Tooling design plays a significant part in the manufacturing process. if it’s done incorrectly, major complications can take place on both the launch and success of a product. Various amounts of these tools can range from simple drilling, to a complex, multi-piece assembly fixture.
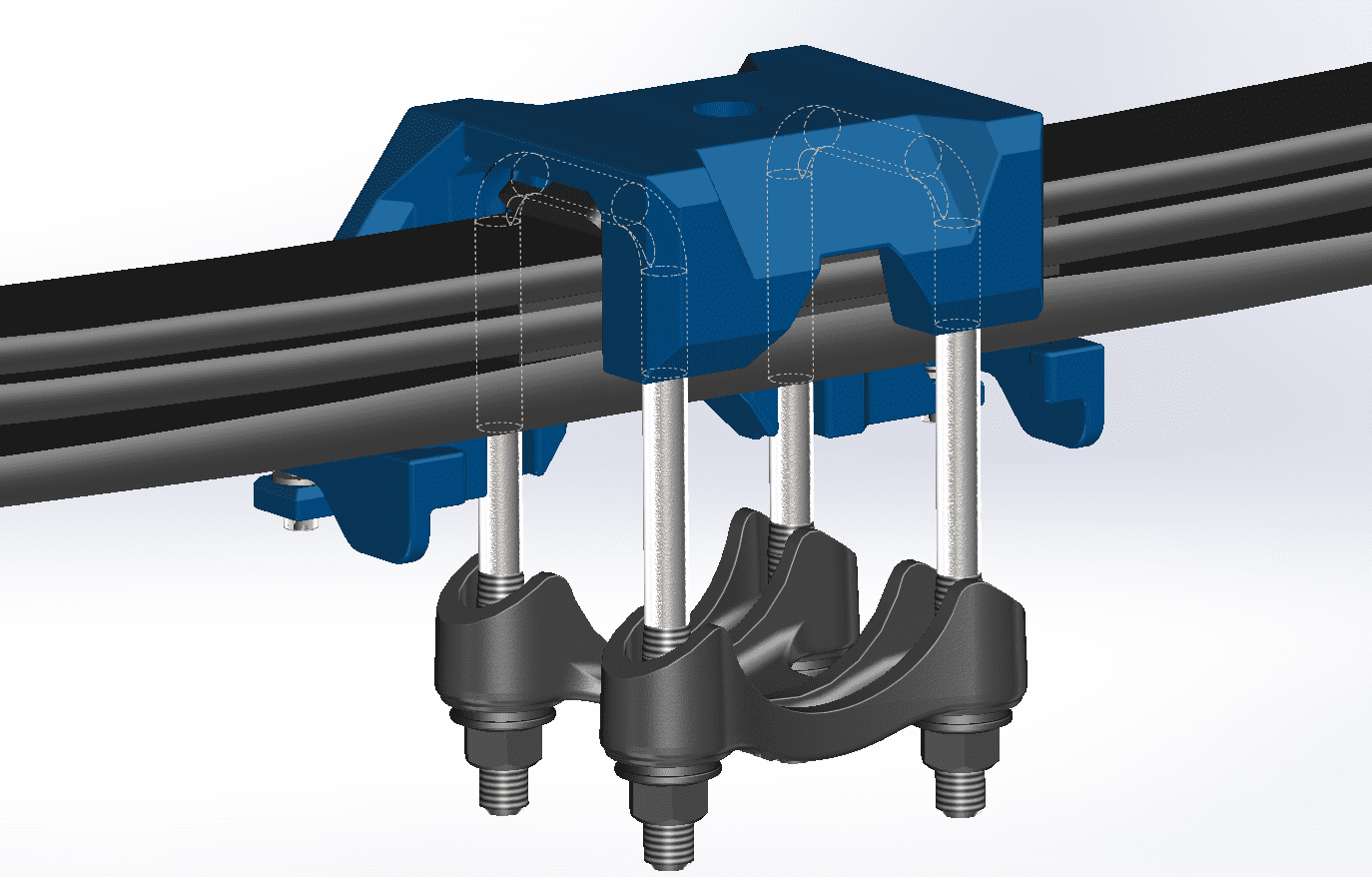
However, no matter what the type and intended usage, manufacturing engineers often attempt in finding a balance between cost, lead time, and performance without passing hidden costs onto the consumer. One proposal which has proven viability to focus on these challenges s the implementation of Additive Manufacturing (AM). Contrary to subtractive methods of manufacturing, additive manufacturing allows for complex, distinct application designs without having to sacrifice cost or lead time.
Additive manufacturing demands a specific approach for design, fabrication and validation compared to traditional methods of manufacturing. Designing for additive manufacturing (DFAM) is necessary to reduce as much cost and lead time, without sacrificing performance for manufacturing tooling. Taking a tool design from CAD to production can regularly be convoluted because of limitations in the software used to prepare the design to be printed. This calls for Jigs and Fixtures for GrabCAD Print, a new, progressive FDM processing software that allows the user to meet their use case requirements by simply adjusting the strength, rigidity, and fill style of bodies including the faces/surfaces on the part.
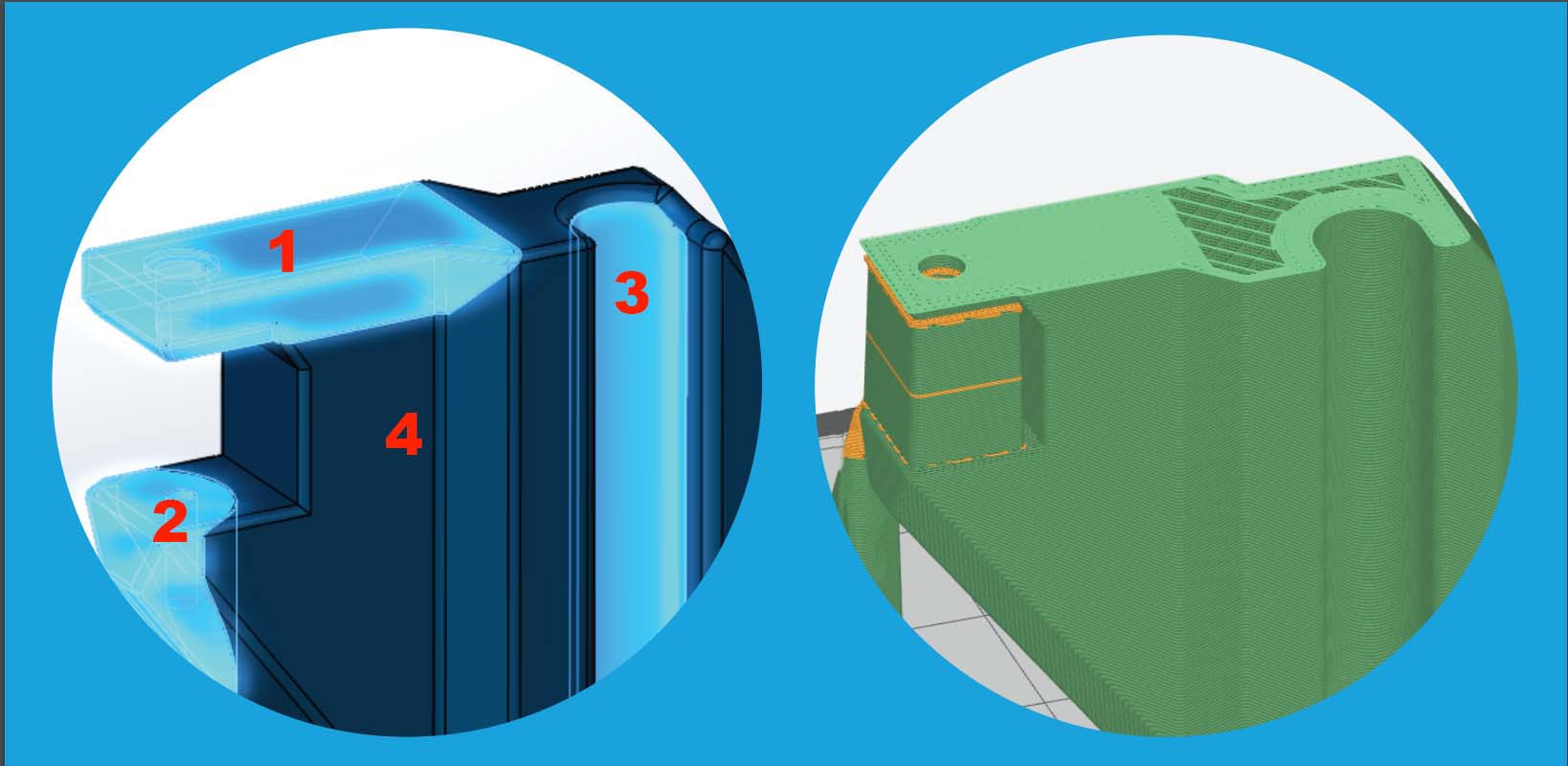
Finally, engineers and designers hold functional control over the part they’re constructing. Now, users can locally add thickness to whichever selected faces that could potentially require reinforcement and have region-specific density, shell thickness and infill styles. This is beneficial in circumstances where parts that require internal reinforcement or additional shell thickness, without having to build a completely solid part, leading to reduced material usage, part weight and build times, all while maintaining structural and functional integrity.
Take 3D Printing to the Next Level
Book a demo with our 3D printing experts and see what’s possible when software and industry leading additive technology come together.