FDM 3D Printing Technology Overview
Fused Deposition Modeling (FDM) systems and related technologies are the most accessible and widely used form of 3D printing. FDM machines build parts layer-by-layer from the bottom up by heating and extruding thermoplastic filament. The production-grade thermoplastic material used is suitable for detailed functional prototypes, durable manufacturing tools & low-volume manufacturing parts.
Different industries require different solutions to maximize the efficiency of their objective. FDM 3D printing technology builds durable and functional prototypes that can withstand rigorous testing.
How FDM 3D Printing Technology Works
FDM 3D printing technology works by extruding heated thermoplastic material layer-by-layer onto a build tray.
- Pre-Processing: Build-preparation software slices and positions a 3D CAD file and calculates a path to extrude thermoplastic and any necessary support material.
- Production: The 3D printer heats the thermoplastic to a semi-liquid state and deposits it in ultra-fine beads along the extrusion path. Where support or buffering is needed, the 3D printer deposits a removable material that acts as scaffolding.
- Post-processing: The user breaks away support material or dissolves it in detergent and water- then the part is ready to use.
Benefits of FDM 3D Printing
FDM technology uses thermoplastics found in traditional manufacturing processes and are ideal for applications that demand tight tolerances, toughness, and environmental stability.
- Technology is well-developed, clean, simple-to-use, and office-friendly
- Supported production-grade thermoplastics are mechanically and environmentally stable
- Complex geometries and cavities that would otherwise be problematic become practical with FDM technology
FDM 3D Printing Materials
With FDM 3D printed thermoplastic filament, you can achieve specialized properties like toughness, electrostatic dissipation, translucency, bio-compatibility, UV resistance & high heat deflection. This allows FDM technology to be suitable for a range of applications from classroom projects to lightweight duct work on commercial aircraft.
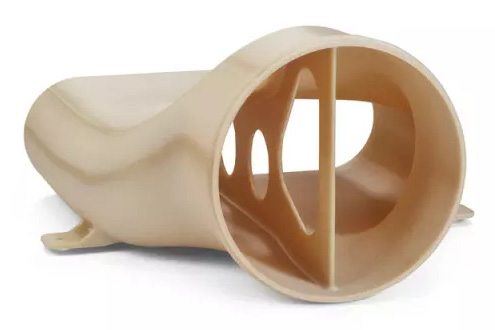
ULTEM™ 9085
Certified for High Performance & FST
ULTEM™ 9085 resin filament is a PEI (polyetherimide) thermoplastic FDM material. It features a high strength-to-weight ratio and high thermal and chemical resistance.
Full Description
ULTEM™ 9085 resin CG meets stringent test criteria and retains traceability required by the aerospace industry as well as railway industry standards for flame, smoke, and toxicity (FST) characteristics.
Available colors: natural ad black.
Specs
-
- Ultimate Tensile Strength: 69 MPa (9950 PSI)
- Heat Deflection Temperature:153℃ (307℉)
Application
- Rapid prototyping
- Tooling
- Production parts
- Aerospace interior components
- FST-rated components
Technology/Process
- Fused Deposition Modeling (FDM)
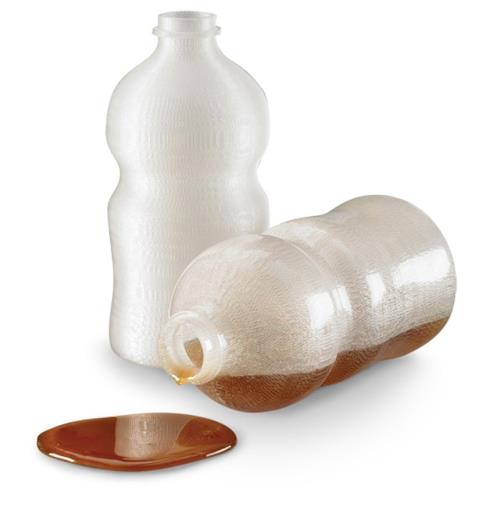
ABSi
Translucent Prototypes with ABSi 3D Printing Thermoplastic
Stratasys ABSi™ is an ideal material for conceptual modeling, functional prototyping and direct digital manufacturing. ABSi gives you parts that are visually unique, dimensionally accurate, durable and hold their shape over time.
Full Description
Its strength is superior to standard ABS, and the translucent nature of ABSi is beneficial for monitoring material flow and light transmission, most commonly used for medical and automotive applications.
Available colors: Translucent Amber, Translucent Red and Translucent Natural
Specs
-
- Tensile Strength: 37 MPa (5400 psi)
- Tensile Modulus: 1920 MPa (277,000 psi)
- Glass Transition Temperature (Tg): 116°C (240°F)
- Heat Deflection Temperature (HDT) at 66 psi: 0.125″ unannealed
- Heat Deflection Temeprature (HDT) at 264 psi: 0.125″ unannealed
Application
- Functional Prototyping
- Conceptual Modelling
- Digital Manufacturing
Technology/Process
Fused Deposition Modeling (FDM)
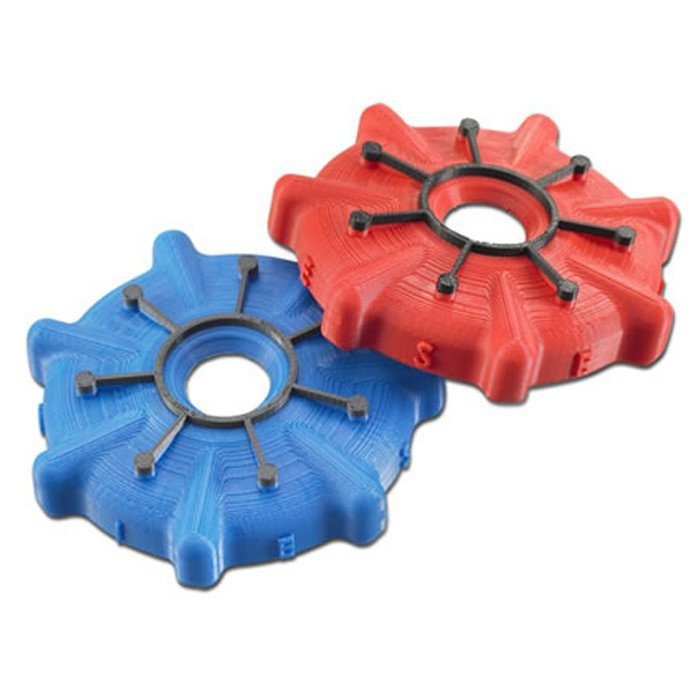
ABSPlus
ABSplus for Mechanical Strength and Available in Many Colors
Stratasys ABSPlus is an FDM thermoplastic with production-grade durability in a wide range of colors for concept modeling and rapid prototyping. It has stability over time, therefore, it can also be used for production parts.
Full Description
ABSPlus is a versatile and tough 3D printing material, resistant to impact due to its strong and durable characteristics. 3D printed parts with this thermoplastic require hands-free soluble support.
Available in 9 colors:
- white
- ivory
- black
- dark grey
- dark blue
- red
- fluorescent yellow
- nectarine
- olive
Specs
- Tensile Strength, Yield: 31 MPa
- Tensile Modulus: 2200 MPa
- Heat Deflection Temperature (HDT) at 66 psi: 96℃
- Impact Toughness: IZOD Impact, notched, 106 J/m XZ axis
Application
- General-purpose prototyping
- Concept models
- Functional prototypes
- Jigs and fixtures
- Production parts
Technology/Process
Fused Deposition Modeling (FDM )
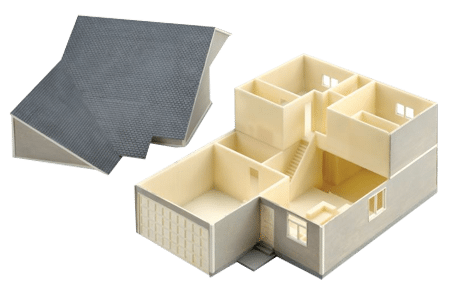
ABS-M30
Suitable for General-Purpose
3D Printing Use Cases
ABS-M30 is up to 25-70% stronger than standard ABS and is ideal for conceptual modeling, functional prototyping, manufacturing tools and end-use parts. Bring your product to market faster with this strong and affordable FDM material.
Full Description
The ABS-M30™ filament combines the design freedom of FDM® technology with the versatility and capability of ABS (acrylonitrile butadiene styrene) which is well-known for its strength and toughness, yet lightweight and resilient.
Features:
- Opaque
- Impact-resistance
- Strong and durable
- Dimensionally stable
- Hands-free support removal
Available in 6 colors:
- ivory
- white
- black
- red
- blue
- dark grey
Specs
- Ultimate tensile strength: 32 MPa
- Izod Unnotched: 7%
- Elongation at Break:
- 300 ohms (electrical resistance)
- 8.1% (XZ orientation) and 1.8% (ZX orientation)
Application
- General-purpose prototyping
- Concept models
- Functional prototypes
- Jigs and fixtures
- Production parts
Technology/Process
Fused Deposition Modeling (FDM)
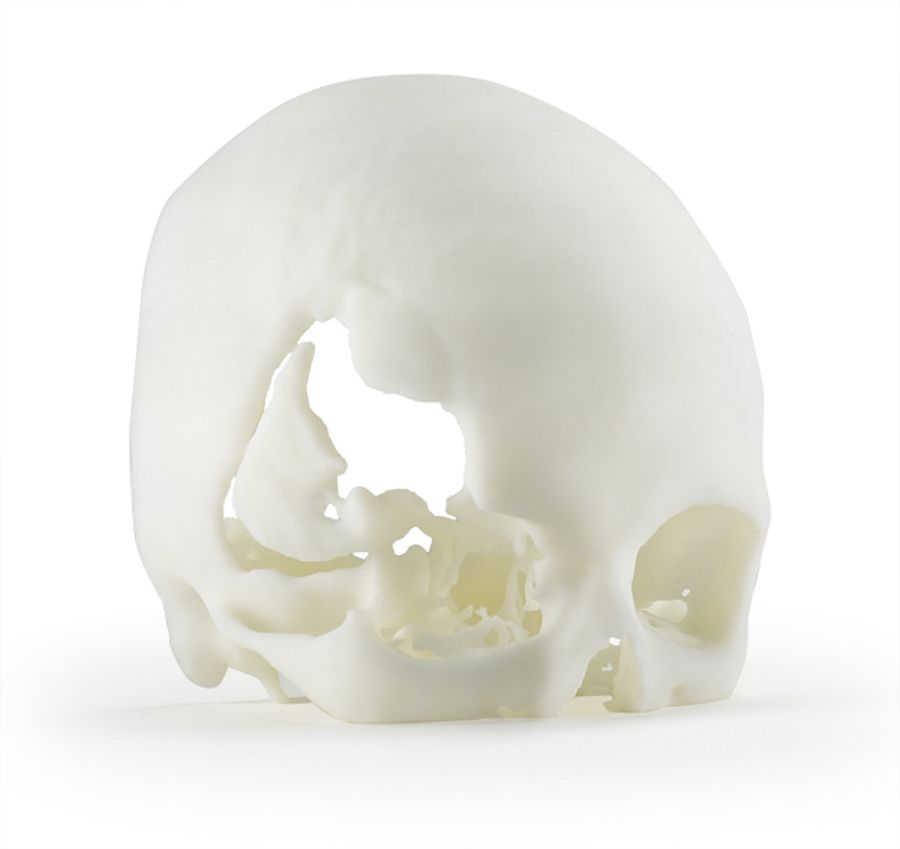
ABS-M30i
Biocompatible FDM material
ABS-M30i is a high-strength material well suited for the medical, pharmaceutical, and food packaging industries. Parts manufactured with ABS-M30i are biocompatible (ISO 10993 USP Class VI)* and can be gamma or EtO (Ethylene Oxide Processing) sterilized.
Full Description
Characteristics:
- Biocompatible
- Opaque
- Strong and durable
- Impact-resistant
- Dimensionally stable
- Accurate, reliable functional testing
Specs
- Tensile Strength: 31 MPa (XZ Axis), 26 MPa (ZX Axis)
- Tensile Modulus: 2180 MPa
- Heat Deflection Temperature (HDT) at 66 psi: 96 °C
- Impact Toughness: IZOD Impact, notched -160 J/m XZ axis
Application
- Medical device components
- Medical or pharmaceutical prototypes
- Functional prototypes
- Jigs and fixtures
- Manufacturing tooling
- Production parts
Technology/Process
Fused Deposition Modeling (FDM)
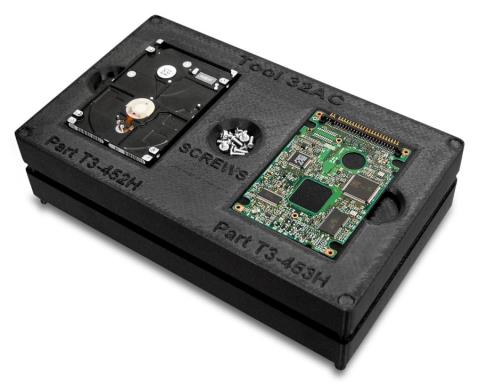
ABS-ESD7
Static-Dissipative ABS Material
ABS-ESD7 is the best FDM printing material for printing with a static-dissipative thermoplastic. It has the strength and durability of the ABS with carbon to provide electrostatic dissipative (ESD) properties.
Full Description
ABS-ESD7 has the strength and durability of the ABS with carbon to provide electrostatic dissipative (ESD) properties.
For applications where a static charge could damage components, impair the performance, or cause an explosion, ABS-ESD7 offers a safe and suitable FDM material for printing. This prevents a build-up of static electricity so that it doesn’t produce a static shock or cause other materials like powders, dust, and fine particles to stick to it.
Specs
- Ultimate Tensile Strength: 35 MPa
- Elongation at Break: 2-3%
- Izod Impact, Notched: 28 J/m XZ axis
- Heat Deflection (HDT) at 264 psi, 0.125″ unannealed: 82℃ or 180℉
- Heat Deflection (HDT) at 66 psi, 0.125″ unannealed: 96℃ or 204℉
- Volume Resistivity (ASTM D257): 3.0 x 109 – 4.0 x 1010 ohm-cm
Application
- Prototypes, Fixtures, and Support Equipment for Electronics:
- End-use components
- Electronic products
- Assemblies of electronic components
- Concept models for prototypes for static-sensitive applications
- Tooling: jigs and fixtures and support tooling used in static-critical fabrication and packaging applications
Technology/Process
Fused Deposition Modeling (FDM)
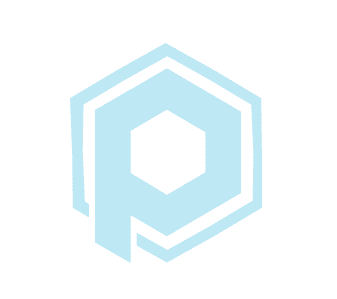
Antero 800NA
High-performance PEKK based material
Stratasys Antero 800NA is a PEKK-based (polyetherketoneketone) thermoplastic 3D printing material that holds outstanding mechanical properties making it ideal for use in aircraft, space and manufacturing applications.
Full Description
FDM Antero™ 800NA gives new opportunities for chemical-resistant 3D printed parts. A majority of thermoplastics tend to fail when they come in contact with fuel, hydraulic fluids, or other chemicals. However, FDM Antero™ 800NA, a PEKK proprietary blend, solves these challenges with excellent mechanical properties and the highest chemical resistance available.
Advantages:
- Excellent mechanical properties
- Design freedom
- Chemical resistance
- Low outgassing properties
- Heat resistance
- Less waste than CNC
- Cost advantages over PEKK
Specs
- Ultimate Tensile Strength (XZ axis): 90 MPa
- Heat Deflection (HDT) at 66 psi, ASTM D648: 163 °C (325.4 °F) – Annealed
- Heat Deflection (HDT) at 264 psi, ASTM D648: 157 °C (314.6 °F) – Annealed
- Glass Transition Temperature (Tg), ASTM D7426-08: 151 °C (303.8 °F)
Application
For aircraft components exposed to jet fuel, oil and hydraulic fluid, spacecraft parts that demand low outgassing and chemical-resistant industrial parts.
- Prototyping
- Tooling
- Production Parts
- Aircraft, Space, and Manufacturing Applications
Technology/Process
Fused Deposition Modeling (FDM)
FDM Technical Specifications
Maximum Accuracy |
Maximum Accuracy0.18-0.25mm |
Layer Resolution |
Layer Resolution0.007 in - 0.020 in |
Minimum Wall Thickness |
Minimum Wall Thickness1mm |
Maximum Part Dimensions (Single Build) |
Maximum Part Dimensions (Single Build)914 x 610 x 914 mm(36 x 24 x 36 in) |
Finishes |
FinishesAdvanced finishing options available like smoothing, painting and sanding. |
FDM 3D Printers
Idea Series
Develop your ideas with affordable models and prototypes. Idea Series 3D Printers fit your desktop and your budget.
Design Series
Perfect your designs with strong, durable and dimensionally-stable parts that withstand tough testing.
Production Series
Bring agility and aesthetics to every stage of product development with the widest range of colors and material properties for prototypes and tooling.