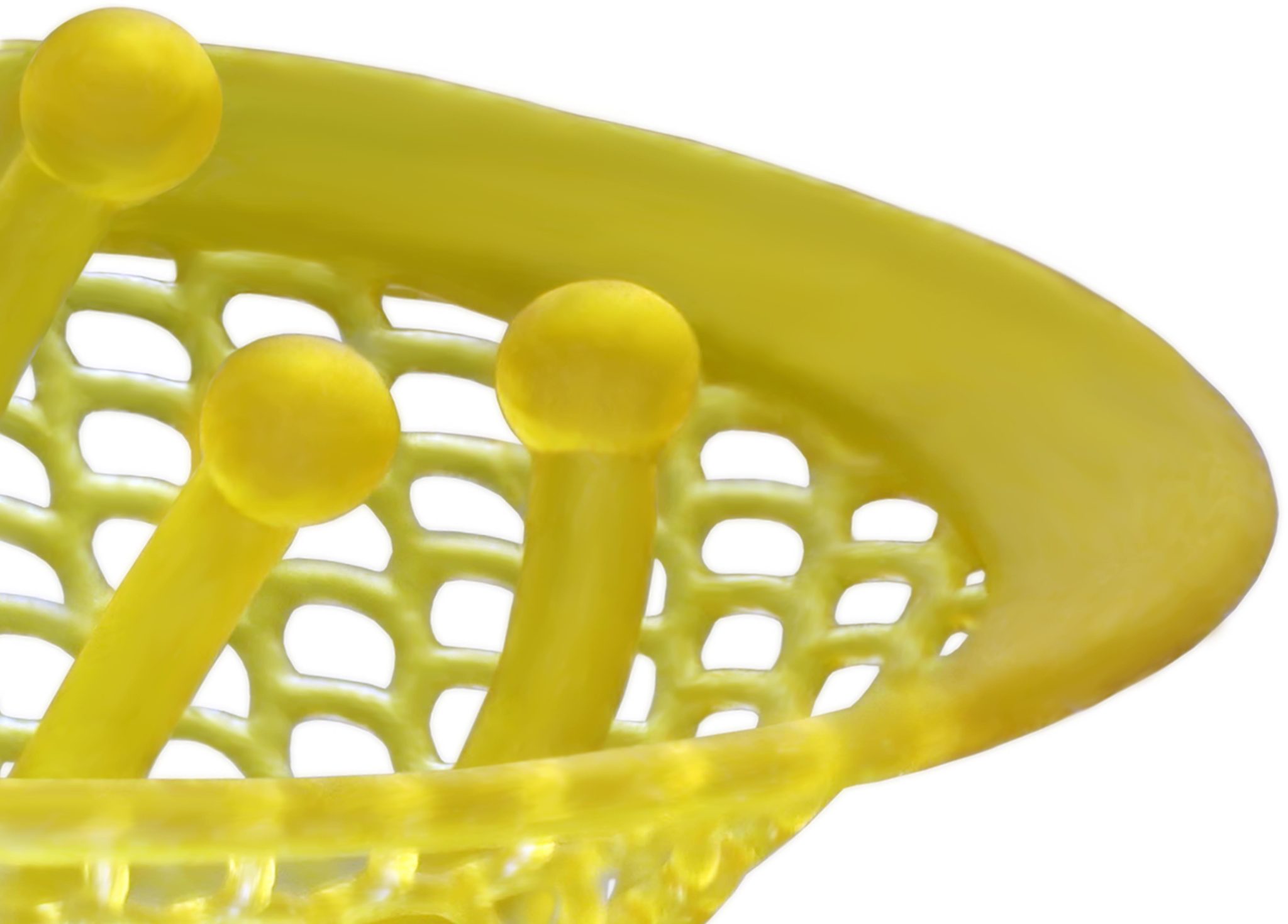
PIC 100 Series
Plastic Investment Casting (PIC) material
The PIC 100 Series – Plastic Investment Casting (PIC) resin with no wax content has been developed for direct investment casting applications.
Full Description
These casting applications offer excellent burnout properties and build with the highest quality and crisp detail.
Parts made using PIC 100 resins evaporate at moderate burnout temperatures without reacting with investment and offer extremely low thermal expansions. They are optimally suitable for producing precious metal castings. PIC 100 resins build extremely smooth surfaces. The burnout process is ash-free, allowing for a casting that is free from porosity.
The highest quality details, standard burnout procedures, and high-speed building qualify PIC 100 resins for producing high-quality parts in the jewelry market for production capacity direct investment casting.
Specs
- Viscosity: 361.7 MPa
- Tensile Strength: 16.8 MPa
- Elongation at Break: 7.46%
- Flexural Strength: 23.0 MPa
- Flexural Modulus: 404.0 MPa
- Bending Strain: 10.2%
- Izod Impact – Notched: 11.03 kJ/m2
- Density: 1.178 g/cm3
- Hardness (Shore D): 69
- Ignition Temperature: 350°C
- Colors Available: Gold, Green
Application
- Entertainment
- Jewelry
- Consumer Goods
- Education
- Manufacturing
Technology/Process
- cDLM (Continuous Digital Light Processing)
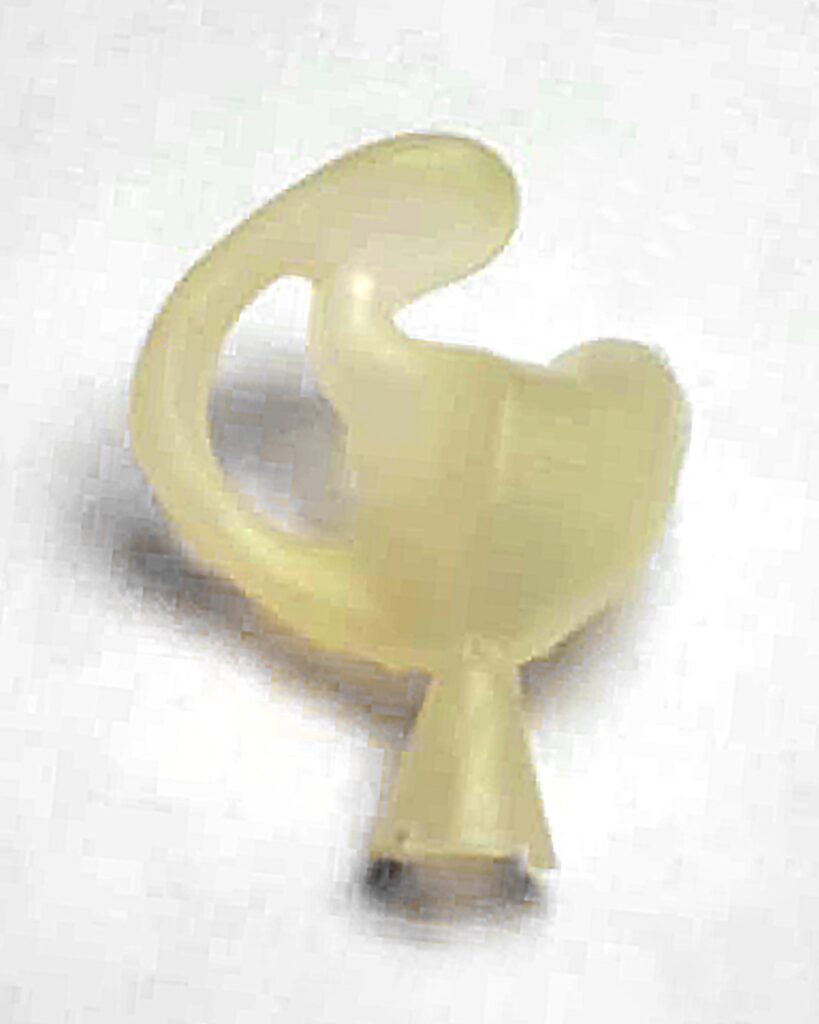
E-Aquasol
Water-soluble 3D printing resin
A water-soluble 3D printing resin, ideal for printing molds in a wide variety of industrial applications. Manufacturers can shell-cast thin-walled parts with high feature resolution.
Full Description
Due to its high water solubility, E-Aquasol resin is a great replacement for more aggressive solvents such as caustic.
This material was developed in joint collaboration between EnvisionTEC and Sartomer, both leading experts in 3D printing and advanced materials.
Specs
- Tensile Strength: 7.9 MPa
- Elongation at Break: 2.65%
- Tensile Modulus: 542 Mpa
- Flexural Strength: 16.7 MPa
- Flexural Modulus: 1840 MPa
- Viscosity @ 30°C: 28 cP
- Density: 1.2 g/cm3
Application
- Aerospace
- Entertainment
- Automotive
- Consumer Goods
- Education
- Medical Devices
- Manufacturing
Technology/Process
cDLM – Continuous Digital Light Processing
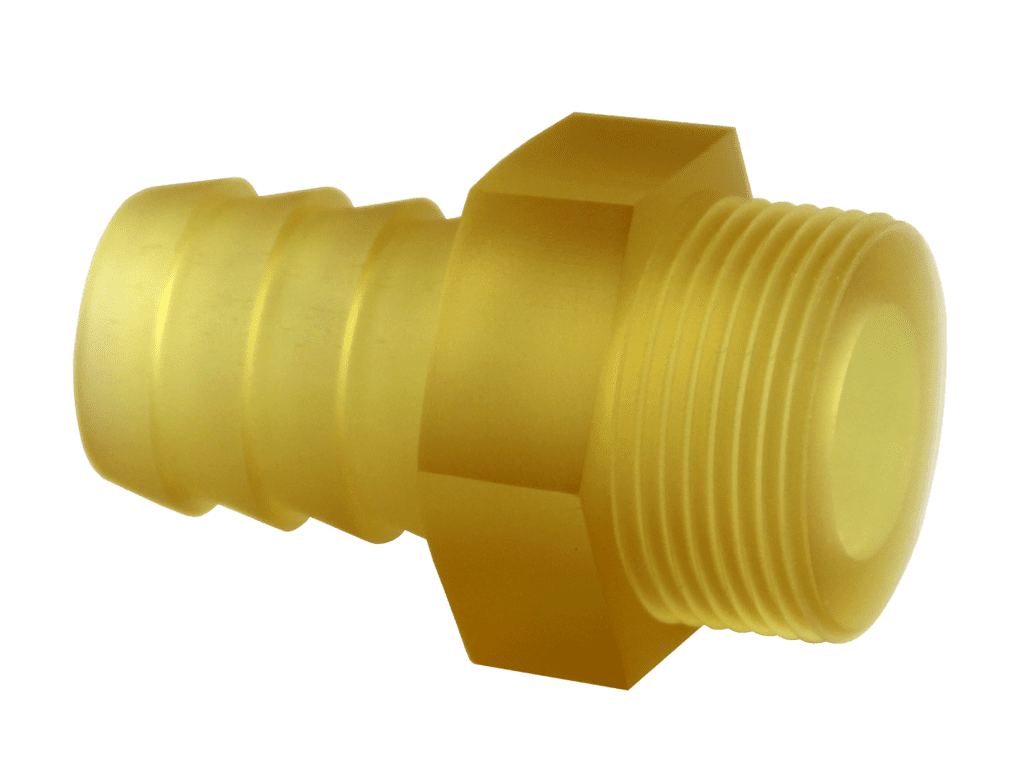
R5-385
Chemical and water resistance material
R5-385 produces robust, accurate and functional parts with superior chemical and water resistance, as well as excellent tolerance to a broad range of temperature and humidity fluctuations.
Full Description
Parts build in R5-385 exhibit superior fatigue properties and excellent surface detail as well as impressive stability over long periods of time.
R5-385 material is an update on the original R5 material, one of EnvisionTEC’s earliest materials still in use around the world, re-engineered for optimal performance in 3D printers utilizing 385nm wavelength light sources.
Specs
- Tensile Strength: 54 MPa (ASTM Method D638)
- Elongation at Break: 5 % (ASTM Method D638)
- Tensile Modulus: 2250 MPa (ASTM Method D638)
- Flexural Strength: 90 MPa (ASTM Method D790)
- Flexural Modulus: 2500 MPa (ASTM Method D790)
- Impact: 35 J/m (ASTM Method D256)
- Hardness (Shore D): 85 Shore (ASTM Method D2240)
- HDT @ 1.82 MPa: 54°C (ASTM Method D648)
- Viscosity: 395 cP @ 30°C
Application
- Aerospace
- Entertainment
- Automotive
- Consumer Goods
- Education
- Manufacturing
Technology/Process
cDLM – Continuous Digital Light Processing